Introduction
Force and torque measurement are foundational to industrial automation, materials testing, and structural monitoring. Two common sensor technologies dominate the field: piezoelectric sensors and strain gauge sensors.
While they both serve the purpose of force measurement, they differ significantly in terms of working principle, performance characteristics, and application suitability.
So which one should you use? This article provides a side-by-side comparison to help you decide.
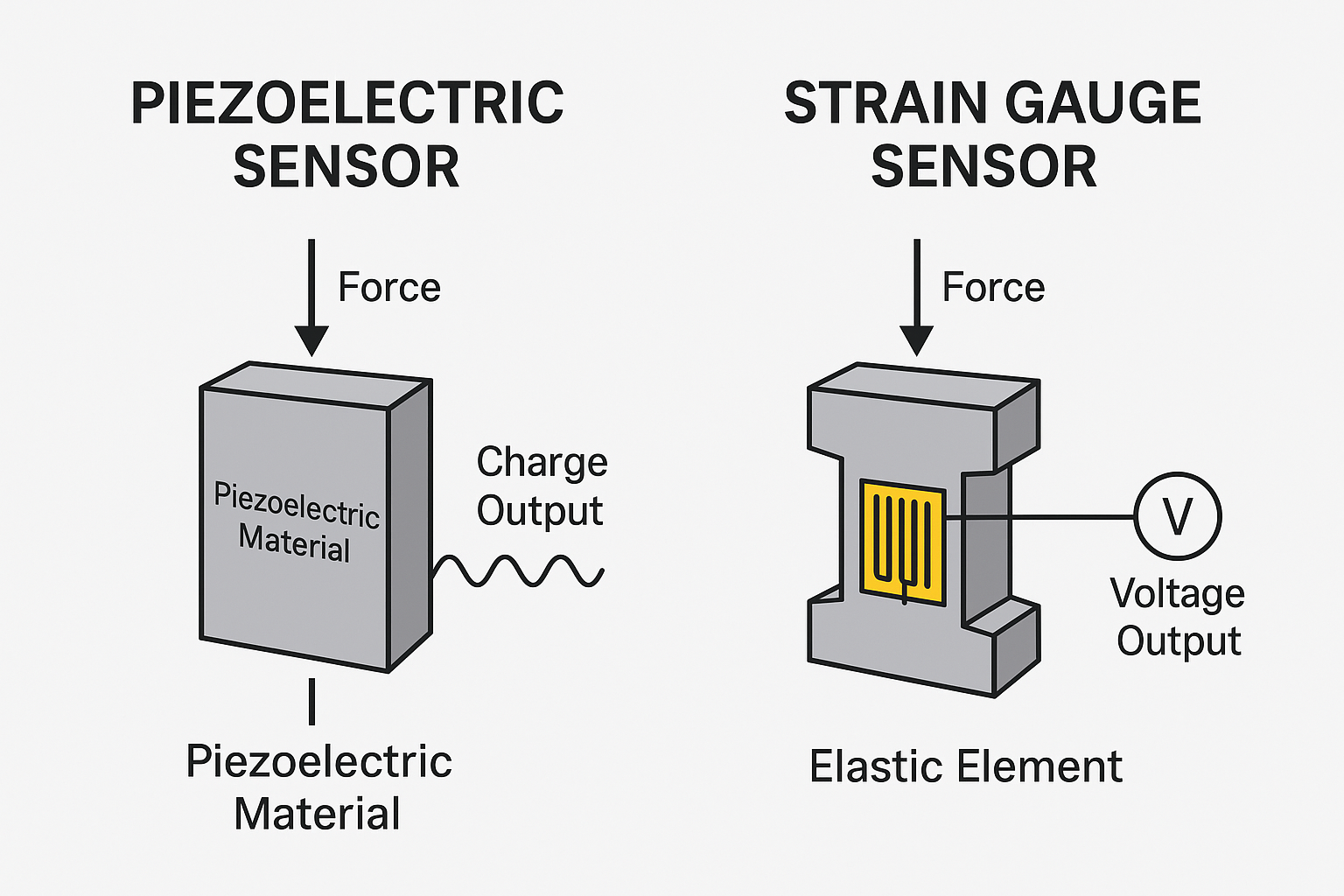
1. Working Principles
⚙️ Strain Gauge Sensors
These sensors use foil or wire strain gauges bonded to a mechanical element. When force is applied, the element deforms slightly, causing a change in resistance. This resistance change is converted into an electrical signal via a Wheatstone bridge circuit.
Signal Type: Analog voltage (e.g., mV/V)
Requires amplification and temperature compensation
Sensitive to mechanical strain (elastic deformation)
⚡ Piezoelectric Sensors
These sensors use materials like quartz or PZT crystals that generate electrical charge when mechanically stressed. The output is a high-impedance charge signal proportional to the applied dynamic force.
Signal Type: Charge output (pC), requires a charge amplifier
No strain gauges involved
Ideal for measuring dynamic/fast-changing forces
2. Comparative Overview
Feature | Strain Gauge Sensor | Piezoelectric Sensor |
---|---|---|
Force Type | Static or slowly changing | Dynamic or transient |
Accuracy (static) | Very high (±0.03% typical) | Moderate |
Frequency Response | Low to medium (<1 kHz) | High (>100 kHz possible) |
Sensitivity to Noise | Low (low-impedance signal) | High (requires shielding/amplifier) |
Drift Over Time | Low (good long-term stability) | Higher, especially with temp changes |
Signal Conditioning | Simple amplifiers (voltage) | Requires charge or ICP amplifier |
Temperature Range | -20°C to +80°C typical | Up to +150°C or more |
Cost (sensor only) | Lower (mainstream industrial use) | Higher, plus amplifier cost |
3. When to Use a Strain Gauge Sensor
✅ You need precise static force or weight measurement
✅ You’re designing a weighing system, load cell, or torque transducer
✅ Your application involves slow or steady forces
✅ Cost-efficiency and long-term stability are important
Typical Applications:
Silo and tank weighing
Torque monitoring in motors and drives
Structural load monitoring
Universal testing machines
4. When to Use a Piezoelectric Sensor
✅ You’re measuring dynamic, fast-changing, or impact forces
✅ You require high-frequency response
✅ Space is limited and compact size is preferred
✅ You’re monitoring vibration, stamping, or press-fit forces
Typical Applications:
Shock and impact monitoring
Press tooling force feedback
Machine vibration diagnostics
Ultrasonic welding or punching systems
5. Key Takeaways
Strain Gauge Sensors are the go-to solution for static and general-purpose industrial force measurement.
Piezoelectric Sensors excel in high-speed, dynamic force applications where rapid response is critical.
👉 For most process automation systems, strain gauge technology is sufficient and cost-effective.
👉 For research labs, dynamic testing, or impact measurement, piezoelectric sensors may be essential.
🔍 Sensor Application Quick Reference Guide
Application Scenario | Force Type | Recommended Sensor Type | Notes |
---|---|---|---|
Tank / Hopper Weighing | Static | Strain Gauge | Reliable and economical for load monitoring |
Robotic Arm Torque Monitoring | Dynamic | Strain Gauge or Piezo | Depends on speed and resolution requirements |
Ultrasonic Welding / Punching | High-frequency | Piezoelectric | Excellent dynamic response and compact form |
Motor Shaft Torque Measurement | Dynamic (Rotary) | Strain Gauge | Use rotary torque transducer with amplifier |
Crash or Impact Testing | Transient | Piezoelectric | High-speed response, ideal for short bursts of force |
Bolt / Fastener Tightening Verification | Static | Strain Gauge | Widely used in torque calibration and QC tools |
Vibration Monitoring on Machinery | Oscillating | Piezoelectric | Ideal for measuring force fluctuations and resonance |
Lab Force Testing Machines (e.g. UTM) | Static or slow | Strain Gauge | High accuracy and linearity for static test loads |
High-temp or Corrosive Industrial Settings | Static / Dynamic | Piezo (Quartz) w/ protection | Use IP-rated housing and charge amplifier |
Dynamic Web Tension Control | Rapid feedback | Piezoelectric or hybrid | Fast signal transmission for process control systems |
Final Thoughts
The right choice depends on your measurement goals, signal requirements, environmental conditions, and budget. Don’t just look at the sensor—consider your amplification, data acquisition, and mounting setup as part of the total solution.
If you’re designing a new measurement system or upgrading an old one, consulting a sensor expert can save you time and money down the line.