Introduction
Grain production is a multifaceted process that demands precision at every stage. From raw material intake and processing to storage and distribution, accurate instruments and measurement equipment are crucial for ensuring the quality, safety, and efficiency of grain production. In grain factories, selecting the right instruments not only improves operational efficiency but also guarantees stability and safety during production processes.
This guide explores the primary processes of grain factories, the specific instrument needs of each stage, and how to choose the most suitable devices for precision measurement.
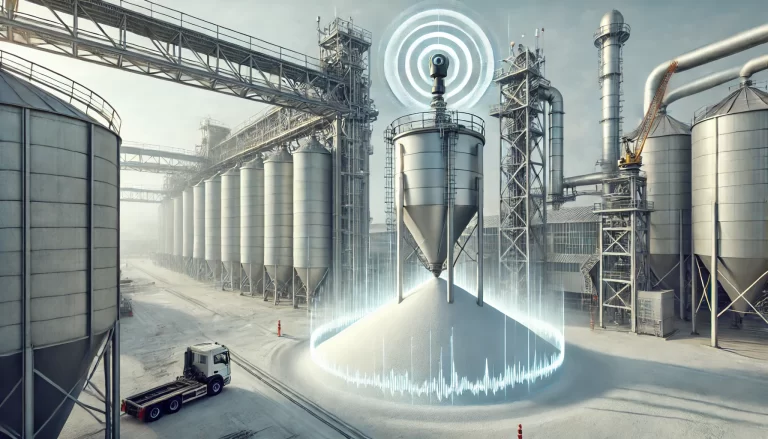
Key Processes in Grain Factories
Grain factories typically follow these major processes:
Raw Material Intake and Preprocessing Grain is transported from farms or warehouses to the factory, where it undergoes cleaning, drying, and screening. This step aims to remove impurities and ensure raw material quality.
Processing Preprocessed grains enter various production lines for grinding, milling, mixing, or other treatments to produce end products such as flour or starch.
Storage and Distribution Finished products and raw materials are stored in large silos before distribution. This phase involves extensive monitoring of parameters such as level, temperature, and humidity.
Packaging and Delivery The final step involves packaging products and preparing them for transportation, ensuring timely delivery to markets.
Every stage requires advanced instrumentation, particularly for measuring level, temperature, humidity, flow, and pressure. Using suitable instruments enhances the efficiency and stability of production.
Instrumentation Requirements for Grain Factories
Level Measurement: Monitoring Silo Levels
Large silos store significant volumes of raw materials and finished products. Level measurement devices are essential for real-time monitoring of storage levels, preventing overfilling or shortages.
Radar Level Transmitters: Using high-frequency electromagnetic waves, radar transmitters provide precise level measurements regardless of environmental conditions like temperature or pressure. Their non-contact nature minimizes wear and reduces maintenance costs, making them ideal for large silos storing granular or powdered materials.
Ultrasonic Level Sensors: These devices utilize ultrasonic waves to measure levels and are suitable for monitoring bulk solids like grain. Ultrasonic sensors offer high accuracy, are easy to install, and require minimal maintenance, making them a cost-effective choice for daily monitoring.
Recommendation: For large-scale grain silos, instruments such as radar and ultrasonic level transmitters provide high precision and low maintenance, ensuring long-term reliability.
Temperature and Humidity Monitoring: Ensuring Grain Quality
Storage conditions greatly affect grain quality. Temperature and humidity changes can lead to spoilage, mold growth, or compromised processing efficiency.
Temperature Sensors: Devices like RTDs (Resistance Temperature Detectors) and thermocouples provide highly accurate temperature data, helping maintain optimal storage conditions.
Humidity Sensors: High humidity can foster mold growth, while low humidity may cause grain desiccation. Real-time humidity sensors ensure grains are stored in ideal conditions.
Gas Detection and Safety Monitoring
During storage and processing, gases such as oxygen, carbon dioxide, or methane may accumulate, particularly in fermentation or damp environments. Gas detection instruments are essential for ensuring safety.
Gas Detectors: These devices monitor harmful gas levels and prevent hazards like explosions or poisoning.
Flow and Pressure Measurement: Managing Fluid Control in Processing
Grain processing often involves fluid control, including water and gas usage. Accurate measurement of flow and pressure is crucial for maintaining equipment stability and ensuring production efficiency.
Mass Flow Meters: For processes like water addition or gas injection, mass flow meters provide precise control of fluid quantities.
Pressure Sensors: Monitoring pressure in pipelines and equipment prevents overpressure or leaks, safeguarding operations.
Dust Monitoring: Ensuring Safety and Cleanliness
Grain processing generates dust, particularly during grinding or crushing. Excessive dust can compromise air quality and pose explosion risks.
Dust Concentration Sensors: These sensors detect dust levels and issue warnings, ensuring a safe and clean working environment.
Factors to Consider When Choosing Instruments
To select the most suitable instruments for grain factories, consider the following:
Accuracy: Many processes demand high precision, particularly for level, flow, and temperature measurements. Ensure instruments meet the required accuracy standards.
Durability and Corrosion Resistance: Instruments must withstand challenging conditions like humidity, dust, and corrosion.
Real-Time Monitoring and Automation: Modern grain factories prioritize automation. Instruments capable of remote monitoring and integration into automated systems are highly advantageous.
Ease of Maintenance: Hygiene is critical in grain production. Instruments should be easy to clean and maintain.
Compliance with Industry Standards: Ensure selected instruments meet relevant industry certifications and food safety standards.
Practical Case Study: Implementation of Instruments in a Grain Factory
Scenario: A mid-sized grain processing plant faced frequent issues with silo overfilling and moldy storage conditions.
Solution:
Installed radar level transmitters to accurately monitor silo levels, preventing overfilling and ensuring efficient inventory management.
Deployed RTD sensors and advanced humidity sensors to maintain optimal storage conditions, reducing spoilage rates by 20%.
Introduced gas detectors to ensure safety during storage and processing phases.
Result: The plant achieved a 15% increase in production efficiency and improved grain quality, leading to higher customer satisfaction.
Emerging Trends: Smart Instrumentation for Grain Factories
IoT Integration: Internet of Things (IoT) technology enables real-time data collection and remote monitoring, enhancing process automation.
Predictive Maintenance: Smart sensors equipped with predictive analytics can identify potential equipment failures, reducing downtime.
Sustainability Focus: Energy-efficient instruments and automated systems help reduce environmental impact and operational costs.
Conclusion
Precision instrumentation is indispensable for modern grain factories, where efficiency, quality, and safety are paramount. From level and humidity measurement to dust monitoring and gas detection, the right instruments play a critical role in optimizing production processes.
By carefully evaluating factors such as accuracy, durability, and compliance, grain factories can select instruments that meet their operational needs and pave the way for a sustainable and profitable future.