Introduction
Industrial instruments play a critical role in process control, monitoring, and automation across various industries such as oil and gas, chemical processing, power generation, and pharmaceuticals. Selecting the wrong instrument can lead to safety hazards, operational inefficiencies, and financial losses. To ensure safety and reliability, potential hazards must be identified and mitigated during the selection process.
This article explores how to eliminate safety hazards in industrial instrument selection by considering environmental factors, measurement principles, explosion protection, compliance with safety standards, ease of maintenance, and risk assessment.
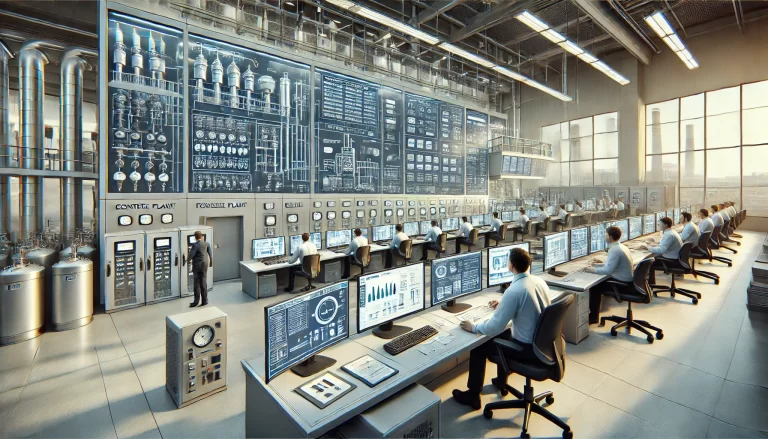
1. Understanding Environmental Factors
The operating environment has a significant impact on instrument performance and safety. Several factors must be evaluated:
Temperature Extremes: Instruments must withstand the ambient and process temperature ranges. High temperatures can degrade sensors, while low temperatures may cause freezing and sensor malfunctions.
Pressure Conditions: Instruments should match the system’s pressure ratings to prevent failures or leakage.
Corrosive and Hazardous Media: Chemicals, moisture, and gases may corrode instrument components. Material selection (e.g., stainless steel, Hastelloy, ceramic) is crucial for longevity and safety.
Dust and Debris: Instruments should have appropriate ingress protection (IP rating) to prevent damage from dust, water, or solid particles.
Explosive Atmospheres: If the environment contains flammable gases, vapors, or dust, instruments must meet explosion-proof or intrinsically safe standards (ATEX, IECEx, FM, CSA).
Electromagnetic Interference (EMI): Instruments must be designed to resist EMI, which can cause incorrect readings or system failures.
2. Selecting the Right Measurement Principle
Each measurement principle has advantages and limitations. Selecting the wrong method can lead to inaccurate readings, process disruptions, and safety risks.
Pressure Measurement:
Diaphragm Seal Transmitters: Recommended for high-pressure and corrosive environments.
Capacitive or Piezoresistive Sensors: Suitable for low-pressure and non-corrosive applications.
Explosion-proof or Intrinsically Safe Models: Necessary for hazardous locations.
Level Measurement:
Radar and Ultrasonic Level Sensors: Ideal for non-contact measurement in hazardous or aggressive liquid applications.
Float-Based Sensors: Suitable for simple applications but not for viscous or foaming liquids.
Hydrostatic Level Sensors: Can be used for deep tanks, but must account for temperature-induced density changes.
Flow Measurement:
Electromagnetic Flow Meters: Recommended for conductive liquids; not suitable for non-conductive fluids.
Coriolis Mass Flow Meters: Preferred for high-accuracy applications, including gas and liquid measurement.
Vortex Flow Meters: Effective for steam and gas applications but require stable flow conditions.
Temperature Measurement:
Thermocouples (K, S Type): Suitable for high-temperature applications (e.g., furnaces, boilers).
Resistance Temperature Detectors (RTDs, PT100/PT1000): Provide high accuracy and stability for lower temperature ranges.
Infrared Sensors: Ideal for non-contact measurement in extreme environments.
Gas Detection:
Catalytic Bead Sensors: Used for detecting combustible gases but require regular calibration.
Infrared (IR) Gas Detectors: Suitable for hydrocarbon gases, offering long-term stability.
Electrochemical Sensors: Effective for toxic gases such as carbon monoxide and hydrogen sulfide.
3. Ensuring Compliance with Safety Standards
To mitigate safety risks, instruments should comply with industry regulations and standards:
ATEX & IECEx: Certifications for explosion-proof and intrinsically safe equipment in hazardous areas.
SIL (Safety Integrity Level): Specifies instrument reliability in safety-critical applications. SIL 2 or higher is often required for process safety.
FM, UL, CSA: Certifications for electrical safety in North American markets.
ISO 9001, ISO 14001: Quality and environmental management standards to ensure long-term operational safety.
4. Considering Installation, Maintenance, and Longevity
A well-chosen instrument should not only be safe but also easy to install, maintain, and operate. Factors to consider:
Remote Monitoring Capabilities: Instruments that support wireless communication reduce the need for manual intervention in hazardous areas.
Self-Diagnostics and Predictive Maintenance: Instruments with built-in health monitoring help predict failures before they occur.
Calibration and Adjustment Needs: Some sensors require frequent recalibration, which can pose risks in hazardous areas.
Mounting and Accessibility: Properly positioned instruments reduce safety risks during installation and maintenance.
Shock and Vibration Resistance: Industrial environments often involve machinery vibrations that can affect instrument readings.
5. Conducting Risk Assessments and Safety Evaluations
A comprehensive risk assessment should be performed before finalizing the instrument selection:
Failure Mode and Effects Analysis (FMEA): Identifies potential failure points and their impact on the system.
Hazard and Operability Study (HAZOP): Evaluates operational risks and mitigation strategies.
Redundancy and Backup Systems: Critical processes may require redundant instrumentation to ensure safety in case of primary sensor failure.
Alarm and Shutdown Mechanisms: Instruments should integrate with safety systems to trigger alarms or shutdowns in hazardous conditions.
Compliance with Safety Instrumented Systems (SIS): Ensures that instruments contribute to overall process safety.
Conclusion
Eliminating safety hazards in industrial instrument selection requires a systematic approach that considers environmental conditions, measurement principles, compliance standards, maintenance requirements, and risk assessments. By selecting the right instruments and ensuring they meet industry-specific safety regulations, organizations can enhance process reliability, reduce operational risks, and protect personnel and equipment.
For complex applications, consulting with instrument manufacturers or industry experts is advisable to ensure optimal and safe instrument selection.