Toxic gas detectors are vital safety devices in industrial environments, designed to identify hazardous gases at low concentrations to prevent accidents, health risks, and equipment damage. Multiple sensor technologies are employed in these detectors, each with distinct working principles, advantages, limitations, and suitable use cases. This article presents a detailed comparison of the most common detection methods used in toxic gas monitoring.
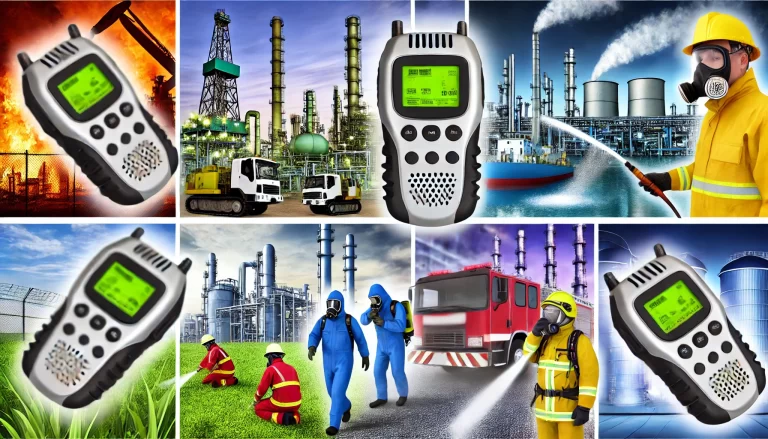
1. Electrochemical Sensor Detection
Working Principle: Electrochemical sensors detect gases through redox reactions that generate electrical signals proportional to the gas concentration. They are suitable for gases such as CO, H2S, NO2, and Cl2.
Advantages:
High sensitivity and accuracy (ppm-level detection)
Good selectivity for target gases
Low power consumption, ideal for portable use
Limitations:
Affected by temperature and humidity
Short lifespan (typically 1–3 years)
Not suitable for non-reactive gases like methane or CO2
Applications: Confined space monitoring, industrial health and safety, portable toxic gas detectors
2. Photoionization Detection (PID)
Working Principle: PID uses ultraviolet light to ionize volatile organic compounds (VOCs). The resulting current is measured to determine gas concentration. Common targets include benzene, formaldehyde, and vinyl chloride.
Advantages:
Extremely fast response (seconds)
High sensitivity (ppb to ppm)
Non-destructive analysis allows further testing of the sample
Limitations:
Ineffective for gases with high ionization potential (e.g., CO)
Cannot distinguish gases with the same ionization energy
Sensitive to humidity and particulate matter
Applications: Indoor air quality testing, chemical spill response, VOC screening in environmental studies
3. Non-Dispersive Infrared (NDIR) Detection
Working Principle: NDIR sensors measure the absorption of infrared light at specific wavelengths by gases like CO2, CH4, and CO. Each gas absorbs IR light uniquely, enabling identification and quantification.
Advantages:
Non-contact measurement with long sensor life (5–10 years)
Resistant to humidity and dust interference
Suitable for stable, long-term monitoring
Limitations:
Only detects IR-active gases (e.g., with C=O or C-H bonds)
Overlapping absorption bands can complicate analysis
High cost and larger size
Applications: Emission monitoring, process control in industries, greenhouse gas measurements
4. Semiconductor Sensor Detection
Working Principle: These sensors use metal oxide semiconductors (e.g., SnO2) that change conductivity when gas molecules are adsorbed on the surface. They are sensitive to various toxic and combustible gases.
Advantages:
Low cost and power consumption
Fast response time for ppm-level gases
Compact and easily integrated
Limitations:
Poor selectivity and cross-sensitivity to alcohol, moisture, etc.
Limited long-term stability
Requires frequent calibration
Applications: Residential gas leak alarms, budget industrial safety systems, indoor pollution detection
5. Catalytic Combustion Detection
Working Principle: Combustible gases burn on a catalytic surface, producing heat and changing sensor resistance. While mainly for flammable gases, some toxic gases like H2S can be detected this way.
Advantages:
High sensitivity to flammable gases
Broad linear detection range (up to 100% LEL)
Proven, cost-effective technology
Limitations:
Requires oxygen to function
Can be poisoned by sulfur compounds like H2S
Not suitable for non-combustible toxic gases
Applications: Explosive atmosphere monitoring in petrochemical plants, refineries, and gas stations
6. Spectroscopic Detection (Laser/UV Differential Absorption)
Working Principle: Gas-specific absorption spectra are used to measure gas concentrations using tunable diode lasers or UV sources. Target gases include SO2, NO, NH3, and others.
Advantages:
Exceptional precision (ppb-level) and selectivity
Remote sensing capability over long distances
Maintenance-free and long operational lifespan
Limitations:
High initial cost and complexity
Suitable for specific gases only
Requires skilled calibration and installation
Applications: Environmental air quality monitoring, real-time emissions tracking, regulatory compliance systems
Comparative Summary Table
Detection Method | Suitable Gases | Detection Range | Accuracy | Key Advantages | Main Limitations | Common Applications |
---|---|---|---|---|---|---|
Electrochemical | CO, H2S, NO2, Cl2 | ppm | High | Sensitive, selective, portable | Short lifespan, humidity-sensitive | Occupational safety, confined spaces |
PID | VOCs (benzene, formaldehyde) | ppb–ppm | Very High | Ultra-sensitive, fast, non-invasive | Cross-sensitivity, humidity impact | VOC leak detection, environmental testing |
NDIR | CO2, CO, CH4 | ppm–% | High | Long life, stable, non-contact | High cost, gas selectivity | Fixed monitoring, industrial control |
Semiconductor | CO, NO2, formaldehyde | ppm | Low | Low cost, compact, fast response | Poor selectivity, drift-prone | Household alarms, early-warning systems |
Catalytic Combustion | CH4, H2, some H2S | %LEL | Medium | Mature tech, wide range | Needs O2, sensor poisoning risk | Combustible gas detection in hazardous areas |
Spectroscopic (Laser) | SO2, NO, NH3 | ppb–ppm | Very High | Remote sensing, high accuracy | Expensive, gas-specific | Air pollution control, emissions monitoring |
Selection Recommendations
For low-concentration precision monitoring (e.g., occupational exposure): Use electrochemical or PID sensors.
For long-term, stable fixed monitoring: Use NDIR or laser spectroscopy.
For cost-sensitive or high-density applications: Choose semiconductor or catalytic combustion sensors (only for combustible gases).
For comprehensive monitoring across gas types: Combine multiple sensor types (e.g., electrochemical + PID + NDIR) in an integrated system.
Choose your detection technology based on gas reactivity, whether it’s flammable, required precision, monitoring duration, and budget constraints.