1. Level Measurement Challenges in Metallurgy
The metallurgical industry deals with high-temperature, high-pressure, and highly corrosive liquids under complex process conditions. These environments demand accurate, safe, and stable level measurement solutions. Typical applications include:
Continuous Casting Cooling Water Systems
Real-time monitoring of water levels ensures smooth and safe operation of casting equipment.BOF Dust Removal Water Circulation
Monitoring water levels prevents overflow and protects pumps from running dry.Steelmaking Equipment Cooling
Accurate level control of cooling water for blast furnaces and converters safeguards critical machinery.Softened Steam Water Tanks
Stable water levels ensure system heat balance and vaporization efficiency.
Given the presence of particles, steam, and corrosive substances, traditional contact-type level meters are prone to fouling or corrosion. Ultrasonic level meters, with their non-contact design, provide a reliable alternative in such environments.
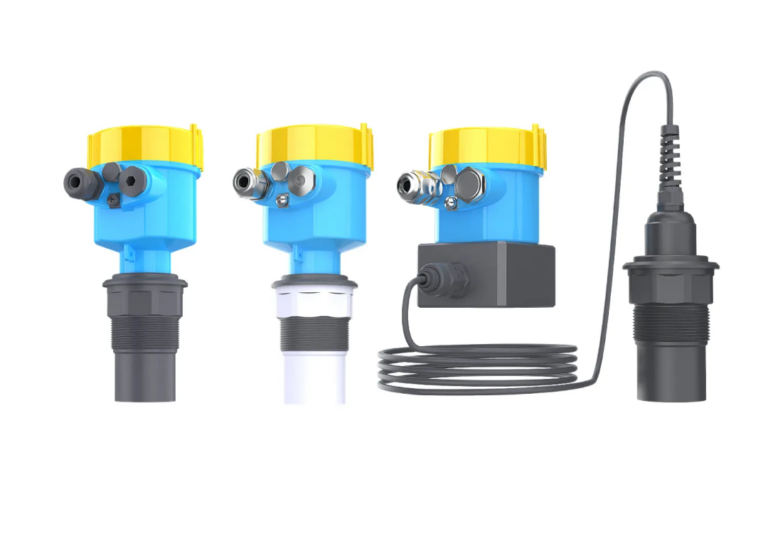
2. Working Principle and Suitability for Metallurgy
Ultrasonic level meters operate based on the time-of-flight of high-frequency sound waves (20kHz–1MHz). The sensor emits a pulse which reflects off the liquid surface and returns to the receiver. The level is calculated using:
L = E − (c × t / 2)
L: Liquid level, E: Empty tank height, c: Speed of sound, t: Round-trip time
Key Advantages for Metallurgy:
Non-Contact Design
Avoids direct exposure to molten metal, acids, or alkalis, prolonging sensor life.Corrosion Resistance
PTFE and ceramic probes withstand aggressive chemicals across a wide pH range.Strong Interference Immunity
Multi-pulse emission and noise filtering minimize effects from dust and steam.Real-Time and Remote Monitoring
Supports 4–20mA and RS485 output for seamless integration with DCS/PLC systems.
3. Application Cases in Steel Plants
✔ BOF Oxygen Lance Cooling Water Monitoring
Oxygen lances in converters require stable cooling. An ultrasonic level meter installed atop the water tank ensures timely water replenishment, reducing lance failure by 60% in one steel plant.
✔ Secondary Cooling Water in Continuous Casting
Level meters work with flow meters to dynamically adjust water levels, stabilizing pressure and improving slab surface quality. Results showed a 12% increase in surface pass rate.
✔ Sedimentation Tanks for Dust Removal Water
These tanks often contain metallic oxides that settle and clog the system. Ultrasonic level meters trigger automated sludge discharge based on real-time level changes, improving efficiency by 30% and reducing maintenance costs by 25%.
4. Installation & Maintenance Guidelines
Installation Tips:
Mount vertically at the center of the tank top to avoid sidewall reflections.
Maintain a minimum 50cm distance from the maximum liquid level to avoid blind zones (typically 0.3–0.5m).
Avoid electromagnetic interference (e.g., near furnaces or inverters); shielding may be required.
Adaptations for Harsh Environments:
For temperatures >80°C, use heat sinks or high-temperature probes rated up to 150°C.
In steam-heavy areas, install air purging systems to prevent condensation on the sensor.
Maintenance Practices:
Clean sensor surface monthly to remove dust and buildup.
Recalibrate sound velocity compensation quarterly for accuracy.
Annually inspect electronic components and replace if aging or damaged.
5. Limitations & Countermeasures
Limitation | Solution |
---|---|
Sound attenuation in steam >150°C | Use radar level meters or guided wave tubes |
Heavy foam or suspended particles | Add mechanical foam breakers or switch to low-frequency ultrasonic sensors |
Sealed tanks | Install flange-type units with dedicated sealing components |
6. Future Trends in Metallurgical Level Measurement
Multi-parameter Fusion
Integrated temperature and pressure sensing for comprehensive process insights.AI-Based Calibration
Machine learning models dynamically adjust for sound velocity deviations in complex conditions.Wireless IoT Connectivity
LoRa/NB-IoT communication enables wide-area, low-power wireless monitoring.
✅ Conclusion
Ultrasonic level meters have become a reliable solution for challenging liquid level measurement in the metallurgical industry. Their non-contact design, resistance to corrosion, and easy integration make them an ideal fit for high-temperature and dusty environments. With proper model selection, standardized installation, and routine maintenance, ultrasonic meters can significantly improve process reliability, safety, and automation. As smart manufacturing evolves, their role in digitalization and sustainability will only grow stronger.