Introduction
A resistance temperature detector (RTD) is a sensor that measures temperature based on the principle that its electrical resistance changes with temperature. Specifically, it utilizes the property of metal conductors or semiconductors where the resistance value varies with temperature. By measuring the change in resistance, the temperature can be calculated.
RTDs are among the most commonly used temperature detectors in the low to medium temperature range, known for their high measurement accuracy and stable performance. Most RTDs are made from pure metal materials, with platinum and copper being the most commonly used. Additionally, materials like nickel, manganese, and rhodium are also being used in the production of RTDs.
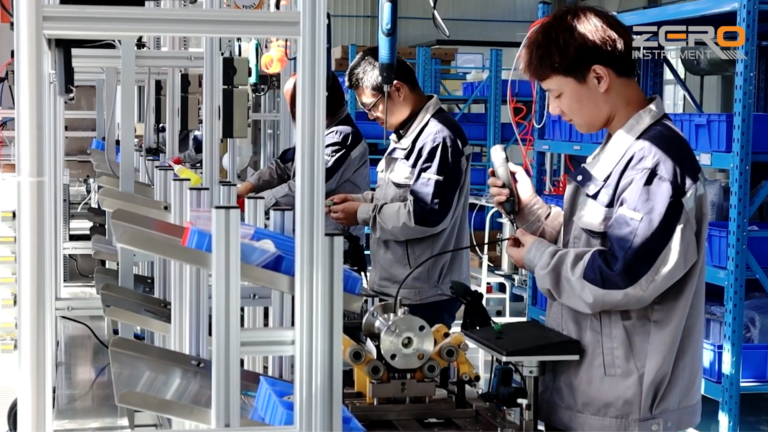
Main Characteristics of Resistance Temperature Detectors (RTDs):
High Measurement Accuracy: RTDs provide precise temperature measurements, making them suitable for applications requiring accurate temperature control.
Stable Performance: RTDs are known for their long-term stability, ensuring consistent and reliable temperature readings over time.
Wide Temperature Range: RTDs can measure a broad range of temperatures, especially in the low to medium temperature range, making them versatile for various industrial applications.
Good Linearity: The resistance change of RTDs with temperature is relatively linear, simplifying the conversion from resistance to temperature in measurement systems.
Durability: RTDs are generally robust and can withstand harsh environments, which contributes to their longevity and reliability in industrial settings.
Material Versatility: RTDs can be made from a variety of materials, including platinum, copper, nickel, and other metals, each offering different advantages depending on the application.
Interchangeability: Due to standardized manufacturing processes, RTDs can often be replaced without significant recalibration, making them convenient for maintenance and replacement.
Working Principle of Resistance Temperature Detectors (RTDs):
The working principle of a resistance temperature detector (RTD) is based on the predictable change in electrical resistance of certain materials as their temperature changes. Specifically, as the temperature of the RTD sensor increases, the resistance of the metal element inside the sensor also increases. This relationship between temperature and resistance is typically linear over a wide range of temperatures.
Here’s how it works:
Material Selection: RTDs are usually made from pure metals like platinum, copper, or nickel, which have a known and consistent change in resistance with temperature. Platinum is the most commonly used material due to its high stability and repeatability.
Temperature-Resistance Relationship: The metal element within the RTD exhibits a specific resistance at a given temperature. As the temperature increases, the resistance of the metal increases proportionally. This change in resistance is used to determine the temperature.
Measurement Process: The RTD sensor is connected to a measurement circuit, typically a Wheatstone bridge or a similar setup, that can accurately measure the resistance of the RTD. As the temperature changes, the resistance of the RTD changes, causing a corresponding change in the voltage or current in the circuit.
Temperature Calculation: The measured resistance is then converted to a temperature reading using a calibration equation or a standard reference table, such as the Callendar-Van Dusen equation for platinum RTDs.
Output: The temperature reading is displayed or used in a control system for monitoring or regulating the process in which the RTD is installed.
This principle allows RTDs to provide highly accurate and repeatable temperature measurements, making them widely used in industrial, scientific, and medical applications.
Main Types of Resistance Temperature Detectors (RTDs):
Platinum RTDs (Pt100, Pt1000, etc.):
- Pt100: The most common type, where the RTD has a resistance of 100 ohms at 0°C. It is widely used due to its excellent stability, repeatability, and accuracy over a broad temperature range (-200°C to 850°C).
- Pt1000: Similar to Pt100 but with a resistance of 1000 ohms at 0°C, offering higher sensitivity and often used in applications where lead wire resistance may affect measurements.
Copper RTDs (Cu10, Cu50, Cu100):
- Cu10: Has a resistance of 10 ohms at 0°C. Copper RTDs are commonly used in lower temperature applications (-50°C to 150°C) due to their good linearity and lower cost.
- Cu50, Cu100: Higher resistance variants, used in similar applications but with varying sensitivity and accuracy.
Nickel RTDs (Ni100, Ni120):
- Ni100: Nickel RTDs have a resistance of 100 ohms at 0°C. They offer good sensitivity but are less accurate and have a narrower temperature range compared to platinum RTDs (-60°C to 180°C).
- Ni120: Similar to Ni100 but with a slightly different temperature coefficient, providing an alternative for specific applications.
Wire-Wound RTDs:
- Made by winding a thin wire of platinum, copper, or nickel around a ceramic or glass core. Wire-wound RTDs offer high accuracy and stability, especially at higher temperatures, but they are more delicate and expensive.
Thin-Film RTDs:
- These are manufactured by depositing a thin layer of platinum onto a ceramic substrate. Thin-film RTDs are more robust, cost-effective, and have a faster response time than wire-wound RTDs, making them suitable for industrial applications.
Surface-Mounted RTDs:
- Designed to measure the temperature of surfaces, these RTDs can be attached directly to a surface, providing accurate readings without the need for insertion into the material being measured.
Coiled RTDs:
- A variation of wire-wound RTDs where the wire is wound in a coil and suspended in a protective sheath. This design allows for expansion and contraction of the wire with temperature changes, improving accuracy and reducing strain.
Each type of RTD is selected based on the specific requirements of the application, including the temperature range, required accuracy, response time, and environmental conditions.
Wiring Configurations of Resistance Temperature Detectors (RTDs):
RTDs can be connected using different wiring configurations, each with its own advantages depending on the accuracy requirements and the length of the connecting wires. The most common wiring methods are:
Two-Wire Configuration:
Description: In this simplest configuration, two wires connect the RTD element to the measuring instrument. One wire carries the excitation current, and the other measures the voltage drop across the RTD.
Advantages: Simple and cost-effective, requiring minimal wiring.
Disadvantages: Lead wire resistance is not compensated, which can introduce errors, especially in applications with long lead wires or where high accuracy is needed.
Typical Use: Used in applications where high precision is not critical or where the lead wires are short.
Three-Wire Configuration:
Description: This configuration adds a third wire, which is connected to one end of the RTD. The measuring instrument uses the third wire to compensate for the resistance of the lead wires, reducing the error caused by lead resistance.
Advantages: Provides a good balance between accuracy and cost. Compensates for lead wire resistance, making it suitable for most industrial applications.
Disadvantages: Some residual error may remain, especially if the lead wires are not identical in resistance.
Typical Use: Commonly used in industrial applications where lead wire resistance needs to be minimized, but the highest level of accuracy is not required.
Four-Wire Configuration:
Description: This configuration uses four wires, with two wires carrying the excitation current and the other two measuring the voltage drop across the RTD. This setup completely eliminates the effect of lead wire resistance.
Advantages: Provides the highest accuracy by fully compensating for lead wire resistance. Ideal for precise temperature measurements.
Disadvantages: More complex and expensive due to the additional wiring and instrumentation requirements.
Typical Use: Used in laboratory settings, calibration applications, and other situations where the highest accuracy is required.
Six-Wire Configuration:
Description: This rare configuration is an extension of the four-wire configuration, where two additional wires are used for redundancy or to measure the temperature at different points on the RTD element.
Advantages: Provides enhanced accuracy and reliability, particularly in critical applications where redundancy or detailed profiling is needed.
Disadvantages: Complex, costly, and typically used only in specialized applications.
Typical Use: Applied in highly specialized scientific or industrial processes requiring redundancy or temperature profiling.
Application Areas of Resistance Temperature Detectors (RTDs):
Industrial Process Control:
- Description: RTDs are widely used in industrial settings for monitoring and controlling the temperature of processes, such as in chemical plants, refineries, and manufacturing facilities.
- Typical Applications: Monitoring reactors, distillation columns, pipelines, and storage tanks.
HVAC Systems:
- Description: RTDs are used in heating, ventilation, and air conditioning (HVAC) systems to ensure accurate temperature control and energy efficiency.
- Typical Applications: Temperature regulation in air handling units, ductwork, and building automation systems.
Automotive Industry:
- Description: In the automotive industry, RTDs are used to monitor the temperature of various engine components and exhaust systems, contributing to efficient engine management and emission control.
- Typical Applications: Engine coolant temperature sensors, exhaust gas temperature sensors, and battery management systems.
Aerospace:
- Description: RTDs are employed in aerospace applications to monitor critical temperatures in aircraft engines, avionics, and environmental control systems.
- Typical Applications: Monitoring temperatures in jet engines, avionics cooling systems, and spacecraft temperature control.
Medical Devices:
- Description: RTDs are used in medical equipment for precise temperature measurement, which is essential in patient care and laboratory diagnostics.
- Typical Applications: Incubators, blood analyzers, medical imaging equipment, and patient monitoring systems.
Food and Beverage Industry:
- Description: RTDs are crucial in the food and beverage industry for ensuring proper cooking, storage, and processing temperatures to meet safety and quality standards.
- Typical Applications: Monitoring pasteurization processes, fermentation temperatures, and refrigeration systems.
Power Generation:
- Description: In power plants, RTDs are used to monitor the temperature of critical components, ensuring safe and efficient operation.
- Typical Applications: Monitoring turbine temperatures, generator windings, and boiler temperatures.
Research and Development:
- Description: RTDs are used in laboratories and research institutions for precise temperature measurements in experiments and testing.
- Typical Applications: Scientific experiments, material testing, and environmental testing chambers.
Energy and Environmental Monitoring:
- Description: RTDs are used to monitor environmental conditions and energy systems, contributing to the efficient management of resources.
- Typical Applications: Monitoring solar panel temperatures, wind turbine components, and environmental monitoring stations.
Semiconductor Manufacturing:
- Description: RTDs are used in the semiconductor industry to monitor the temperature during the production of integrated circuits and other electronic components.
- Typical Applications: Temperature control in wafer fabrication processes, chemical vapor deposition, and etching processes.
RTDs are chosen in these applications due to their accuracy, stability, and ability to operate over a wide range of temperatures, making them versatile tools in various industries where precise temperature measurement is critical.