1. Definition of Accuracy and Range
Accuracy Class:
Refers to the maximum permissible error as a percentage of the full-scale range.
For example, a gauge with an accuracy of Class 1.0 means the measurement error is within ±1% of its full range.Measurement Range:
Indicates the span between the minimum and maximum measurable pressure.
E.g., a 0–10 MPa gauge has a range of 10 MPa.
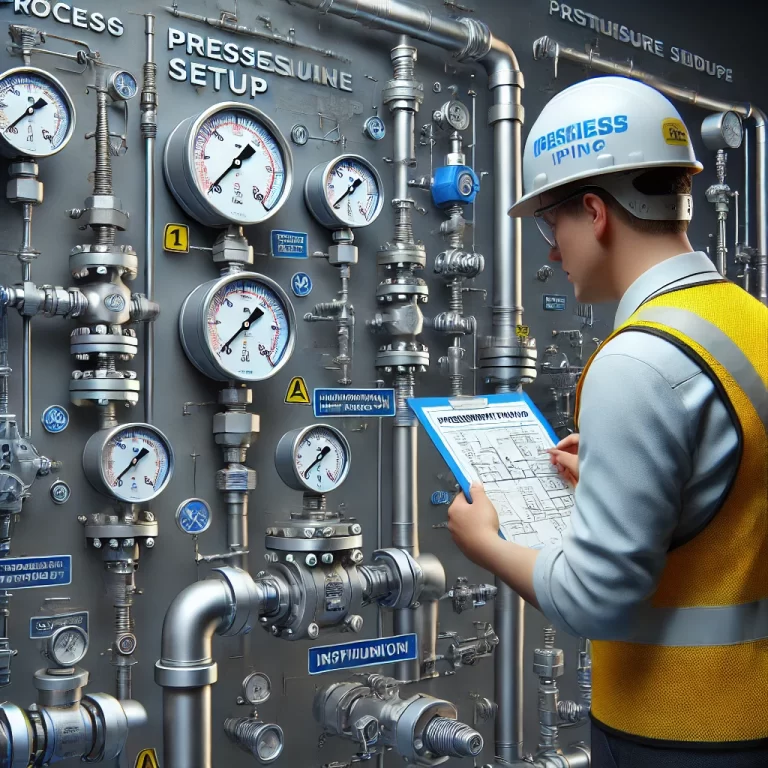
2. The Core Relationship
Formula for Absolute Error:
Absolute Error=Range×Accuracy Class
Example:
A 10 MPa gauge with Class 1.0 accuracy has ±0.1 MPa error.
A 100 MPa gauge with the same accuracy has ±1 MPa error.
✅ Conclusion: The larger the range, the greater the absolute error at the same accuracy level.
Relative Error Consideration:
If actual pressure is far below the full range, relative error increases dramatically.
Example: Using a 100 MPa gauge to measure 10 MPa yields a ±10% relative error.
▶️ Best practice: Keep working pressure within 1/3 to 2/3 of the full range to balance accuracy and safety.
3. Impact of Range Selection on Practical Accuracy
Oversized Range:
Reduces resolution in the low-pressure zone, causing large relative errors.Undersized Range:
Risks overpressure damage; always include a safety margin—typically 1.5 to 2 times the maximum working pressure.
🔧 Optimization Tip: Select a range based on maximum operating pressure and its expected fluctuation, avoiding the “overkill” of using too large a range.
4. Choosing the Right Accuracy Class
Accuracy Class | Typical Applications |
---|---|
2.5 – 4.0 | Low-cost general monitoring |
1.6 – 2.5 | Standard industrial applications |
1.0 – 1.6 | Higher-accuracy process control |
0.6 or better | Lab use, safety-critical systems |
High Accuracy: Low error but higher cost and maintenance
Lower Accuracy: Cost-effective for general use
✅ Tip: Use high-accuracy gauges in safety monitoring and precision control applications.
5. Selection Guidelines
Determine Pressure Range:
Identify max, min, and typical fluctuation range.Select Suitable Gauge Range:
Must exceed the max pressure with 1.5×–2× safety factor.Match Accuracy Class:
Balance between acceptable error and budget.Check Expected Errors:
Ensure the actual pressure falls within a zone where relative error is acceptable.
6. Example: Gauge Selection for an 8 MPa System
Working Pressure: 5–8 MPa
Selected Range: 0–12 MPa (1.5× safety factor)
Accuracy Decision:
If allowed error ≤ 0.12 MPa → Use Class 1.0
If allowed error ≤ 0.2 MPa → Class 1.6 is acceptable and more cost-effective
7. Conclusion
The gauge range determines the base value of error, while the accuracy class defines the error percentage. Matching both wisely leads to optimal performance and cost efficiency. Always consider actual usage, acceptable tolerance, and safety when selecting pressure gauges.