Cabinetless automation systems can reduce costs and minimize floor space, helping manufacturers and end users optimize installation, support, and maintenance processes. This article explores the three critical stages of implementing cabinetless automation designs and examines their feasibility in modern industrial environments.
The Evolution Towards Cabinetless Automation
Transitioning to a cabinetless automation system is similar to training for a marathon. Runners do not simply show up in old running shoes with good intentions; they follow a structured training regimen, gradually increasing their distances from 5 kilometers to a half marathon, ultimately preparing for the final goal. Similarly, adopting cabinetless automation requires a phased approach, allowing companies to test and refine their systems gradually.
Traditionally, control cabinets were essential to protect power supplies, input/output (I/O) modules, networks, human-machine interfaces (HMI), controllers, and other devices from harsh industrial environments. However, advancements in machine control technology are enabling manufacturers to phase out these enclosures, leading to cost and space savings while enhancing operational efficiency.
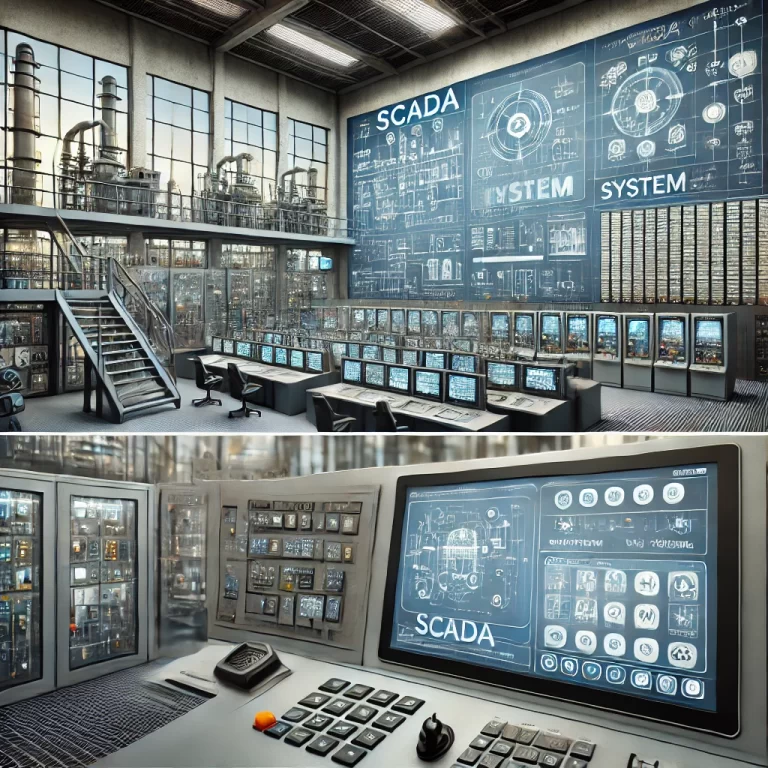
Advantages of Cabinetless Design
For machine builders, original equipment manufacturers (OEMs), and end users, adopting cabinetless designs offers several benefits:
Reduced Total Cost: Eliminating control cabinets removes the need for fans, filters, cooling systems, and associated power supplies, leading to substantial cost savings.
Simplified Installation: Standardized connectors help minimize wiring time, reduce documentation efforts, and eliminate wiring errors.
Optimized Space Utilization: With machines occupying less floor space, manufacturers can install more equipment within the same area.
Enhanced Maintenance Efficiency: Distributed control components simplify troubleshooting and allow for easy replacements without complex rewiring.
Despite these advantages, transitioning to cabinetless automation requires careful planning. Understanding how to move from traditional cabinet-dependent designs to cabinetless setups involves three key phases.
Phase 1: Distributed I/O for Data Collection
The first step, akin to a runner’s 5-kilometer training, involves adding functions without expanding the control cabinet. Companies can introduce remote I/O modules and IP65/67-rated machine controllers that do not require protective enclosures.
Strategic deployment of ruggedized I/O modules (IP67/IP69K) enables significant progress in collecting data from sensors, communication networks, and safety functions. Distributing I/O modules closer to end devices reduces wiring complexity and installation time.
Industrial PC Solutions: Industrial PCs (IPCs) deployed on-site can act as gateways for IoT or edge computing applications. These devices offer flexibility in physical placement, reducing the need for cabinet space and associated cooling systems. With EtherCAT P technology, combining power and communication in a single four-wire cable simplifies connectivity for data acquisition blocks.
Industrial PCs equipped with analytics software can preprocess data and transmit critical information via cellular or Wi-Fi networks to enterprise or cloud-based systems. This solution is ideal for brownfield applications where existing equipment needs monitoring without major infrastructure changes.
Phase 2: Machine-Mounted Control and Distributed Motion Control
Once companies have successfully implemented distributed I/O, the next phase focuses on reducing cabinet requirements for new machines. Advances in cabinetless technologies, such as integrated servo drives and industrial PCs, allow engineers to shrink cabinet sizes further.
Key Technologies in This Phase:
Cabinetless Industrial PCs: Dual-core or quad-core IPCs can serve as primary machine controllers, running control logic for specific machine modules.
Integrated Servo Motors: Combining the amplifier within the motor housing eliminates the need for separate cabinet space.
IP65/67 HMI Panels: Ruggedized, fully enclosed panel PCs merge control and visualization functions in one device.
By leveraging remote I/O and EtherCAT P communication, machine builders can integrate dynamic motion control while reducing the need for bulky control cabinets. This approach is particularly beneficial for industries such as packaging, logistics, and assembly, as well as mobile applications like automated guided vehicles (AGVs) and autonomous mobile robots (AMRs).
Phase 3: Fully Cabinetless Automation Systems
The final stage aims to eliminate control cabinets entirely. However, achieving a completely cabinetless setup requires overcoming several technical challenges, particularly in achieving high IP-rated protection for all control and automation components.
Emerging Modular Technologies: Innovations such as scalable backplanes with plug-and-play components allow users to assemble IPCs, drives, I/O, and safety modules without traditional cabinets. This modular design offers the following benefits:
Up to 70% reduction in machine footprint.
10x reduction in required control components.
80% decrease in documentation efforts.
Elimination of costly wiring errors and multiple failure points.
Accelerated time-to-market with plug-and-play capabilities.
For example, plug-in automation components can reduce control system installation time from 24 hours to just one hour, offering significant operational efficiency.
Furthermore, advanced diagnostic features, such as Bluetooth-enabled monitoring and DataMatrix codes for component identification, simplify maintenance and troubleshooting.
Challenges and Considerations
Despite its promising potential, transitioning to cabinetless automation presents challenges, including:
Environmental Conditions: Ensuring all components can withstand harsh conditions without traditional enclosures.
Integration with Legacy Systems: Seamless communication with existing infrastructure remains crucial.
Safety Compliance: Meeting industry standards for machine safety and redundancy.
Careful planning and phased implementation can help organizations gradually embrace cabinetless automation while mitigating risks.
Conclusion: Selecting the Right Approach
Engineers should carefully evaluate their automation needs before transitioning to a fully cabinetless setup. Some may find that machine-mounted controls meet their immediate requirements, while others may be ready to embrace complete cabinetless automation.
Regardless of the chosen phase, adopting a flexible, scalable automation platform will enable manufacturers to leverage existing software and hardware while preparing for future advancements. An open communication protocol ensures seamless integration with legacy systems and facilitates gradual adoption.
By treating the transition as a marathon rather than a sprint, manufacturers can progressively build upon cabinetless automation technologies, ensuring a smoother and more efficient transformation.