For any company, ensuring the safety of its employees and maintaining a safe production environment are of utmost importance. Many factories are continually striving to minimize the time workers spend in hazardous areas, and one of the most effective measures to achieve this goal is the use of automated instrumentation and control equipment. These instruments help reduce the need for manual operations in dangerous environments, thereby minimizing risks and improving overall safety.
The Dangers of Manual Operations in Hazardous Areas
In industries involving large tanks or vessels, workers often need to access high areas to perform tasks such as measuring liquid levels. For example, when measuring the liquid level inside a storage tank, workers must often climb to the top of the tank, open the hatch, and take measurements manually. Not only does this require working at heights, which presents its own risks, but workers may also be exposed to hazardous vapors from the stored liquid, increasing the chances of injury.
The more frequently these measurements are taken, the longer the exposure time, and consequently, the higher the risk of accidents. Human error, such as misreading gauges, writing down incorrect values, or even simple oversight, can also contribute to inaccuracies in the data. These factors further increase the likelihood of mistakes, which can lead to dangerous situations.
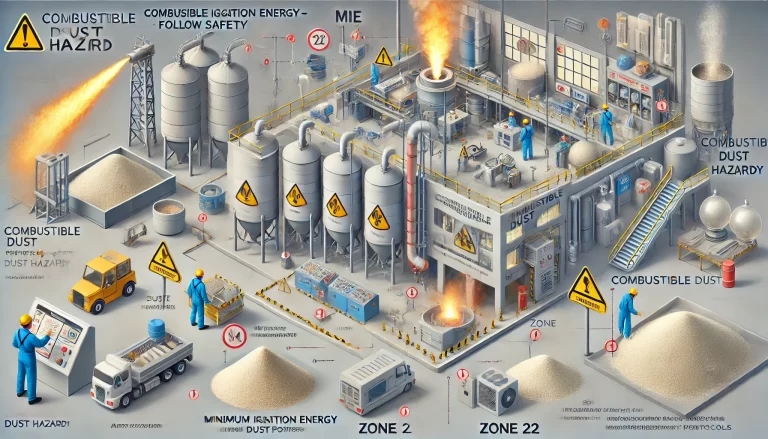
The Solution: Automated Instrumentation and Control Systems
To address these challenges, industries are increasingly turning to automated instrumentation to reduce the need for manual interventions in hazardous environments. Instruments such as pressure transmitters, level transmitters, temperature transmitters, humidity transmitters, soil moisture transmitters, and differential pressure transmitters are capable of performing critical measurements such as pressure, liquid levels, temperature, humidity, soil moisture, and differential pressure without requiring direct human involvement in dangerous areas.
These instruments collect data remotely, which is then transmitted to a central control room or resource management system. By replacing manual readings with automated sensors, companies can minimize human presence in hazardous zones, ensuring that workers do not have to be exposed to dangerous conditions unnecessarily. Moreover, the data collected by these instruments is more accurate and timely, which helps improve decision-making processes and reduces the risk of errors caused by human factors.
Key Benefits of Automated Instrumentation
Safety Improvement: The most significant benefit of automated instruments is the reduction of risk for employees. By eliminating the need for workers to enter hazardous areas for routine measurements, the chances of accidents occurring are greatly reduced. Workers can remain in safe, controlled environments while still having access to accurate data.
Increased Efficiency: Automated systems provide real-time data, allowing for faster response times to potential issues. This leads to quicker decision-making and improves overall operational efficiency. The use of automated instruments also reduces the need for manual labor, which can free up resources for other critical tasks.
Accurate Data Collection: Unlike manual readings, automated instrumentation ensures that data is accurate, precise, and consistent. There is no risk of human error due to misreading gauges, incorrect entries, or poor handwriting. The data collected by these instruments can be analyzed instantly, providing insights that lead to better control and optimization of industrial processes.
Cost Reduction: Although the initial investment in automated instruments may be high, in the long run, they can help reduce operational costs. Fewer accidents mean lower costs related to insurance, medical bills, and potential legal liabilities. Additionally, automation reduces the need for a large workforce, further cutting down on labor costs.
Looking Toward the Future
As technology continues to evolve, the role of instrumentation in industrial safety is likely to become even more critical. Advanced sensors and control systems will increasingly incorporate features like predictive maintenance, where instruments can alert operators to potential failures before they happen, further enhancing safety. Additionally, the integration of the Internet of Things (IoT) in industrial settings will allow for even greater connectivity and real-time monitoring of operations across different locations.
In conclusion, the integration of automated instrumentation in hazardous work environments not only improves safety but also boosts operational efficiency and reduces the likelihood of accidents. By minimizing human exposure to dangerous areas and ensuring more accurate data collection, businesses can ensure a safer and more productive working environment.