Introduction
In industrial automation and process control, various types of switches are used to detect and control different parameters. Among them, limit switches and level switches play crucial roles but serve distinct purposes. While both involve switching mechanisms, their applications, working principles, and functions differ significantly. This article will explain the differences between a limit switch and a level switch, along with their types, applications, and working principles.
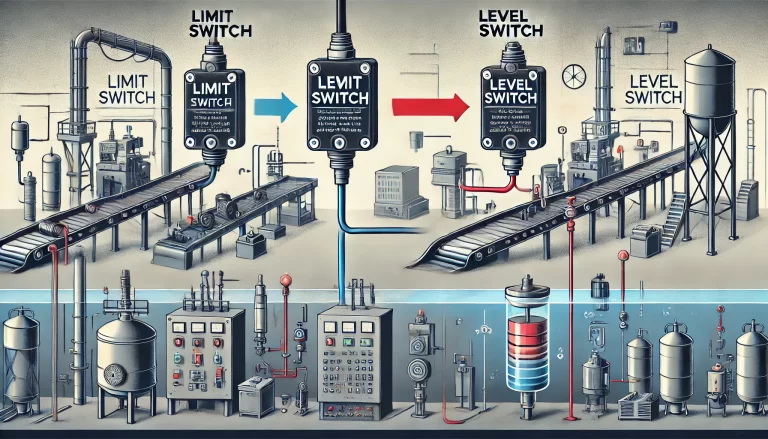
What is a Limit Switch?
A limit switch is an electromechanical device that detects the presence, position, or movement of an object in a mechanical system. It works by making or breaking an electrical connection when an object physically contacts its actuator.
Working Principle
The limit switch consists of an actuator, contacts, and a housing. When a moving object reaches a predefined position and comes into contact with the actuator, the switch is triggered, leading to an electrical response such as stopping or reversing motion, sending an alarm, or activating another process.
Types of Limit Switches
Mechanical Limit Switch – Uses a physical lever, roller, or plunger to detect movement.
Proximity Limit Switch – Detects objects without physical contact using magnetic, capacitive, or inductive sensors.
Micro Limit Switch – A compact version used in small-scale applications where space is limited.
Applications of Limit Switches
Detecting the open/closed state of machine components.
Position control in conveyor systems.
Safety interlocks in doors and automated systems.
Monitoring and restricting movement in industrial machines.
What is a Level Switch?
A level switch, also known as a liquid level sensor, is used to detect and monitor the level of a liquid or solid within a container, tank, or reservoir. It helps in maintaining the correct level by activating alarms or controlling pumps and valves.
Working Principle
A level switch operates based on physical, optical, or electronic detection of liquid or solid material levels. When the substance reaches a specified level, the switch activates, sending a signal to trigger a response, such as stopping a pump, opening a valve, or sounding an alarm.
Types of Level Switches
Float Level Switch – Uses a floating component that rises or falls with liquid levels to trigger a switch.
Capacitive Level Switch – Detects level changes based on changes in capacitance.
Ultrasonic Level Switch – Uses ultrasonic waves to detect liquid levels without physical contact.
Optical Level Switch – Uses light reflection and refraction principles to sense liquid levels.
Applications of Level Switches
Monitoring water levels in tanks and reservoirs.
Controlling the liquid level in chemical and fuel storage systems.
Preventing overflows in drainage and wastewater systems.
Managing the supply of liquids in food and beverage industries.
Key Differences Between Limit Switch and Level Switch
Feature | Limit Switch | Level Switch |
---|---|---|
Function | Detects the position of mechanical components | Detects the level of liquids or solids |
Working Mechanism | Activated by physical contact or proximity detection | Operates using float mechanisms, ultrasonic waves, capacitance, or optical sensors |
Primary Use | Position and motion control in mechanical systems | Liquid or solid level detection in containers or tanks |
Application Areas | Industrial automation, machine safety, conveyor systems | Water tanks, chemical storage, food processing, wastewater treatment |
Types | Mechanical, proximity, micro switches | Float, capacitive, ultrasonic, optical switches |
Conclusion
Though limit switches and level switches share a switching function, they serve entirely different purposes. Limit switches are used for detecting the position or movement of objects in mechanical systems, whereas level switches are designed to monitor and control liquid or solid levels in containers. Understanding the differences between these two types of switches helps in selecting the right switch for specific industrial applications, ensuring efficiency, reliability, and safety in operations.