In the petrochemical industry, crude benzene may not be the most expensive raw material, but it is certainly one of the most unpredictable variables in process control. It appears throughout key stages such as aromatization, hydrotreating, and storage & transport. Once out of control, crude benzene can impact not only production efficiency but also plant safety and regulatory compliance.
To control crude benzene, accurate and stable measurement is the first priority.
This article offers a systematic perspective on the difficulties of measuring crude benzene, compares mainstream measurement technologies, and provides targeted instrument selection recommendations. It is intended to serve as a practical reference for engineers and process designers.
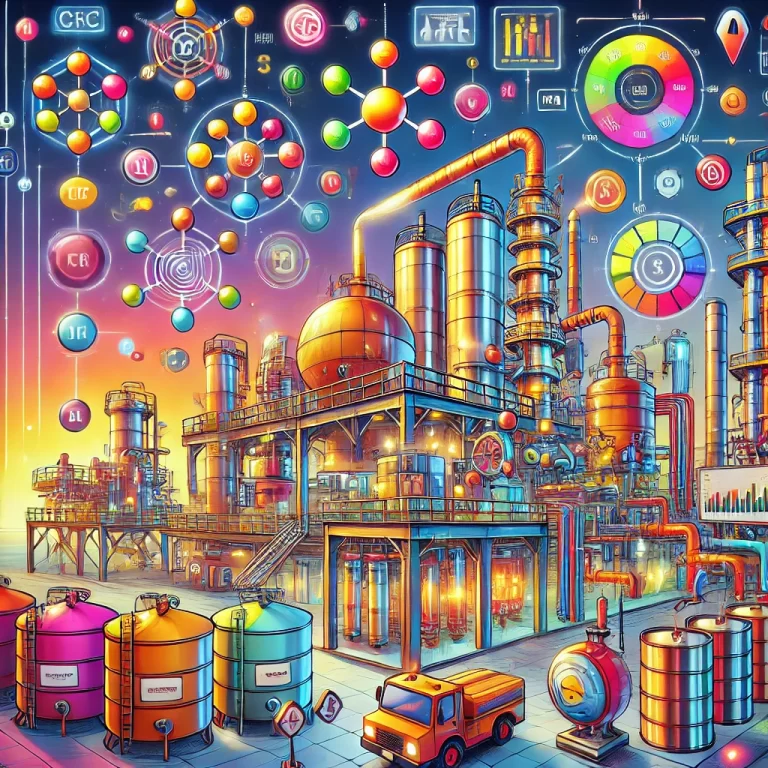
1. Why Is Crude Benzene Difficult to Measure?
Crude benzene is not a pure substance, but a complex mixture of aromatic hydrocarbons, mainly including:
Benzene
Toluene
Xylene
Styrene
Other light aromatics
This complexity, along with its volatile nature, introduces several measurement challenges:
⚠️ Key Challenges:
High Volatility
Leads to vapor interference, condensation on sensor surfaces, and potential sample loss.Moderate Corrosiveness
Causes long-term wear or degradation of metal components in sensors or piping.High Parameter Instability
Properties like density and dielectric constant fluctuate significantly with temperature changes, reducing measurement accuracy.
Due to these factors, crude benzene is considered a “high-uncertainty medium,” requiring instruments with excellent stability, interference immunity, and material compatibility.
2. Comparative Analysis of Measurement Technologies
Several analysis techniques are commonly used in crude benzene process control for composition and concentration monitoring:
Technique | Full Name | Advantages | Limitations |
---|---|---|---|
GC | Gas Chromatography | High resolution, precise quantification | Slow response, complex sampling system |
FTIR | Fourier Transform Infrared | Real-time data, non-destructive | Sensitive to humidity and contamination |
MS | Mass Spectrometry | High sensitivity, detailed analysis | Expensive, complex to maintain |
NIR | Near-Infrared Spectroscopy | Fast, in-line measurement | Requires calibration and compensation models |
🔍 Conclusion: No single method is sufficient for full lifecycle control under crude benzene’s complex conditions. A multi-technology, system-based approach is preferred.
3. Level Measurement – The Anchor of Control Systems
Level measurement plays a critical role in both material balance and as a trigger point for safety interlocks. Below are recommended solutions for different operating scenarios:
✅ Radar Level Transmitter (Top Recommendation)
Best For: Main storage tanks, process control tanks
Advantages:
Non-contact measurement
Immune to vapor interference
Accurate for low dielectric media
Recommended Specs:
80GHz FMCW radar
Probe Material: PTFE-coated or Hastelloy
Hazardous Zone Compatibility: Intrinsically safe (Ex ia) or Explosion-proof (Ex d)
Suitable for Zone 1 and Zone 2 classified areas
✅ Tuning Fork Level Switch (Safety Interlock Protection)
Best For: High/low level alarms, pump protection logic
Advantages:
Compact and fast response
Not affected by dielectric constant or temperature
Excellent corrosion resistance
Usage Tip:
Install at critical interlock points
Integrate into SIS (Safety Instrumented System) for redundancy
✅ Float Level Gauge (Cost-Effective Backup Option)
Best For: Secondary tanks, local indication, non-critical areas
Advantages:
Simple structure, easy to maintain
Budget-friendly
Precautions:
Not suitable for tanks with strong agitation
Material: 316L stainless steel or coated with anti-corrosion layer
4. Future Trends: Integrated & Intelligent Measurement Systems
Crude benzene measurement is transitioning from “point-based instrumentation” to “system-level data integration”. Today’s measuring devices are no longer just data providers—they play a role in:
Control logic execution
Fault prediction
Compliance traceability
✅ Next-Gen System Requirements:
Explosion-proof and corrosion resistance
Digital communication (HART, Modbus, PROFIBUS)
Built-in diagnostics and remote maintenance interface
Integration-ready with SIS, DCS, MES platforms for full closed-loop automation
📈 Modern measurement systems should aim for:
“Intelligent, stable, and predictive” rather than just “accurate.”
5. Final Thoughts
Crude benzene measurement is a cross-disciplinary task that connects chemical engineering, process safety, automation systems, and instrumentation. It is not only about choosing the right instrument, but also about designing a robust control architecture.
Instrument selection is just the first step. Building a smart, closed-loop system is the ultimate goal.
If you are currently working on crude benzene system design, plant retrofit, or have questions about sensor selection or data integration strategies — feel free to connect and discuss further.