In industrial environments where ultra-precise temperature control is essential—such as semiconductor manufacturing, precision material processing, and high-end laboratory equipment—relying solely on a general-purpose PLC is often insufficient. While a PLC can technically perform temperature control, it falls short in many aspects when compared to dedicated temperature controllers. This article explores the key reasons behind this choice, focusing on control accuracy, algorithm optimization, system cost, and application-specific adaptability.
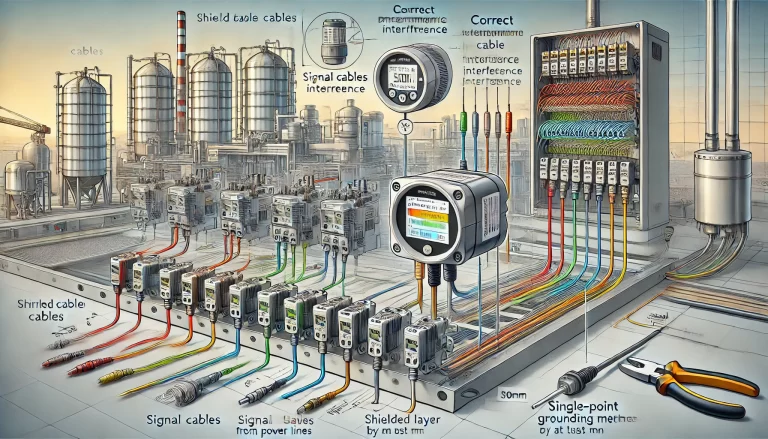
1. Accuracy Is Just the First Barrier
Both PLCs and temperature controllers can implement PID (Proportional-Integral-Derivative) control, a fundamental algorithm in process automation. However, when the control requirement reaches ±0.1°C or tighter tolerances—especially in processes such as etching or thin-film deposition in semiconductor fabrication—many limitations of PLCs become apparent.
Key Challenges in Ultra-Precise Control:
High sampling rate and resolution: Semiconductor processes often require at least 0.01°C display resolution and control accuracy better than ±0.1°C. Standard PLCs, even high-end ones, struggle to meet these stringent demands.
Thermal system lag: For example, heating systems that rely on radiation (e.g., furnaces) have significant lag, increasing the risk of overshoot or undershoot, which can severely affect product yield.
Nonlinearity and process coupling: Temperature control in multi-zone heating or materials with complex thermal characteristics introduces control instability when handled by basic PID or open-loop systems.
2. Hidden Costs of Using General PLCs
Even if we assume the PLC hardware meets the baseline—say, 10ms sampling rate and 16-bit ADC resolution—it still lags behind dedicated controllers in real-world scenarios. Why?
Key Limitations:
No built-in advanced algorithms: PLCs are generic platforms and lack embedded algorithms like cascade PID, feedforward control, or adaptive learning. Users must write these from scratch.
High development and tuning cost: PID tuning in complex environments like semiconductor etching requires expertise in both process knowledge and control theory. Developing a stable algorithm with feedforward compensation can take 2–3 weeks, significantly increasing time-to-market.
Low portability and reusability: Custom control logic developed for a PLC is often tailored for a specific setup. Changing equipment may require re-coding and retuning from scratch, unlike plug-and-play temperature controllers.
3. From “General” to “Specialized”: Value in Encapsulated Intelligence
Dedicated temperature controllers excel not only in control precision and reliability but also in pre-embedded solutions to common industry problems.
Example: Delta DTDM Series Modular Temperature Controller
Delta’s DTDM series showcases how modern controllers embed both hardware and software innovations to meet industry needs:
Modular design: Supports up to 32 PID loops per cluster by combining 4-channel main and extension modules.
High-speed sampling (10ms): With 14-point temperature calibration curves, DTDM minimizes sensor error and improves consistency.
Built-in cascade PID: Handles time-lagged systems by using a master-slave loop structure—greatly improving response time and reducing overshoot.
Feedforward compensation: Provides proactive response to heat disturbances, ideal for dry etching or other highly dynamic processes.
Illustration: Cascade and feedforward mechanisms ensure tighter control for lagging thermal systems.
Industry-specific algorithms: Algorithms tailored to semiconductor tools like CVD, PVD, ALD, and oxidation furnaces come preloaded, reducing integration and commissioning time.
4. Conclusion: Why Controllers Win in Precision Applications
Dedicated temperature controllers are not merely substitutes for PLCs—they are purpose-built solutions. They transform the control paradigm from “general-purpose and reactive” to “specialized and proactive.”
Their benefits include:
Superior hardware optimized for thermal control
Preloaded algorithms that reduce development time
Configurability for multi-zone and complex heating applications
Plug-and-play usability that saves engineering resources
In applications where ±0.1°C accuracy matters, the right choice isn’t just about hardware—it’s about built-in expertise, scalability, and total system efficiency. That’s why precision industries increasingly favor specialized temperature controllers over generic PLCs.