Routine inspection in industrial environments is more than a formality—it’s a vital part of equipment management and risk prevention. This article provides a comprehensive guide to the purpose, methods, responsibilities, and common pitfalls in inspection work, with practical strategies for ensuring safety and reliability.
1. Purpose of Routine Inspection
The core goal of routine inspection is to detect abnormalities in equipment early, thereby avoiding unexpected shutdowns and preventing accidents. Inspection covers a wide scope, including:
Mechanical and static equipment
Pipelines and valves
Instrumentation and control points
A qualified inspection process ensures the stability and safety of the production system.
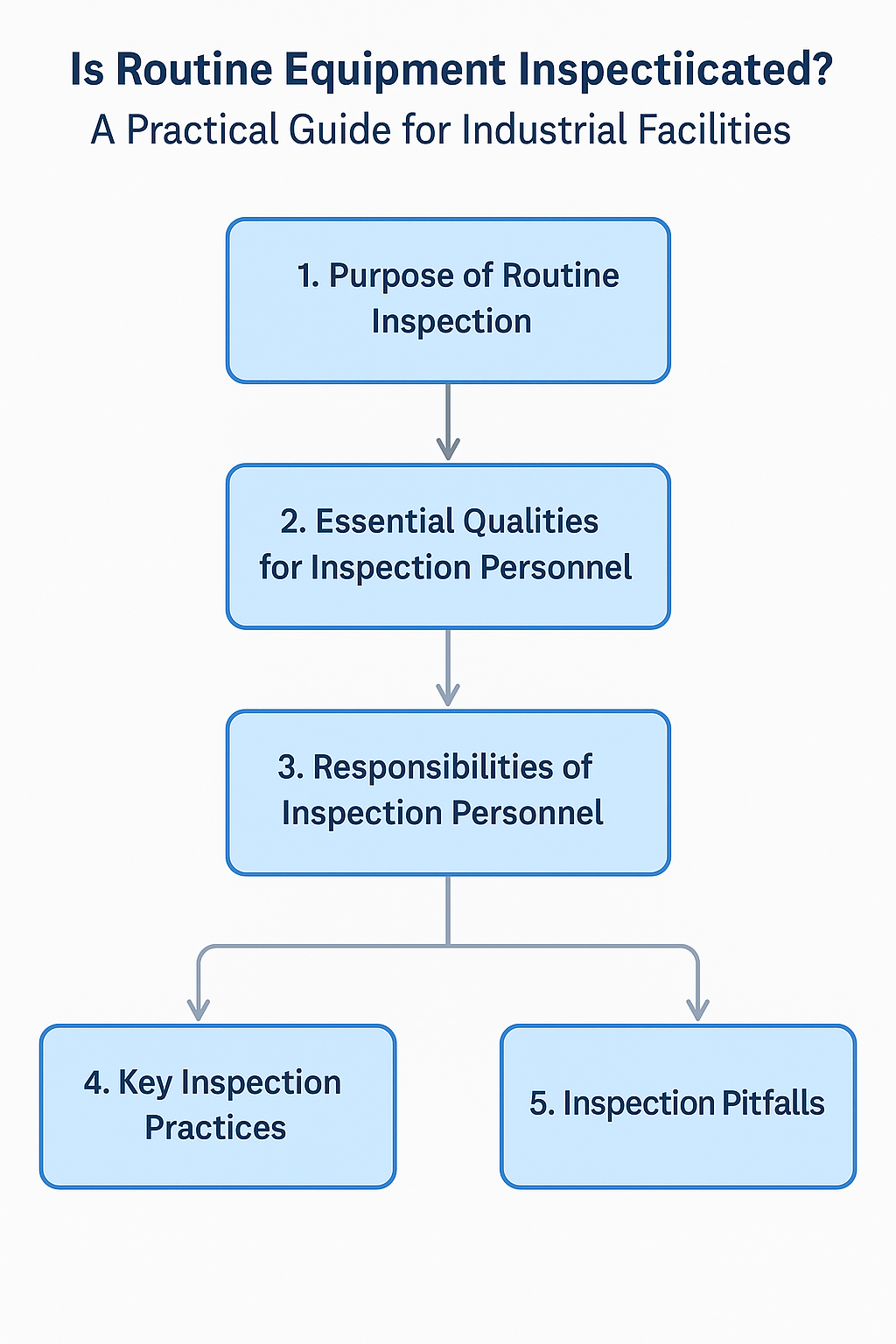
2. Essential Qualities for Inspection Personnel
Competent inspection personnel must meet the “Four Understandings and Three Skills” standard:
Understand equipment structure, operation principles, common faults, and safety precautions.
Be skilled in operation, maintenance, and troubleshooting.
This requires systematic theoretical training and on-site experience—especially important for personnel transitioning from unrelated roles.
3. Responsibilities of Inspection Personnel
While automation has reduced the need for constant onsite presence, manual inspection is still indispensable during startup, shutdown, and abnormal situations. Thus, on-site inspection teams are essential for:
Verifying normal operations
Responding quickly to issues
Recording and reporting faults
4. Key Inspection Practices
4.1. The “Five Senses” Method
A highly effective technique combines human sensory input with routine procedures:
Look: Observe equipment condition, leaks, discoloration, or changes in indicator readings (temperature, pressure, level).
Listen: Detect unusual noises or vibrations that indicate wear or imbalance.
Smell: Identify leaks or overheating by abnormal odors.
Touch: Feel for temperature, vibration, or loose components using hands or tools (carefully and safely).
Think: Compare current data with historical trends; analyze deviations.
5. Inspection Best Practices
Understand production processes and equipment thoroughly.
Always wear PPE and use protective instruments.
In case of gas leaks or toxic hazards—report immediately. Never attempt to “be the hero.”
The inspection must emphasize three types of safety:
Personal Safety
Equipment Safety
Product Quality Safety
6. Key Inspection Areas
Focus should be placed on:
Critical equipment
Known defective units
Under-maintenance or temporary repairs
Units awaiting overhaul
Tailor the checklist based on the type of device (static vs. rotating). Examples include:
Static equipment: Look for discoloration, corrosion, or leaks at flanges, nozzles, or vessel walls.
Rotating equipment: Listen for noise changes, check lubrication, observe bearing temperatures and alignment.
7. Defect Handling
Operators should eliminate minor defects promptly and log the details.
If unable to resolve, report up the chain and monitor for changes.
Unresolved issues must be discussed in daily shift meetings.
All repairs should have clear ownership, safety measures, and implementation plans.
8. Equipment Status Monitoring
Dynamic equipment management allows maintenance and operations teams to:
Monitor trends in performance
Predict failures using early warning signals
Schedule maintenance proactively
9. Common Inspection Pitfalls
Focusing only on major or rotating equipment, ignoring secondary/static units (especially those in remote or elevated areas).
Underestimating long-term minor leaks or known issues, leading to complacency.
Valuing form over substance, resulting in superficial walkarounds rather than meaningful analysis.
Neglecting personal safety, especially in hazardous zones or during emergencies.
10. General Equipment Checklist: Centrifugal Pumps Example
Check for abnormal noise and vibration using a sound rod or stethoscope.
Monitor temperature of bearings and casing (≤65°C is standard).
Inspect seals for leaks (mechanical seals should not leak; packing seals may allow minor dripping).
Confirm oil levels, pressure gauges, and flow meters are within normal ranges.
Examine the cooling system and tightening of foundation bolts.
Never wear gloves when handling rotating equipment.
Verify seal water availability—absence may burn the seal.
11. Outdoor Walkdown Guidelines
Wear full PPE and carry detectors (e.g., gas or H₂S alarm).
Understand hazardous zones and dominant wind directions.
Avoid steam clouds, slippery areas, and overhanging objects.
Stick to designated routes and never walk on pipelines.
12. Performance Assessment
Inspection performance should be evaluated not just by attendance or documentation, but also by:
Safety compliance
Quality and accuracy of findings
Predictive capability (e.g., through trend analysis)
Contribution to equipment reliability and energy efficiency
13. Final Thoughts
While routine inspection may appear repetitive, it plays a crucial role in preventing accidents and extending equipment life. With the right training, attention to detail, and proactive mindset, inspectors serve as the frontline defenders of plant safety.