Magnetic level gauges have become essential instruments in petrochemical operations due to their high visibility, durability, and suitability for harsh environments. This article explores how these devices are applied across various sectors, including storage tanks, reactors, pipeline systems, and explosion-prone areas, with emphasis on performance specifications, integration methods, and real-world case studies.
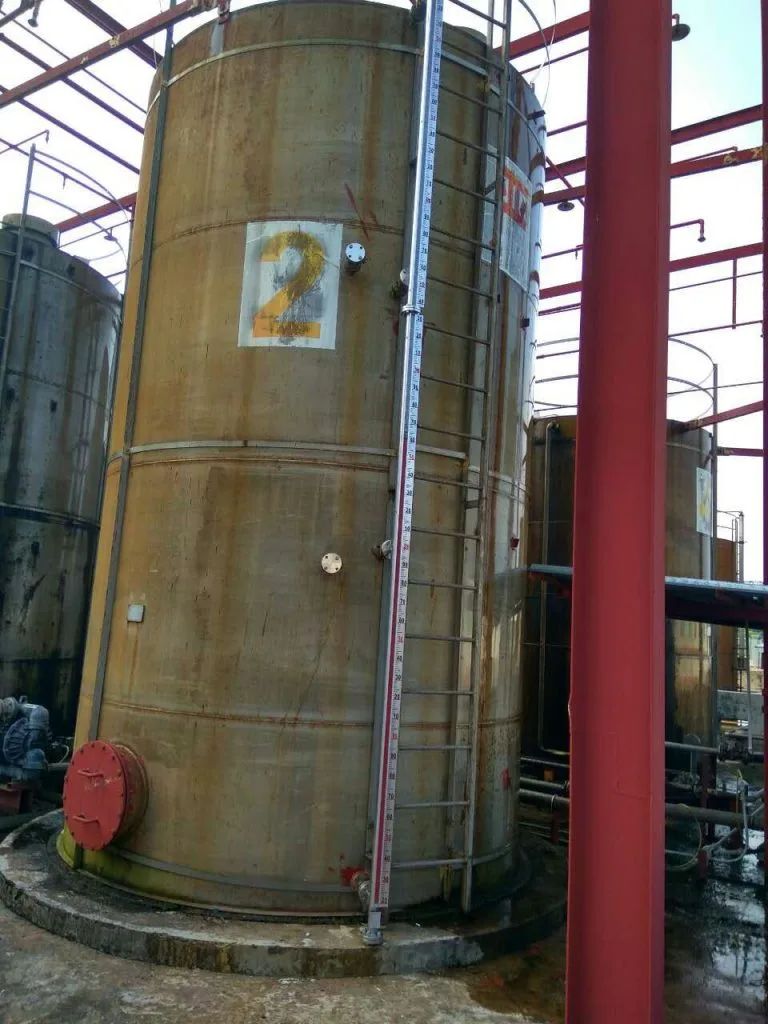
1. Storage Tank Monitoring and Inventory Control
1.1 Crude Oil and Product Storage Tanks
Magnetic level gauges utilize the magnetic coupling principle to provide direct visual indication of liquid levels. They are widely used in large storage tanks (10,000 m³ and above), offering:
Measurement range: 0.5 to 15 meters
Accuracy: ±2mm
Materials: 304/316L stainless steel or PTFE-lined to resist corrosive substances like sulfur compounds and salts in crude oil
Lifespan: Over 8 years under normal operating conditions
Signal Output: 4–20mA or HART-compatible remote transmitters for DCS integration and inventory automation
1.2 LPG and LNG Storage
For liquefied gas tanks, explosion-proof models (ATEX/IECEx certified) are adopted with features including:
Pressure Rating: Up to PN40
Temperature Range: -50°C to +200°C
Sealed Construction: Vacuum insulation jacket prevents frost buildup and float blockage under cryogenic conditions
2. Level Control in Reactors and Separation Equipment
2.1 Reactors and Separators
In high-pressure, high-temperature units like hydrocracking and catalytic reforming reactors:
Operating Conditions: Up to 450°C and 25MPa
Materials: Hastelloy or PP/PVC linings withstand pH 0–14 environments containing strong acids or alkalis
Application: Prevents overflow or dry-run accidents by real-time level monitoring
2.2 Distillation and Desulfurization Towers
Side-Mounted Installation: Suitable for narrow tower wall clearances
Medium: Handles viscous fluids like heavy oil and asphalt
Anti-Freezing Design: Steam-traced chambers ensure flow
LED Backlighting: Ensures visibility in low-light field conditions
3. Pipeline Integration and Pump/Valve Interlock
3.1 Crude Oil Pipeline Monitoring
Integrated via flanged connections (DN50–DN300), these gauges:
Display pump suction/discharge levels
Prevent cavitation or dry-run damage
Pair with explosion-proof magnetic switches (Ex d IIC T6) for alarm triggering and emergency shutdown valve actuation
3.2 Chemical Transportation
In volatile chemical pipelines (e.g., benzene, ethylene):
Leak-Proof Welding: Fully welded construction eliminates gasket-related leakage risks
Remote Output: Signals sent to SCADA for batch delivery tracking and historical data logging
4. Explosion Protection and Extreme Conditions
4.1 Hazardous Area Deployment
Explosion-Proof Models: Certified for Class I/II areas (e.g., Ex ia IIC T4)
Grounding Requirement: Resistance ≤ 4Ω with sealed cable entries
SIL2 Certified: For redundant safety in Safety Instrumented Systems (SIS)
4.2 High Pressure and Cryogenic Environments
Ultra-High Pressure Units: Rated up to 40MPa for use in ammonia, methanol synthesis units
Cryogenic Applications: LNG-compatible models operate at -196°C, using floats filled with special low-temperature magnetic material to prevent demagnetization
5. Installation and Calibration Guidelines
5.1 Installation Requirements
Verticality: Bypass chamber must be ≤2° off vertical
Access Space: ≥500mm for maintenance on side-mounted units
Stabilization: Guide tubes and dampers reduce float oscillation in vibrating areas (e.g., compressor rooms)
5.2 Calibration and Maintenance
Calibration Methods:
≤2m: Standard water column calibration
≥10m: Laser ranging with simulation correction (accuracy within 0.5%)
Routine Maintenance:
Clean indicator every 6 months
Replace float seals every 3 years
Service interval is 3x longer than traditional glass tube level indicators
6. Real-World Case Studies
Case 1: Coastal Refinery Storage Upgrade
A refinery installed magnetic level gauges across 12 crude oil tanks (100,000 m³ each), integrating with remote transmitters and DCS. Result:
Inventory error reduced from ±0.5% to ±0.1%
Annual savings on losses exceeded 12 million CNY (~1.7 million USD)
Case 2: Olefin Production Reactor
A customized high-temp, high-pressure magnetic level gauge was used in a cracking reactor (15MPa, 420°C). Result:
Five years of continuous operation without failure
Cost reduction: Replaced imported units, saving 60% on procurement
✅ Conclusion
Magnetic level gauges offer robust, reliable, and safe solutions for level measurement in demanding petrochemical processes. Their compatibility with harsh environments, automation systems, and safety compliance frameworks make them a preferred choice for both greenfield projects and system upgrades.