Mass flow meters are essential instruments in industries where precise measurement of the mass of a fluid (liquid or gas) passing through a system is required. These devices are widely used in applications ranging from chemical processing to oil and gas, food and beverage production, and pharmaceuticals. For accurate and reliable performance, mass flow meters must be regularly calibrated using high-precision equipment. Calibration ensures that the flow meter provides correct mass flow readings under a variety of operational conditions.
1. Standard Mass Flow Meters
The primary equipment for calibrating mass flow meters is a standard mass flow meter, which is a highly accurate and reliable device. These standard meters are used to compare and verify the accuracy of the meter under test (MUT).
Typically, standard mass flow meters are selected based on their accuracy, measurement range, and compatibility with the type of fluid being measured. These devices often include technologies like Coriolis or thermal mass flow sensors, which are considered to provide some of the most accurate flow measurements available.
Standard meters are typically calibrated to a higher precision than the flow meter being tested, and they serve as the benchmark for the verification process.
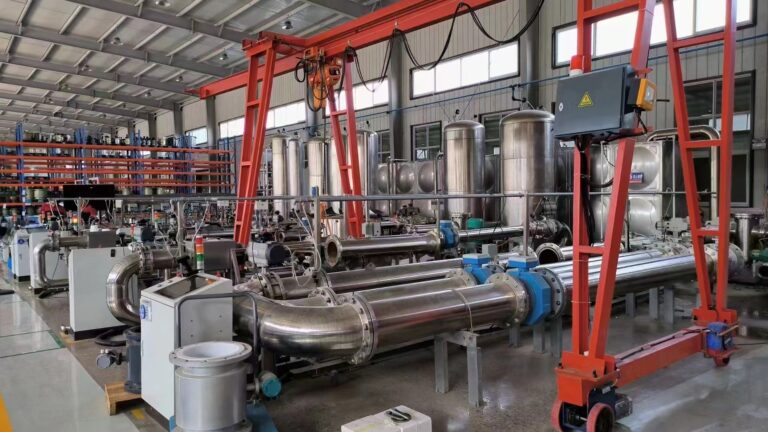
2. Flow Standards and Reference Instruments
Flow standards are used to provide a reference flow rate for calibration. These instruments are generally more accurate than the flow meter under test and are critical in ensuring that the test results are reliable.
Types of Flow Standards:
Volumetric Flow Standards: These include devices that measure the volume of a fluid over a given period. For instance, a positive displacement meter or piston prover can be used to determine volumetric flow, which can then be converted into mass flow using the density of the fluid.
Coriolis Mass Flow Standards: These devices are often used in high-precision applications and directly measure the mass flow by detecting changes in the oscillation of a tube carrying the fluid.
Turbine Flow Meters: In certain applications, turbine flow meters with calibrated rotors may be used as a reference. These can be especially useful for testing gases at lower flow rates.
Ultrasonic Flow Meters: These meters, particularly in their differential form, can also be used as reference meters for flow testing. They use the Doppler effect or time-of-flight measurements to determine flow rate.
3. Static and Dynamic Calibration Devices
Calibration can be carried out either statically or dynamically, depending on the nature of the fluid and the meter being calibrated.
Static Calibration:
In static calibration, a known and constant mass of fluid is measured using a precise, known volume or mass. One common approach involves using gravimetric calibration, where the mass of the fluid is measured directly using scales as it flows into a collection vessel.
Volumetric containers and weighing scales are often used in this type of calibration. The fluid’s density is assumed constant, or it is measured directly at the time of calibration to convert volume flow into mass flow.
Laboratory calibration systems often rely on static methods when precise control over variables like temperature and pressure is needed.
Dynamic Calibration:
Dynamic calibration involves testing the flow meter under operating conditions. This method requires more complex setups, as it involves flowing a controlled amount of fluid through the system under actual flow conditions. This ensures that the flow meter can be tested under the same circumstances in which it will be used in the field.
In dynamic calibration, flow calibration rigs and test loops are often employed. These rigs include valves, pumps, and flow meters that can simulate real-world flow conditions, such as fluctuations in pressure, temperature, and flow rate.
4. Gas and Liquid Flow Calibration Equipment
The calibration equipment used varies based on whether the meter is intended for gas or liquid flow. Each type of fluid behaves differently, which influences the calibration procedure.
Gas Flow Calibration Equipment:
Gas Flow Provers: For gases, devices like gas displacement provers or gas cylinders are often used to generate a known gas flow, which can be calibrated against the mass flow meter.
Thermal Mass Flow Standard: A highly accurate standard for calibrating gas meters, especially in cases where the meter needs to measure gases with varying temperatures and pressures.
Differential Pressure Meters: These can also be used as reference devices for calibrating gas flow meters under specific conditions of pressure and temperature.
Liquid Flow Calibration Equipment:
Piston Provers: For liquids, piston provers are commonly used. These systems involve a piston moving through a fixed volume, allowing for very precise measurement of the volume and, by extension, the mass flow.
Rotary Displacement Meters: These are used for measuring liquid flow and are sometimes used as standard reference devices in liquid flow calibration.
5. Temperature and Pressure Standard Devices
Since the mass flow of fluids is highly dependent on both temperature and pressure, maintaining accurate temperature and pressure readings is essential during the calibration process. To ensure consistency and accuracy, specialized instruments are used to measure these variables.
High-precision Temperature Sensors: Thermocouples or RTDs (resistance temperature detectors) are commonly used to monitor the temperature of the fluid, ensuring that the flow meter is calibrated under accurate temperature conditions.
High-accuracy Pressure Transducers: Pressure is another critical variable, especially in gas flow measurements. Pressure transducers that offer high precision are used to monitor the pressure within the system during calibration.
These devices allow the technician to ensure that the mass flow meter is being tested under controlled conditions, with the results adjusted for changes in temperature and pressure as necessary.
6. Data Acquisition and Analysis Systems
Modern calibration often involves the use of data acquisition (DAQ) systems that collect and analyze real-time data from both the mass flow meter and the reference devices. These systems ensure that the calibration process is automated, consistent, and precise.
Data Loggers: These devices continuously record readings from the calibration equipment, ensuring that all relevant variables (flow rate, pressure, temperature, etc.) are documented for further analysis.
Analysis Software: Specialized software tools are often used to process the data collected during calibration, providing insights into the performance of the mass flow meter and identifying any discrepancies that need to be addressed.
These systems improve efficiency, allow for better tracking of calibration history, and help in generating certificates or reports that can be used to ensure compliance with regulatory standards.
Conclusion
The calibration of mass flow meters is a critical process in ensuring accurate flow measurements, which are essential in many industries. A variety of specialized equipment and techniques are used to calibrate these meters, including standard mass flow meters, flow standards, calibration rigs, and temperature/pressure monitoring devices. By using high-precision instruments and systematic procedures, engineers can ensure that mass flow meters continue to perform optimally, providing reliable measurements for various industrial applications. Regular calibration not only improves measurement accuracy but also enhances process efficiency and safety, making it a cornerstone of fluid measurement technology.