Static electricity bonding for flange bolts is an essential safety measure, especially in industrial piping systems that transport flammable or explosive materials. Proper bonding ensures that any potential static charge accumulation is safely dissipated, preventing the risk of sparks that could lead to hazardous incidents. This article provides a comprehensive guide on how to perform static electricity bonding for flange bolts.
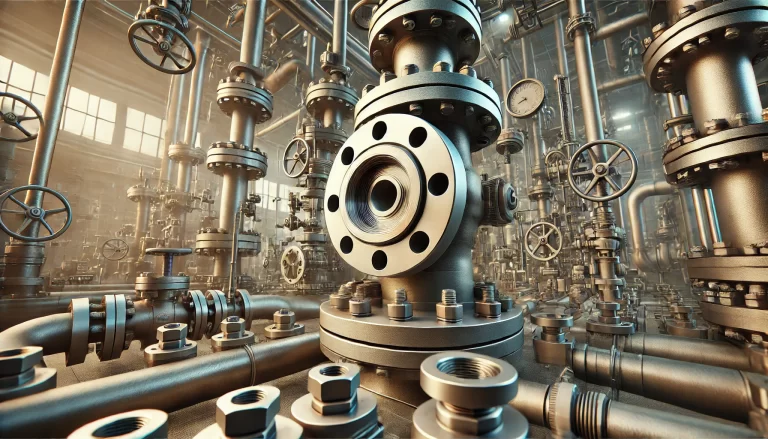
1. Understanding the Importance of Static Bonding
In industrial environments, such as oil and gas, chemical processing, and pharmaceutical industries, the movement of liquids or gases can generate static electricity. If not properly managed, this static buildup can discharge in the form of sparks, posing serious safety hazards. Flange bolts, which connect sections of piping, must be electrically bonded to ensure continuity and safe dissipation of charges.
2. Materials and Equipment Required
Before beginning the bonding process, the following materials and tools are necessary:
Bonding Straps/Wires: Copper braided straps, stainless steel braided straps, or copper core insulated wires.
Fasteners: Stainless steel bolts, nuts, and washers for secure attachment.
Protective Coating: Anti-corrosion paint or insulating sleeves.
Tools: Wire strippers, wrenches, crimping tools, and a multimeter for resistance testing.
3. Step-by-Step Procedure for Bonding
Step 1: Preparation
Inspect the Flange Surface: Ensure the flange surfaces are clean, free of rust, paint, and debris to ensure good electrical contact.
Measure Resistance: Use a multimeter to check the initial electrical resistance across the flange to determine the need for bonding.
Step 2: Selection of Bonding Method
There are several common methods for bonding flange bolts:
Welding Method: Attach a bonding strap by welding it directly to the flange; this method provides a permanent solution.
Bolted Connection: Secure the bonding wire using terminal lugs fastened with bolts and washers.
Clamp-on Straps: Use specially designed clamps that grip onto the flange bolts without requiring modification.
Step 3: Installation Process
Attach Bonding Strap: Securely fasten one end of the bonding strap to one flange and the other end to the adjoining flange using bolts or welding.
Ensure Tight Connections: Use stainless steel nuts and washers to avoid loosening over time.
Protect the Connection: Apply anti-corrosion coating or heat-shrink tubing to prevent degradation over time.
Step 4: Testing and Verification
Check Electrical Continuity: Use a multimeter to measure the resistance across the flanges; the resistance should typically be below 0.03 ohms.
Perform a Visual Inspection: Ensure no loose connections or exposed conductive parts.
Conduct Spark Tests: For high-risk environments, spark testing can be conducted to confirm static dissipation.
4. Installation Best Practices
To achieve the best results, consider the following best practices:
Multiple Bonding Points: For large-diameter pipelines, install multiple bonding points for better static dissipation.
Regular Maintenance: Inspect bonding straps regularly to check for wear, corrosion, or breakage.
Compliance with Standards: Adhere to industry standards such as:
NFPA 77: Recommended Practice on Static Electricity
API 2003: Protection Against Ignitions Arising Out of Static, Lightning, and Stray Currents
OSHA 29 CFR 1910.106: Flammable Liquids Regulations
5. Common Challenges and Troubleshooting
Some challenges faced during the bonding process include:
Corrosion Issues: Select corrosion-resistant materials like stainless steel or coated copper to prevent degradation.
Loose Connections: Use lock washers and secure tightening to prevent loosening due to vibrations.
Incorrect Resistance Readings: Ensure proper surface preparation and contact point selection to achieve accurate readings.
6. Conclusion
Proper static electricity bonding for flange bolts is crucial for ensuring operational safety in industrial piping systems. By following a systematic approach—starting from preparation, installation, and testing—industries can effectively mitigate static-related hazards. Regular inspections and adherence to industry standards further contribute to long-term safety and reliability.