Accurate measurement of mineral powder is crucial for optimizing production processes, improving product quality, and ensuring production safety. Among various measurement technologies, radar level meters have gradually become the preferred tool due to their high precision and reliability.
A radar level meter is a measuring instrument based on the time-of-flight principle. It transmits microwaves and receives reflected signals to calculate the distance between the material surface and the radar antenna. Compared to traditional ultrasonic or mechanical measurement methods, radar level meters offer stronger environmental adaptability and higher precision.
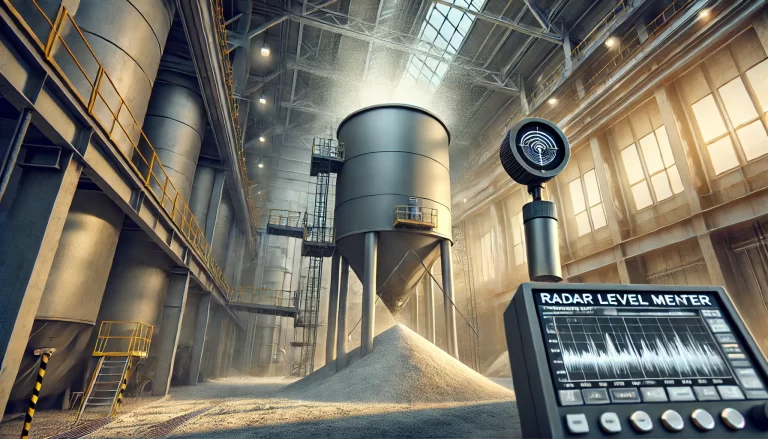
Mineral powder, a common powdery substance in mineral processing, presents several measurement challenges. Factors such as the shape, density, and storage environment of the powder can affect the measurement results. However, radar level meters effectively address these challenges. They utilize electromagnetic waves for measurement, unaffected by temperature or pressure changes and capable of penetrating dust and steam to achieve high-precision measurements.
In practical applications, a mining company used radar level meters to manage its mineral powder warehouses. The company found that the meters not only provided real-time and accurate measurement data but also required low maintenance costs and demonstrated good equipment stability. By using radar level meters, the company avoided material waste and equipment damage, enhancing production efficiency and product consistency.
Compared to other measurement technologies, the advantages of radar level meters are particularly evident. Traditional ultrasonic level meters often encounter interference from dust and steam in complex environments, leading to measurement errors. Radar level meters, on the other hand, utilize high-frequency microwaves, offering better transmission performance and anti-interference capabilities. Additionally, radar level meters are relatively easy to install and maintain, capable of long-term stable operation in harsh industrial environments.
To ensure measurement accuracy, certain key factors should be considered during use. The installation location is critical; the meter should be installed away from areas prone to material accumulation and turbulence and should maintain a certain distance from the warehouse walls to avoid errors caused by signal reflection. Regular calibration and maintenance of the equipment are also essential to ensure accuracy. By comparing with known standard levels, calibration can effectively eliminate measurement deviations caused by prolonged operation.
In conclusion, the use of radar level meters for measuring mineral powder has improved production efficiency and product quality while providing strong support for the company’s safe production practices.