Introduction
Ultrasonic liquid level meters operate based on the propagation characteristics of ultrasonic waves in a given medium. These devices determine the distance between the sensor and the liquid surface by measuring the time difference between the emission and reception of an ultrasonic pulse. This time delay is then used to calculate the liquid level height.
The core components of an ultrasonic liquid level meter include an ultrasonic transducer probe, an electronic control unit, and a display/output interface. The ultrasonic transducer functions as both an emitter and a receiver, sending high-frequency pulse waves toward the liquid surface and detecting the returning echo. The electronic control unit manages the transmission and reception processes, processes the acquired signals, and ultimately calculates the liquid level.
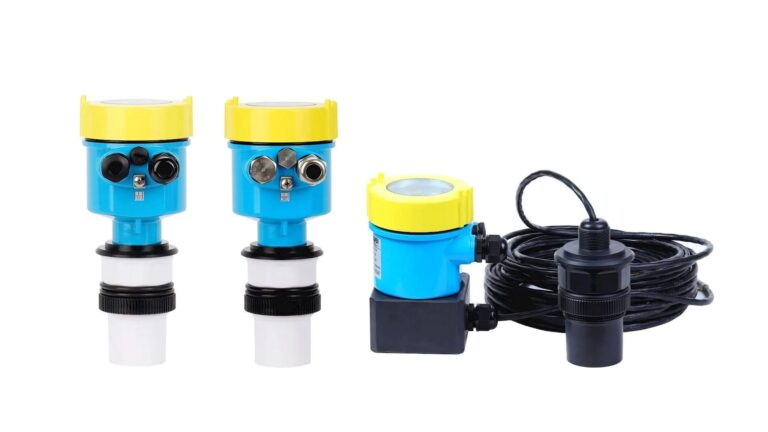
Principle of Ultrasonic Liquid Level Measurement
The fundamental equation governing ultrasonic liquid level measurement is:
where:
S is the distance from the sensor to the liquid surface,
C is the speed of sound in the medium (air),
T is the time taken for the sound wave to travel to the liquid surface and back.
This formula assumes that the speed of sound in air remains constant. However, in real-world conditions, the speed of sound is highly sensitive to temperature variations. Under standard atmospheric pressure (101.3 kPa), the speed of sound in air at 20°C is approximately 343 m/s. The speed of sound increases by approximately 0.607 m/s per 1°C rise in temperature.
If temperature variations are ignored, the calculated distance may deviate significantly, leading to substantial measurement errors. Thus, implementing temperature compensation is essential to ensure measurement accuracy.
The Role of Temperature Compensation in Ultrasonic Liquid Level Measurement
Temperature compensation plays a crucial role in minimizing measurement errors caused by temperature-induced variations in sound speed. Without compensation, ultrasonic liquid level meters operating in environments with fluctuating temperatures may exhibit considerable inaccuracies.
For example, in industrial applications such as wastewater treatment plants, chemical storage tanks, and industrial reservoirs, temperature fluctuations are common. If the sound speed is assumed to be a constant value, the resulting level measurements can be significantly distorted, leading to improper control decisions or operational inefficiencies.
By integrating temperature compensation, ultrasonic liquid level meters dynamically adjust the sound speed parameter based on real-time temperature readings, ensuring high precision in liquid level determination.
Implementation of Temperature Compensation
Temperature compensation in ultrasonic liquid level meters is generally achieved through the following steps:
Incorporating a Temperature Sensor
A temperature sensor (e.g., a thermistor or RTD) is embedded within the ultrasonic transducer probe to measure the ambient air temperature in real-time.
Converting Temperature Data into Electrical Signals
The temperature sensor converts the detected temperature into an electrical signal, which is sent to the microcontroller or processing unit of the ultrasonic level meter.
Comparison of Temperature Compensation Techniques
Different methods can be used to implement temperature compensation in ultrasonic level measurement:
Embedded Temperature Sensor Method (Most Common)
Uses an internal temperature sensor to adjust sound speed dynamically.
Offers high accuracy and real-time correction.
Suitable for industrial applications where temperature variations are frequent.
Predefined Look-Up Table Method
Uses a pre-calibrated temperature-sound speed table.
Less flexible for real-time compensation but effective for controlled environments.
Dual-Wave Frequency Compensation
Uses two ultrasonic waves at different frequencies to determine sound speed variations.
More complex but improves measurement stability in extreme conditions.
Applications of Temperature-Compensated Ultrasonic Liquid Level Meters
Temperature compensation is widely applied in industries where precision liquid level measurement is critical:
Wastewater Treatment Plants: To monitor and regulate water levels in treatment tanks.
Chemical Processing Facilities: To ensure safe storage of volatile or reactive liquids.
Food and Beverage Industry: To maintain consistent fluid levels in production lines.
Oil and Gas Storage Tanks: To improve measurement reliability in outdoor environments.
Pharmaceutical Manufacturing: To ensure compliance with strict quality control standards.
Conclusion
Temperature compensation is an essential enhancement in ultrasonic liquid level measurement, significantly improving measurement precision by dynamically adjusting for sound speed variations due to temperature fluctuations. The implementation of temperature sensors within the ultrasonic transducer allows real-time correction, ensuring accuracy even in environments with fluctuating temperatures.
By incorporating temperature compensation techniques, industries can achieve more reliable liquid level monitoring, reduce measurement errors, and optimize process control. As ultrasonic level sensing technology continues to evolve, more sophisticated compensation methods may emerge, further enhancing measurement accuracy in challenging conditions.