Pressure transmitters are essential instruments in modern industrial automation, responsible for converting pressure signals into standardized electrical outputs that can be used for process control and monitoring. However, they often operate in complex and dynamic environments, where pressure spikes can pose serious threats to sensor integrity. This article explores the structural design of pressure transmitters, their protective damping features, and recommended installation practices for harsh working conditions.
1. Construction and Working Principle of Pressure Transmitters
A typical industrial pressure transmitter integrates an isolated silicon piezoresistive sensing element encased within a stainless-steel housing. When pressure is applied by a fluid or gas, the sensing diaphragm deforms, and the embedded piezoresistive elements change resistance proportionally. This change is converted into a standard electrical signal, such as 4–20 mA or 0–10 V, which is then transmitted to a control system.
This conversion allows the transmitter to serve as a reliable interface between mechanical pressure and electronic data acquisition systems.
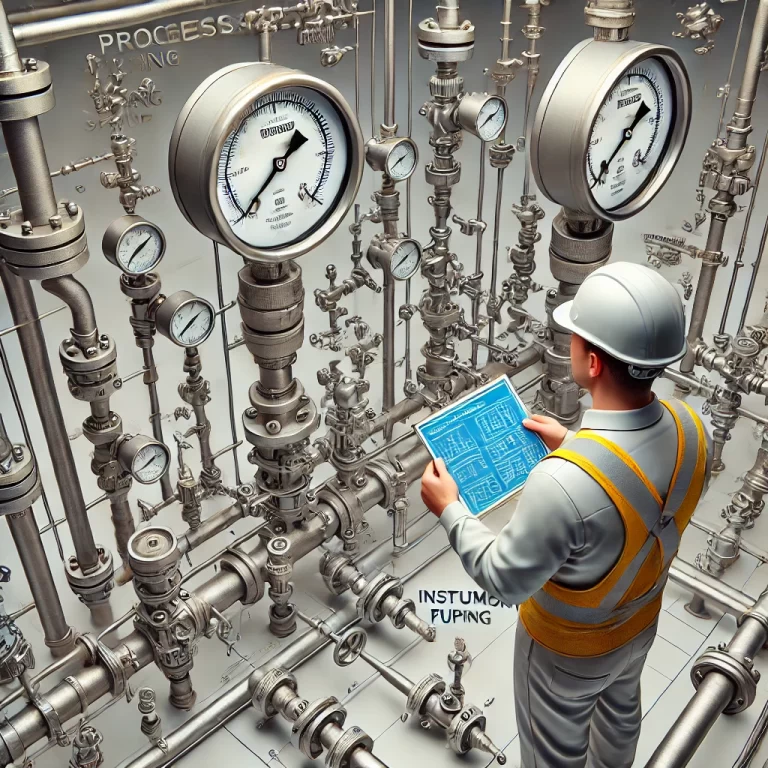
2. Common Applications
Pressure transmitters are widely used across various industries and equipment types, including:
Hydraulic and pneumatic boosters
Gas-liquid intensifiers and booster cylinders
Pressing machines and compressors
HVAC and refrigeration systems
Their ability to operate under diverse conditions makes them integral to both process monitoring and safety interlocks.
3. The Problem of Sudden Pressure Spikes
In industrial processes, sudden and extreme pressure fluctuations—commonly referred to as shock or surge pressure—are not uncommon. These can occur due to:
Valve operations (e.g., sudden closing or opening)
Pump startups or malfunctions
Gas/liquid hammer effects
Such conditions may cause instantaneous overpressure, which can severely damage the transmitter’s sensitive core, rendering it inoperable. The silicon chip or diaphragm can crack or deform beyond recovery if not adequately protected.
4. Role of Damping Mechanisms
To address this challenge, many pressure transmitters are equipped with damping structures designed to buffer sudden pressure changes. Key features include:
A damping screw or insert located at the bottom of the threaded connection port
An internal small orifice or sintered metal filter that limits the rate at which pressure reaches the sensing element
These damping elements help:
Reduce mechanical vibration and resonance amplitude
Absorb shock energy, protecting the sensor from direct impact
Stabilize the signal output and extend sensor life in turbulent flow conditions
This design is particularly important in applications where rapid pressure transitions are expected.
5. Best Practices for Field Installation in Harsh Environments
If the pressure transmitter is to be used in hostile or high-shock environments, additional precautions are highly recommended:
✔ Avoid Direct Mounting to High-Pressure Lines
Installing the transmitter directly on pipelines that experience frequent or high-pressure surges should be avoided whenever possible.
✔ Use Intermediate Buffer Elements
Incorporate a buffer tube, pulsation damper, or snubber between the pressure source and the transmitter. This helps dissipate the energy of incoming pressure waves and reduces the risk of sensor damage.
✔ Advantages of Buffer Tube Installation:
Cost-effective and easy to implement
Protects the sensing element from pulsations and thermal effects
Reduces maintenance frequency and replacement costs
This approach has become a standard practice in many industrial setups, particularly where reliability and service life are priorities.
Conclusion
Proper selection and installation of pressure transmitters are vital for ensuring long-term reliability, especially in challenging operating environments. While the core sensing technology is robust, protection against pressure spikes through damping structures and buffered installation is essential to prevent premature failure.
By following these best practices, engineers and technicians can enhance system stability, extend device lifespan, and avoid costly downtime.