Distributed Control Systems (DCS) are the backbone of modern industrial automation, responsible for real-time control, monitoring, and data acquisition. However, like all complex systems, DCS components can experience a variety of faults that may lead to process interruptions or safety risks. This article summarizes the most frequently encountered failures in DCS systems and provides practical guidance for diagnosis and mitigation.
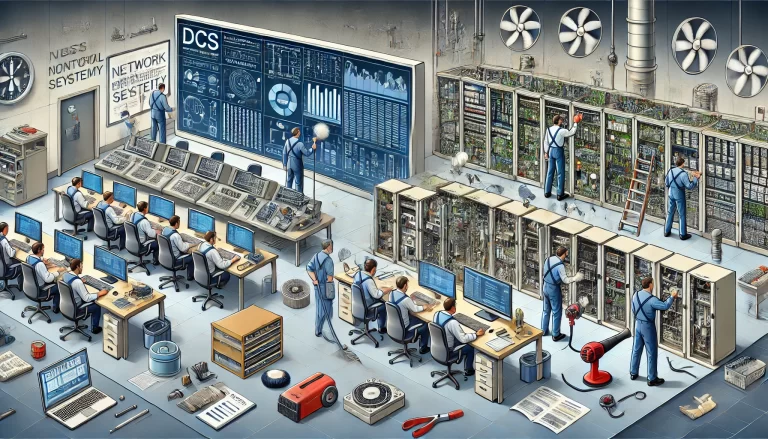
1. I/O Card Failures
Symptoms and Identification
I/O card failures are typically detected through system diagnostics. Symptoms include abnormal signal readings, channel loss, or communication errors.
Common Causes
Aging of internal electronic components
Connector failures or corrosion
Manufacturing defects
Troubleshooting and Resolution
Since most I/O cards are integrated modules, field-level maintenance is limited. In most cases:
Replace the card with a spare module
Swap channels (if supported)
Contact the manufacturer for component-level repair
⚠️ Note: Hot-swapping of cards should follow strict safety protocols, especially for digital input/output (DI/DO) modules, to prevent load or system fluctuations.
2. Operator Station Crashes (Freezing or Deadlock)
Typical Triggers
Hard disk or memory failure
Faulty expansion cards
Overloaded cooling fans
Human error during configuration or software uploads
Risks and Consequences
System crashes during control logic changes or forced signal operations can cause:
Abnormal system behavior
Unexpected shutdowns
Extended downtime during reboot (varies by manufacturer)
Recommendations
Avoid non-essential configuration during live operation
Ensure system backups and image recovery tools are in place
Use industrial-grade hardware with redundancy where possible
3. Unresponsive Control Operations
When operator inputs do not result in expected process changes, potential causes include:
Software defects: Faulty logic or unverified control schemes
Hardware malfunction: Unresponsive output channels or signal path disruptions
Resolution Strategy
Confirm process feedback signal path is functional
Test communication integrity between operator station and controller
Restart operator station if necessary
4. Power Supply Failures
Failure Modes
Blown fuses or incorrect fuse ratings
Failure of automatic switching between primary and backup power
Voltage fluctuations causing false protections or shutdowns
Loose or oxidized power terminals
Preventive Measures
Proper fuse selection according to load type
Use of UPS (Uninterruptible Power Supply) with redundancy
Dual power input modules where available
Scheduled power terminal inspection and maintenance
5. Electromagnetic Interference (EMI) and Signal Noise
Primary EMI Sources
Improper grounding of the DCS system
Switching of backup power supplies
High-frequency wireless devices (e.g., radios, mobile phones)
Interference from high-voltage or high-current equipment
Mitigation Strategies
Strict adherence to shielding and grounding standards
Maintain adequate spacing between signal cables and power sources
Use isolation modules for high-interference areas
Avoid using handheld radios near the engineer station or control modules
Avoid manual master-slave switching during normal operation unless necessary
Conclusion and Best Practices
While DCS systems are designed for high reliability, proper training, preventive maintenance, and incident analysis are key to minimizing downtime:
Train operators to record system behavior before and after any fault
Implement layered protection, including hardware redundancy and UPS
Collaborate with DCS vendors for firmware updates and system audits
Periodically test hot-swappable modules under safe conditions
By understanding and anticipating common failure modes, facilities can maintain stable operation, reduce unplanned shutdowns, and enhance system safety.