Atmospheric storage tanks and breather valves play a critical role in the storage of liquids, particularly in industries such as petroleum, chemicals, and food processing. Regular inspections and maintenance are essential to ensure safe and efficient operations. This article outlines the regulatory requirements, inspection methodologies, and maintenance guidelines based on international standards.
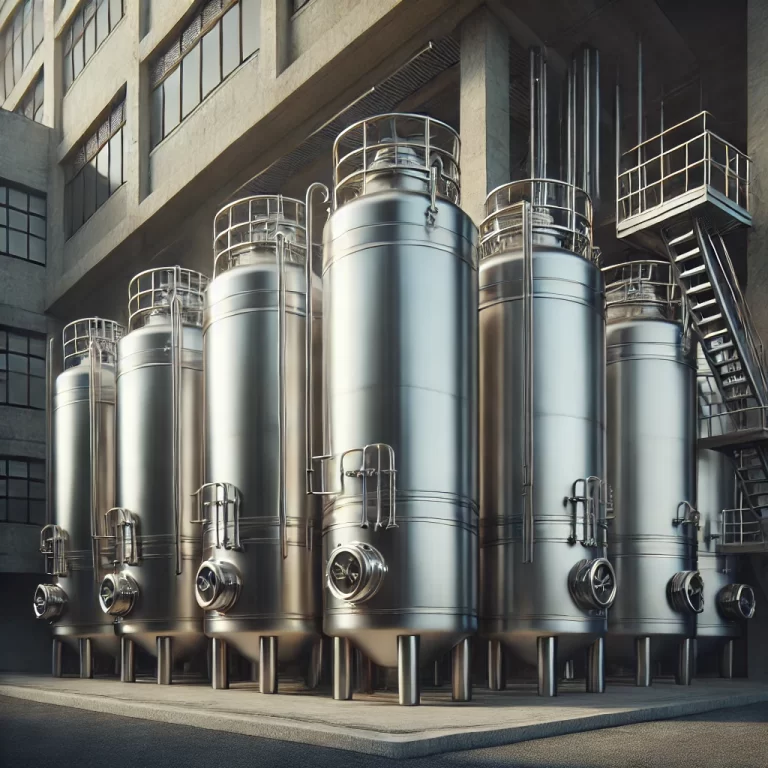
1. Inspection Requirements for Atmospheric Storage Tanks
Atmospheric storage tanks are designed to store liquids at ambient pressure. Proper inspection is necessary to monitor the tank’s structural integrity, prevent leaks, and ensure compliance with safety regulations. The inspection of atmospheric storage tanks generally adheres to standards such as API 653, GB/T 25198-2010, and other industry-specific guidelines.
1.1 Types of Inspections
External Inspection
- Frequency: Conducted annually.
- Scope:
- Visual examination of the external surfaces for signs of:
- Corrosion, pitting, and general deterioration;
- Cracks or weld defects;
- Settlement, deformation, or bulging of the tank shell and roof;
- Integrity of nozzles, manholes, drains, and pipes;
- Check for coating integrity and ensure there is no flaking or peeling;
- Assess the condition of accessories such as ladders, platforms, and railings.
- Visual examination of the external surfaces for signs of:
- Tools: Visual inspection tools, corrosion thickness gauges, and cameras for hard-to-access areas.
Internal Inspection
- Frequency: Every 3 to 6 years, depending on the tank’s usage, stored medium, and operational history.
- Scope:
- Inspect the tank’s inner surfaces for corrosion, erosion, and cracks;
- Examine the bottom plate for any signs of thinning, leakage, or corrosion holes;
- Conduct non-destructive testing (NDT) such as ultrasonic thickness testing (UT), magnetic particle testing (MT), and dye penetrant testing (PT);
- Remove sediments or sludge from the tank bottom and inspect for uneven buildup.
- Safety Precautions: Before internal inspection, tanks should be fully drained, cleaned, and ventilated. Confined space entry protocols must be followed, including gas detection and proper permits.
Leakage and Seal Integrity Testing
- Frequency: Conducted during major inspections or when required.
- Scope:
- Perform a hydrostatic test or pneumatic test to ensure the tank’s structural integrity and leak-tightness.
- Hydrostatic testing involves filling the tank with water and monitoring for leaks.
- Standards: Follow API 653 guidelines for pressure and acceptance criteria.
Foundation and Settlement Check
- Frequency: Every 3 years or when irregularities are observed.
- Scope:
- Inspect the foundation for cracks, settlement, or erosion;
- Measure vertical and horizontal settlement using survey tools;
- Ensure the tank remains level and within tolerance.
2. Inspection and Maintenance of Breather Valves
Breather valves, also known as pressure-vacuum relief valves, are essential safety devices installed on atmospheric storage tanks to regulate pressure changes. They prevent overpressure or vacuum conditions that could cause tank deformation or failure. Inspection and maintenance of breather valves are guided by standards such as API 2000 and GB/T 18529-2001.
2.1 Inspection Requirements
Visual Inspection
- Frequency: Annually or as part of the tank’s external inspection.
- Scope:
- Check for external corrosion, damage, or signs of wear;
- Inspect components such as the body, bonnet, and vent openings for dirt, rust, or obstructions.
Functional Testing
- Frequency: Annually, or more frequently based on operational conditions.
- Scope:
- Test the opening and closing pressures to ensure compliance with design specifications;
- Conduct pressure and vacuum release tests to verify functionality under simulated conditions;
- Inspect for leaks in seals, gaskets, and moving parts;
- Test the response time to pressure changes.
- Tools: Calibrated pressure gauges, test benches, and flowmeters.
Inspection of Fire-Safe Features
- Scope: For flame-arresting breather valves, inspect flame arrestor elements for damage, clogging, or corrosion;
- Ensure that the flame arrestor can effectively prevent ignition hazards.
Cleaning and Calibration
- Frequency: Annually, or as needed.
- Scope:
- Clean all internal components, including valves, seats, and vents, to remove contaminants;
- Replace damaged parts such as gaskets, seals, and diaphragms;
- Calibrate the valve’s pressure settings using calibrated tools.
Record Keeping
- All inspections, tests, and maintenance activities should be properly documented, including:
- Date of inspection;
- Inspection findings;
- Test results;
- Actions taken (e.g., repairs or replacements).
- Maintain records for regulatory compliance and historical analysis.
- All inspections, tests, and maintenance activities should be properly documented, including:
3. General Maintenance Guidelines
Preventive Maintenance
- Implement a preventive maintenance plan for both the storage tank and breather valve to avoid sudden failures.
- Include regular cleaning, repainting, and lubrication of moving parts.
Replacement of Components
- Replace corroded, damaged, or worn-out components, including nozzles, flanges, and gaskets.
- Replace safety accessories such as flame arrestors and seals as per manufacturer recommendations.
Emergency Inspections
- Conduct immediate inspections after abnormal events such as earthquakes, fires, or severe pressure fluctuations.
4. Compliance and Standards
The inspection and maintenance of atmospheric storage tanks and breather valves should comply with the following standards:
- API 650: Welded Tanks for Oil Storage
- API 653: Tank Inspection, Repair, Alteration, and Reconstruction
- API 2000: Venting Atmospheric and Low-Pressure Storage Tanks
- GB/T 25198-2010: Atmospheric Storage Tanks Safety Specifications
- GB/T 18529-2001: Technical Requirements and Testing for Breather Valves
5. Summary of Inspection Cycles
Item | Frequency | Scope |
---|---|---|
External Inspection | Annually | Visual examination of tank shell, roof, and foundation. |
Internal Inspection | Every 3–6 years | Tank corrosion, cracks, and bottom plate condition. |
Leak and Seal Integrity Test | Major inspections | Hydrostatic or pneumatic testing. |
Breather Valve Inspection | Annually | Visual check, functional tests, and cleaning. |
Breather Valve Calibration | Annually | Pressure/vacuum setting tests and calibration. |
By adhering to these detailed inspection and maintenance requirements, organizations can ensure that atmospheric storage tanks and breather valves operate safely, comply with regulatory standards, and extend their service life.