A mixing tank is a common reaction device used in various industries such as chemical, pharmaceutical, and food processing. Through its internal mixing mechanism, materials are evenly mixed, dissolved, or reacted. However, due to the often complex working conditions inside the tank—such as fluctuations caused by stirring, foam, and high viscosity—measuring the material level poses significant challenges.
Radar level meters, with their advantage of non-contact measurement, have become one of the effective tools to address this issue. Nevertheless, there are still some difficulties that cannot be overlooked when using radar level meters to measure the level in a mixing tank.
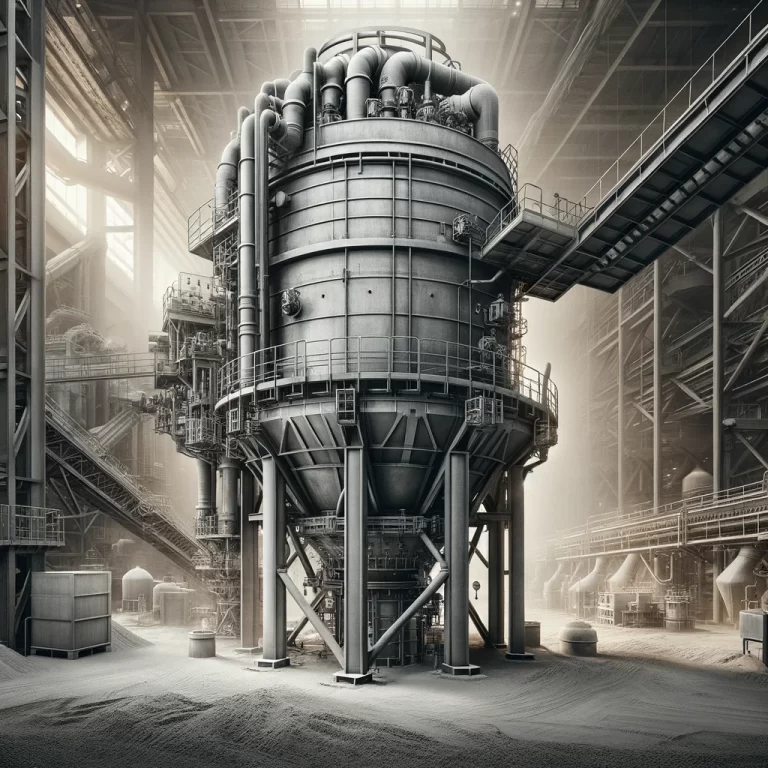
The primary challenge lies in the impact of the agitator itself. During operation, the agitator causes surface fluctuations, which interfere with the propagation path of radar waves, leading to deviations in the reflected signal. This interference becomes especially pronounced when the agitator blades are large or rotating at high speeds, significantly compromising the stability and accuracy of level measurement.
Additionally, if the agitator contains metal components, it can directly reflect radar waves, further affecting the measurement results. Therefore, how to reduce the impact of the agitator on level measurement while maintaining stirring efficiency is an issue that requires in-depth research and solutions.
Foam presence is another major challenge. In many industrial processes, especially in chemical reactions or fermentation, foam generation is almost inevitable. Foam not only covers the liquid surface but also scatters radar waves due to its varying sizes and irregular shapes, severely affecting the accuracy of level measurement.
Even more troublesome is the fact that foam generation and dissipation are often dynamic, requiring radar level meters to have a high refresh rate and sensitivity to capture the true level information.
The characteristics of the material are also an important factor that cannot be ignored. High-viscosity media, highly corrosive chemicals, and environments with large temperature variations all place higher demands on the performance of radar level meters. For example, high-viscosity media can easily adhere to the probe, affecting the transmission and reception of signals.
Highly corrosive chemicals may challenge the materials used in the instrument, requiring special corrosion-resistant materials to ensure long-term stable operation. Additionally, temperature fluctuations can affect the speed of radar wave propagation, thereby impacting the accuracy of the measurement results. This necessitates the radar level meter to have a temperature compensation function to adapt to different working conditions.
The choice of installation location is another important factor that affects measurement accuracy. The ideal installation location should minimize interference and ensure effective signal transmission. However, in practical applications, it is often difficult to find a perfect location due to on-site constraints.
For instance, installing the radar at the top of a mixing tank may be affected by the flange edges, while side installation could be subject to interference from reflections off the container walls. Therefore, selecting the optimal installation location based on actual site conditions is an art that requires rich experience and skill.
The main challenges faced by radar level meters when measuring mixing tanks include the influence of the agitator, the presence of foam, the challenges posed by material characteristics, and the selection of the installation location.
To address these difficulties, in addition to continuously optimizing the design and performance of radar level meters, it is essential to conduct detailed analysis and adjustments based on the actual working conditions.
By making appropriate selections, scientifically installing the equipment, and performing effective maintenance, these challenges can be overcome to the greatest extent possible, ensuring the accuracy and reliability of level measurement.