Distributed Control System (DCS) overhauls are critical for ensuring long-term reliability, operational safety, and performance consistency in industrial automation systems. A well-executed overhaul extends the service life of the system, reduces the risk of failures, and enables timely configuration updates based on evolving production requirements.
This guide outlines the key components of a comprehensive DCS system overhaul, from preparation to functional testing and documentation.
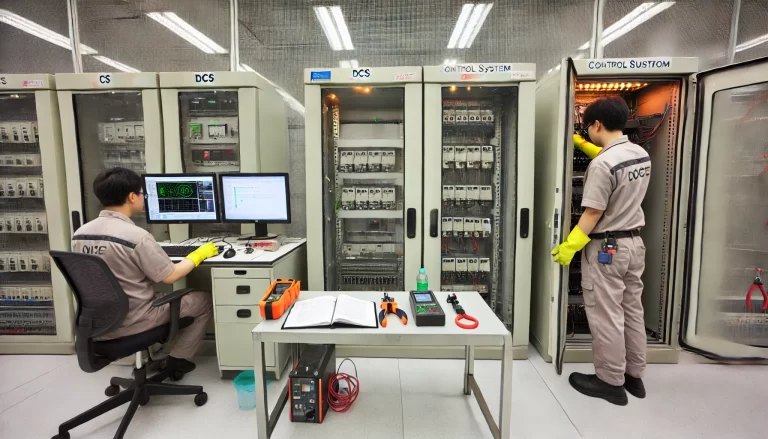
1. Pre-Overhaul Preparation
Before initiating the overhaul, the following steps must be completed:
1.1 Condition Assessment: Analyze the current system performance and identify existing problems. Develop a practical overhaul plan and timeline.
1.2 Resource Readiness: Prepare all necessary tools, testing equipment, cleaning supplies, and spare parts.
1.3 Data Backup: Back up all system software and user configurations to avoid data loss during maintenance.
✅ DCS System Overhaul Checklist
1. Pre-Overhaul Preparation
No. | Item | Completed (✓) | Remarks |
---|---|---|---|
1.1 | System performance assessment completed | ☐ | |
1.2 | Maintenance plan and schedule finalized | ☐ | |
1.3 | Backup of system software and user configurations | ☐ | |
1.4 | All necessary tools and testing equipment prepared | ☐ | |
1.5 | Spare parts and cleaning materials available | ☐ |
2. Overhaul Procedures
2.1 Thorough Cleaning
Clean the entire control room, especially the cabinets, card racks, workstations, terminals, and ventilation systems.
Check for damage or unclear labels on backplanes, terminal blocks, and cables. Replace or relabel as needed.
Carefully disconnect the wiring and modules, label them clearly, and place removed components in order.
Use a vacuum cleaner to remove dust from all surfaces. Clean filters or replace air inlets as necessary.
For dust that cannot be removed by vacuum or air, use neutral detergents. Cleaned components should be stored in a dry, ventilated area.
2.2 Component Reinstallation
After cleaning and inspecting all modules, check the microswitch settings and jumper wiring before reinstallation.
Insert all cards/modules back into their original slots. Reconnect wiring and cables, ensuring all screws are tightened.
2.3 Battery Replacement
Replace onboard batteries that are due to expire before the next scheduled overhaul.
2. Cleaning and Visual Inspection
No. | Item | Completed (✓) | Remarks |
---|---|---|---|
2.1 | Control room thoroughly cleaned | ☐ | |
2.2 | Dust removal from cabinets, racks, monitors, fans, etc. | ☐ | |
2.3 | Air filters cleaned or replaced | ☐ | |
2.4 | Labels and markings on terminals/cables verified | ☐ | |
2.5 | Damaged or worn parts identified and tagged | ☐ |
3. Power-On Commissioning and Diagnostics
Confirm proper insertion of all plug-in cards and secure connections of cables and grounding wires.
Verify that the power supply system meets voltage and current specifications.
Power on all devices sequentially and check voltage levels.
Perform built-in diagnostics for each module and station.
Restore system and user software from backup.
Check system display screens for errors.
Conduct offline diagnostics where needed.
Verify redundancy functions: automatic/manual switchover and enable/disable logic.
Check the accuracy of A/D and D/A modules. Conduct spot testing (15%–20% sampling) on indication modules; increase sampling if issues are found.
Perform signal path verification for interlock-related modules through point-by-point testing.
3. Component Maintenance
No. | Item | Completed (✓) | Remarks |
---|---|---|---|
3.1 | Modules/cardboards removed in proper sequence | ☐ | |
3.2 | Cards cleaned with vacuum and neutral detergent | ☐ | |
3.3 | Cleaned parts dried and stored properly | ☐ | |
3.4 | Battery replacement completed if expiry within next cycle | ☐ |
4. Software Configuration and System Integration
Modify system configurations and logic as needed based on production changes.
Conduct a full system loop check to ensure proper input/output response.
Test all interlock logic by loop to confirm proper action, with verification from responsible personnel.
Backup all updated software (system and user-level) after successful testing.
Record all modifications and test results for documentation.
4. Reinstallation and Wiring Check
No. | Item | Completed (✓) | Remarks |
---|---|---|---|
4.1 | Microswitch and jumper settings checked | ☐ | |
4.2 | All cards reinstalled in correct positions | ☐ | |
4.3 | Wiring connections reattached and secured | ☐ | |
4.4 | Grounding wires checked and tightened | ☐ |
5. Post-Maintenance Documentation
Organize and archive overhaul records, including:
Cleaning reports
Module test results
Software backup logs
Interlock verification records
5. Power-On Test and Functional Checks
No. | Item | Completed (✓) | Remarks |
---|---|---|---|
5.1 | Power supply voltage verified | ☐ | |
5.2 | Module power-on sequence executed properly | ☐ | |
5.3 | Built-in self-diagnostics completed | ☐ | |
5.4 | System and user software restored | ☐ | |
5.5 | Display screens checked for errors | ☐ | |
5.6 | Redundancy (auto/manual switchover) verified | ☐ | |
5.7 | A/D and D/A module calibration completed | ☐ | |
5.8 | Spot testing (15%-20%) of analog input/output modules | ☐ | |
5.9 | Faulty cards replaced and re-tested | ☐ |
6. External Supporting Systems
The following support systems must be coordinated with relevant departments:
UPS System: Perform discharge and switchover tests.
Air Conditioning: Clean or replace filters. For water-based cooling systems, ensure a backup water source is available.
Grounding System: Measure grounding resistance to confirm it meets standards.
Fire Protection: Inspect fire detection and suppression systems.
Lighting: Ensure adequate and functional lighting in control and equipment rooms.
6. System Commissioning
No. | Item | Completed (✓) | Remarks |
---|---|---|---|
6.1 | Logic or configuration modifications done as needed | ☐ | |
6.2 | Full loop check of control and interlock logic | ☐ | |
6.3 | Interlock actions confirmed by safety engineer | ☐ | |
6.4 | Final backup of all updated software | ☐ | |
6.5 | All test results and actions documented | ☐ |
✅ Conclusion
DCS overhauls involve more than hardware cleaning or replacement—they are systematic engineering activities requiring strict procedures, collaboration across departments, and detailed documentation. A successful overhaul ensures system reliability, accuracy of control, and improved safety in plant operations.
7. External System Coordination
No. | Item | Completed (✓) | Remarks |
---|---|---|---|
7.1 | UPS discharge and switchover test | ☐ | |
7.2 | Air conditioner filter cleaning/replacement | ☐ | |
7.3 | Backup water supply for water-based cooling units | ☐ | |
7.4 | Grounding resistance measurement performed | ☐ | |
7.5 | Fire protection systems tested | ☐ | |
7.6 | Lighting system inspected | ☐ |