Alkaline electrolyzer is an important chemical production equipment, which is used to produce products such as sodium hydroxide, chlorine, and hydrogen.
Liquid level measurement is crucial in the chemical production process, and a radar level meter is an advanced liquid level measurement equipment, which has significant advantages in measuring liquid levels in alkaline electrolyzers.
In this paper, we will introduce the characteristics of the alkaline electrolyzer and provide actual measurement cases to demonstrate the application of a radar level meter in an alkaline electrolyzer.
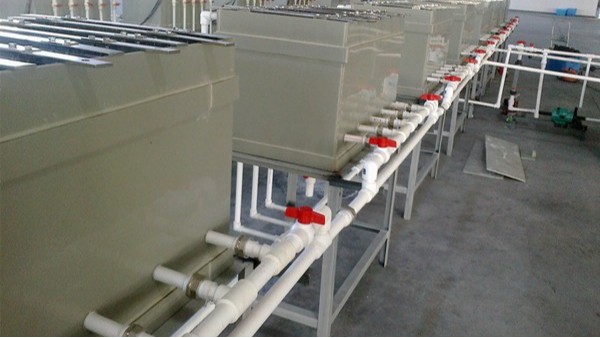
Characteristics of an alkaline electrolyzer An Alkaline electrolyzer is an important industrial equipment, its level measurement faces the following characteristics and difficulties: Liquid nature: in chemical production, the liquid commonly used in electrolyzer is strong alkaline liquid, corrosive and explosive.
High temperature: alkaline electrolyzer working temperature is high, generally in 80-100 ℃, the working environment of the level measurement equipment puts forward higher requirements.
Complex tanks: Alkaline electrolyzer tanks are complex, and the liquid level measurement position is usually not easy to measure.
Below are two actual measurement cases to demonstrate the application of radar level meter in alkaline electrolyzer.
Case 1: Sodium Hydroxide Manufacturer A sodium hydroxide manufacturer located in Asia was faced with a level measurement problem.
The original level measurement equipment had huge leakage and false alarm problems. In order to do so, the manufacturer adopted radar level meter for liquid level measurement.
The radar level meter can penetrate the sodium hydroxide material, accurately measure the liquid level height in the electrolyzer, and adapt to the complex working environment to provide accurate liquid level data.
At the same time, the radar level meter has the characteristics of high temperature resistance and corrosion resistance, and has long time stability and reliability, which greatly improves the production efficiency and product quality, and helps the manufacturer to realize the goal of energy saving and emission reduction.
Case 2: Chemical plant A chemical plant located in North America involves liquid mixing and warming in the production process, which requires liquid level monitoring.
However, traditional level measurement devices such as fluorescent level meters have difficulty accurately measuring the level height in highly corrosive liquids.
To solve the problem, the plant uses radar level meters for liquid level measurement.
The radar level meter can measure corrosive liquids stably and work properly even under extreme conditions, such as high temperature, long retention time, and liquid evaporation, which ensures the stability and accuracy of liquid level monitoring and greatly reduces the risk of safety accidents and improves the productivity and safety of the plant.
The characteristics of alkaline electrolysis tanks and the difficulties in level measurement are real problems, but the radar level meter has the characteristics of corrosion resistance, high temperature, and high pressure, which can measure the liquid level height stably and accurately.
At the same time, the radar level meter can also cope with the complexity of the electrolyzer tank, the measurement position is not easy to access and other issues, greatly improving the precision and stability of the liquid level measurement.