Problem Definition:
Oscillation in control systems typically indicates a problem in the control loop. In the case of level control, we are dealing with oscillation caused by improper PID parameters and insufficient material input. Specifically, in a level control system where the discharge flow is used to control the liquid level, inadequate material input coupled with misconfigured PID parameters can lead to persistent oscillation. In this scenario, the control valve oscillates between fully closed and some intermediate output value.
To address this, process personnel first attempted to limit the controller’s output range to [-5, 3], and then further reduced it to [-5, 1]. By limiting the control output and changing the constraints, the automatic control system could operate correctly. This approach is often employed by process engineers and operators to ensure smooth system performance.
The key to solving oscillation problems is simplicity. The goal is to make the control loop work automatically without requiring excessive manual intervention. Common methods to achieve this include modifying process setpoints, adjusting upstream or downstream parameters, altering operational ranges, or even changing the equipment. Advanced control strategies are effective, but operators still focus mainly on adjusting ranges to keep the system functioning. The advantage of advanced control is the flexibility to modify these ranges at any time.
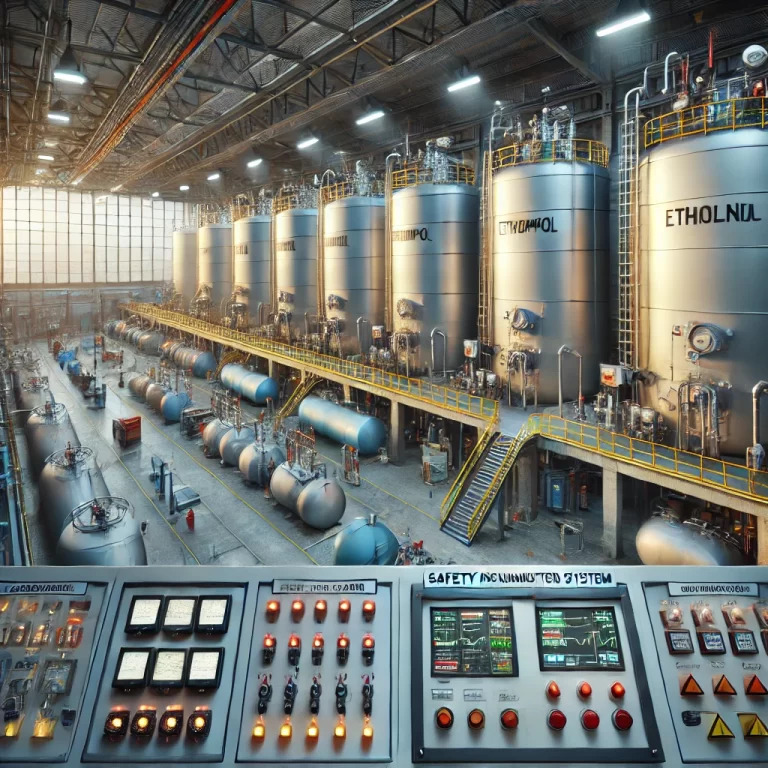
PID Parameter Adjustment:
For control engineers, simply limiting the output range is not a fundamental solution. From the response curve, we can see that when the controller output reaches its maximum, the process variable (PV) is near the setpoint. As the system in question is an integrator, the oscillation is caused by excessive integral action, leading to phase mismatch.
To resolve the oscillation, the PID parameters were adjusted. Initially, the parameters were set at 1/2.5/0, but this led to significant oscillation. The parameters were adjusted further to 1/10/0 and finally to 2/20/0. With each adjustment, the oscillations gradually diminished. This adjustment is critical for reducing wear on control valves caused by excessive oscillations and helps achieve continuous discharge.
During winter, when continuous discharge was not possible due to freezing concerns, heating cables were added to prevent pipeline freezing. This demonstrates how modifying PID parameters can address not only the oscillations but also seasonal operational challenges.
Root Cause Analysis and Solutions:
Once oscillation is observed, it’s important to perform a root cause analysis to identify the underlying issue. While limiting the controller output is a quick and common method, it’s a temporary solution that doesn’t address the root cause. If the oscillation is caused by phase mismatch, increasing the integral time to reduce the integral action can effectively resolve the issue. For phase-matched oscillations, additional steps depend on the specific situation:
If PV is a square wave and OP is a sawtooth wave, the cause is nonlinear actuator behavior. In this case, the actuator should be repaired or replaced.
If phase-matched oscillations occur without regularity, it is likely due to inadequate proportional control. In this scenario, increasing the proportional gain will usually resolve the issue.
If phase-matched oscillations are regular, and manual control eliminates the oscillation, the issue can be resolved by reducing the proportional gain.
If phase-matched oscillations are regular, and manual control increases the oscillation amplitude, external interference is likely the cause. In such cases, identifying and eliminating the source of interference is necessary.
Advanced Control Considerations:
For control engineers, solving oscillations through PID adjustments is just one part of the solution. Advanced control offers the ability to modify the model and parameters on the fly. This is a significant advantage, as the control system can be continuously optimized based on changing process conditions.
However, even with advanced control systems, the operator’s role remains crucial in adjusting ranges and ensuring the system remains within the desired operating conditions. The flexibility of advanced control systems should not overshadow the importance of basic operational adjustments.
Conclusion:
The key to resolving oscillations in level control systems lies in understanding the root cause and applying the appropriate solutions. While limiting control output can provide a quick fix, adjusting PID parameters and considering advanced control strategies offer more permanent solutions. Ultimately, the ability to modify parameters and adapt to changing process conditions is crucial for maintaining stable operation and preventing unnecessary wear on equipment.