Introduction to SIL (Safety Integrity Level)
Safety Integrity Level (SIL) is a key standard used to assess the reliability of Safety Instrumented Systems (SIS). SIL ensures that these systems effectively prevent hazardous events from occurring when failures happen. The design and assessment of SIL are based on failure rates, failure mode analysis, and the reliability requirements of the system. SIL is crucial in industries where safety is a priority, such as in chemical, petrochemical, and oil sectors.
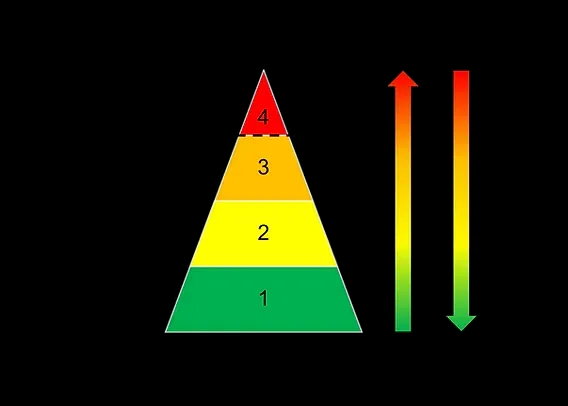
Fault Rate Requirements for SIL Instruments
According to the IEC 61508 and IEC 61511 standards, the fault rate for SIL-rated instruments is typically measured using Mean Time Between Failures (MTBF). Fault rate (λ) is the inverse of MTBF. Each SIL level has specific requirements for fault rates, which are outlined as follows:
For example, instruments such as the tuning fork liquid level switch and magnetic flap level meters are designed to meet SIL 2 and SIL 3 requirements. These systems meet these high standards to ensure their reliability and safety in industrial applications.
Fault Rate Calculation and Evaluation
The process of calculating and evaluating the fault rate of a system involves several methodologies. Among the most commonly used are Failure Mode and Effects Analysis (FMEA) and Fault Tree Analysis (FTA).
1. Failure Mode and Effects Analysis (FMEA):
FMEA is used to identify potential failure modes and evaluate their effects on the system. By analyzing these failure modes, FMEA helps to predict and mitigate potential issues before they occur, reducing the likelihood of system failure. This proactive approach allows for improvements in system design to enhance safety and reliability.
2. Fault Tree Analysis (FTA):
FTA is a tool used to analyze how different fault modes combine to lead to a dangerous event. By evaluating the fault tree, engineers can identify critical parts of the system and optimize the design to reduce the risk of failure. FTA is especially useful in complex systems where failures may not be immediately obvious but could combine to result in a catastrophic failure.
3. Redundancy Design:
To meet higher SIL levels, redundancy is often incorporated into the design of the system. This means duplicating key components or subsystems to ensure that the system continues to function even if one part fails. For instance, in systems requiring SIL 3 or SIL 4, a dual or triple redundancy design may be employed to drastically reduce the probability of failure and enhance system reliability.
Standards and Regulations for SIL Systems
The design and implementation of SIL-rated systems are governed by international standards to ensure they meet the required safety and reliability levels. Two key standards that guide these requirements are IEC 61508 and IEC 61511.
IEC 61508: Functional Safety of Electrical, Electronic, and Programmable Electronic Safety-related Systems
IEC 61508 provides the foundational safety requirements for all types of safety-related control systems. It covers the hardware, software, and management aspects, establishing the necessary conditions for designing, assessing, and maintaining safety systems. It specifies the failure probabilities of safety systems to ensure that their safety functions meet the intended objectives.
For SIL systems, this standard defines how to calculate and evaluate system reliability, as well as how to design equipment and systems that meet SIL requirements. It is applicable across various industries and focuses on minimizing risks by controlling hazards through the implementation of safe, reliable systems.
IEC 61511: Functional Safety – Safety Instrumented Systems for the Process Industry Sector
IEC 61511 is specifically tailored for the process industries, such as chemicals, petrochemicals, and oil and gas. This standard outlines the safety requirements for SIS in these industries, emphasizing the importance of system reliability in preventing hazardous events. The selection and requirement of SIL levels depend on the risk assessment and potential hazardous scenarios. Based on these assessments, the appropriate SIL level is chosen to ensure the system can prevent potential hazards effectively.
SIL Certification Process
SIL certification is essential for verifying that equipment and systems meet the safety requirements defined in the IEC 61508 or IEC 61511 standards. The certification process must be performed by an independent third-party organization, which evaluates the system’s design and operational effectiveness.
For high SIL levels, systems must be designed with redundancy, undergo regular maintenance, and implement fault detection and repair mechanisms to ensure continued reliability and compliance with safety standards.
Conclusion
The fault rate requirements for SIL instruments are strictly defined by the IEC 61508 and IEC 61511 standards. Each SIL level corresponds to specific fault rate ranges, from SIL 1 with the lowest requirements to SIL 4 with the highest. When designing and implementing systems, these standards ensure that the system’s reliability and safety are thoroughly validated through comprehensive evaluations and certifications.
For high SIL-level systems, redundancy design, regular maintenance, and fault detection mechanisms are critical to ensuring the system meets the required standards and continues to function safely. By following these guidelines, industries can significantly reduce the risk of hazardous events, ensuring safer operations in high-risk environments.