In today’s rapidly advancing industrial landscape, precise and efficient measurement technologies are indispensable. Among these, radar level measurement stands out for its exceptional performance, particularly in measuring liquid levels within distillation tanks. Its unique advantages have revolutionized this area of industrial measurement.
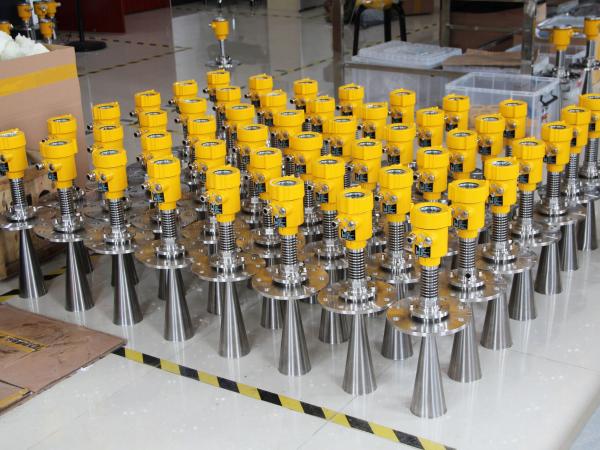
Importance of Level Measurement in Distillation Processes
Distillation is a critical process in chemical engineering, where the accurate control of liquid levels directly impacts the purity and yield of products. Traditional level measurement methods, such as float-type and pressure-based systems, have been used for years to meet production requirements. However, these methods often face challenges under extreme conditions. For instance, float-type level sensors are affected by changes in the medium’s density, while pressure-based systems struggle to maintain accuracy in high-temperature and high-pressure environments.
Radar level measurement has introduced a groundbreaking solution to these challenges. It employs time-domain reflectometry of electromagnetic waves, allowing it to penetrate through steam, foam, and other media to measure the liquid level with precision. This technology is unaffected by factors such as temperature, pressure, and density, making it ideal for the dynamic and often complex environments of distillation tanks. Compared to traditional methods, radar level measurement not only enhances accuracy and reliability but also significantly reduces maintenance costs and workload.
Performance in Challenging Conditions
Distillation processes are often accompanied by rapid temperature changes, pressure fluctuations, and varying media. These factors place high demands on the performance of level sensors. Radar level measurement’s resilience to high temperatures and pressures allows it to function consistently under harsh conditions. Additionally, its adaptability to different dielectric constants ensures that no recalibration is required when switching between different media, greatly improving operational efficiency.
Ease of Installation and Remote Monitoring
Another advantage of radar level measurement lies in its ease of installation and commissioning. With a versatile flange design, the sensor can be easily installed on the top of a distillation tank without requiring specific openings, simplifying the installation process. Moreover, by utilizing HART or PROFIBUS PA communication protocols, remote setup and monitoring become possible, providing strong support for automated process control.
Challenges and Future Prospects
Despite the numerous advantages radar level measurement brings to distillation tank operations, some challenges remain. For example, in environments with excessive dust or crystallization, radar wave attenuation may affect measurement accuracy. Additionally, the high cost of radar systems limits their widespread adoption, particularly among smaller enterprises. However, as technology continues to advance and costs gradually decrease, these challenges are expected to be overcome, paving the way for broader use of radar level measurement in various industrial applications.
In conclusion, radar level measurement has significantly improved the accuracy, reliability, and efficiency of liquid level monitoring in distillation processes. As the technology evolves and becomes more affordable, its potential will only continue to grow, further transforming industrial measurement practices.