1. Introduction
Modern industrial plants rely on a wide array of automation and safety systems to ensure operational efficiency, product quality, and personnel and environmental safety. Among these, systems such as DCS, SIS, GDS, CCS, PLC, PAS, and MMS each play specific, critical roles.
This article aims to clearly define each system, explain its purpose, highlight its key features, and illustrate how they integrate within a typical industrial facility.
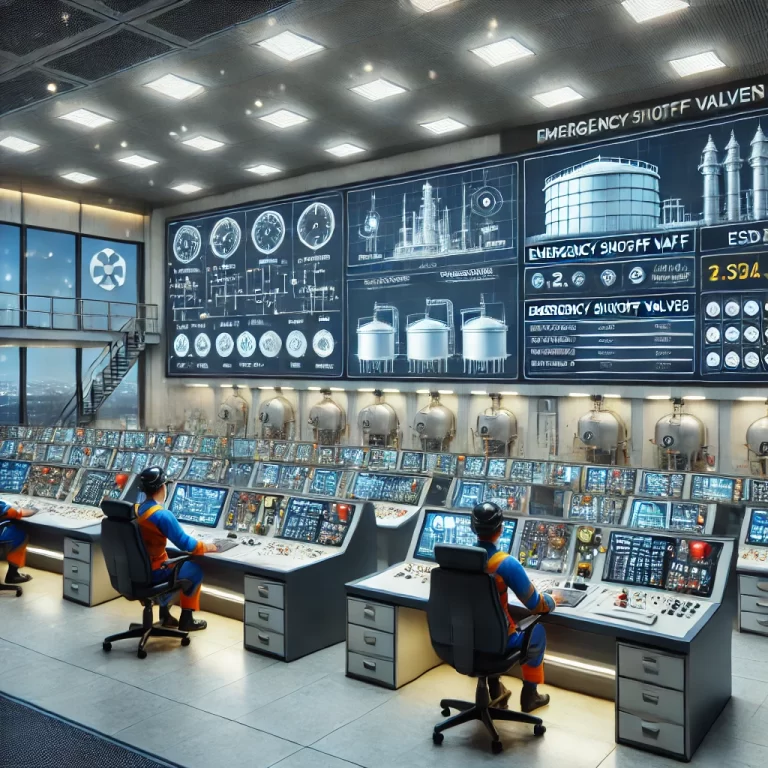
2. Detailed System Overview
Abbreviation | Full Name | Purpose and Main Role | Key Characteristics |
---|---|---|---|
DCS | Distributed Control System | Manages and automates continuous production processes in industries like oil refining, power generation, water treatment, etc. | – Focuses on process continuity – Provides centralized supervision and decentralized control – High stability and redundancy design |
SIS | Safety Instrumented System | Provides emergency shutdown (ESD) or mitigation actions to protect human life, assets, and the environment in the event of hazardous situations. | – Prioritizes safety and fault tolerance – Operates independently from DCS – Designed to achieve specific Safety Integrity Levels (SIL) |
GDS | Gas Detection System | Detects combustible and toxic gas leaks and initiates alarms or automatic responses to prevent explosions or health hazards. | – Real-time, precise detection – Often integrated with SIS for emergency actions – Deploys sensors throughout hazardous areas |
CCS | Compressor Control System | Provides specialized control for compressor operation, including anti-surge protection, load balancing, and emergency shutdown of critical compressors. | – Optimized for dynamic and protective control – Prevents surge and mechanical damage – Fast-responding with complex logic algorithms |
PLC | Programmable Logic Controller | Controls discrete and sequential operations, widely used for machine automation, material handling systems, and utilities management. | – High flexibility and cost-effective – Ideal for small- to medium-scale systems – Supports modular programming and easy maintenance |
PAS | Process Automation System | An overarching system that integrates DCS, SIS, PLC, GDS, CCS and other subsystems into a centralized automation and information platform. | – Focuses on holistic management and optimization – Provides advanced process control (APC) and alarm management – Facilitates centralized engineering and operation |
MMS | Maintenance Management System | Supports proactive maintenance by tracking equipment status, maintenance schedules, and failure histories, improving asset reliability and reducing downtime. | – Specializes in asset health monitoring – Enables predictive maintenance based on real-time data – Often connected to PAS and DCS systems |
3. How These Systems Work Together
In a sophisticated facility, these systems are interlinked but maintain their own independent responsibilities:
DCS operates the core process, controlling temperature, pressure, flow, and other parameters in real-time.
SIS acts as a safety net: if an unsafe condition is detected (such as overpressure or gas leak), it automatically triggers shutdowns and alarms.
GDS continuously monitors the atmosphere for dangerous gases and sends early warnings.
CCS ensures that key compressors operate within safe limits, managing risks like surge or over-speed.
PLC handles ancillary systems like motor control centers (MCCs), package units, and utility services.
PAS provides a centralized platform for operators to monitor, control, and optimize all process activities across DCS, SIS, GDS, and other subsystems.
MMS manages asset maintenance workflows, minimizing unscheduled downtimes and extending equipment life.
4. Practical Example: A Petrochemical Plant
In a petrochemical production site:
DCS controls the distillation, catalytic cracking, and reforming units.
SIS immediately initiates emergency shutdowns if critical pressure or temperature limits are breached.
GDS scans tank farms and process areas for volatile hydrocarbon leaks.
CCS precisely manages the operation of main process gas compressors.
PLC oversees package boiler units, auxiliary cooling towers, and small batch processes.
PAS integrates all systems into a single supervisory and data acquisition platform.
MMS schedules predictive maintenance based on usage patterns and sensor feedback, such as vibration analysis.
5. Key Takeaways
DCS and PLC are primarily focused on process and machine control.
SIS and GDS serve safety and protection purposes, often independently from standard control logic.
CCS is a specialized control system for a critical rotating equipment group.
PAS is the top-level platform ensuring seamless operation across multiple subsystems.
MMS underpins the reliability-centered maintenance philosophy, crucial for modern asset management.
Understanding the clear distinction between these systems is critical for engineering design, system integration, plant operation, and ensuring compliance with industrial safety standards.