In industrial processes, accurate flow measurement is crucial for ensuring process quality and operational efficiency. Metal rotameters, also known as metal tube variable area flowmeters, are widely used due to their robust structure, reliable operation, and wide applicability. However, a common question arises during installation: do metal rotameters require straight pipe sections for optimal performance? This article explores the significance of straight pipe sections and provides practical guidelines for proper installation.
The Role of Straight Pipe Sections in Flow Measurement
Flowmeters determine the flow rate by measuring physical quantities, such as velocity or pressure differential, as fluid moves through the pipeline. For precise measurement, the fluid must flow in a stable and uniform manner before entering the flowmeter. Straight pipe sections help achieve this by stabilizing the fluid flow and reducing disturbances caused by factors such as bends, valves, or obstructions upstream.
Straight pipe sections minimize turbulence and ensure that the flow profile becomes fully developed, which is essential for achieving accurate readings. Without these sections, the measurement may be compromised, leading to errors and inconsistent performance.
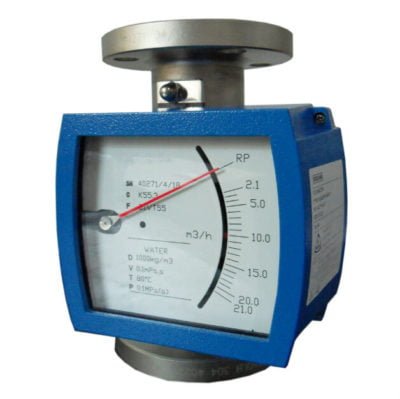
Relationship Between Metal Rotameters and Straight Pipe Sections
Metal rotameters operate on the principle of a float moving within a conical tube. The float’s position, which is determined by the balance between the upward flow force and the downward gravitational force, corresponds to the flow rate. For the float to accurately reflect changes in flow, the incoming fluid must be stable and free of turbulence.
To ensure this stability, straight pipe sections are necessary. Typically, the following guidelines are recommended for the installation of straight pipe sections:
Upstream (inlet) straight pipe section: At least 10 times the nominal diameter (10×DN) of the pipeline.
Downstream (outlet) straight pipe section: At least 5 times the nominal diameter (5×DN) of the pipeline.
These proportions ensure that the fluid is conditioned properly before and after passing through the rotameter, thereby enhancing measurement accuracy and consistency.
Practical Installation Tips for Metal Rotameters
Besides incorporating straight pipe sections, the following installation considerations are critical for achieving optimal performance:
Vertical Alignment:
Metal rotameters must be installed vertically, with the flow direction from bottom to top. The maximum allowable deviation is 2 degrees. A tilted installation can cause inaccuracies in the float’s movement.
Pipeline Cleaning:
Before installation, thoroughly clean the pipeline to remove welding residues, dirt, and other debris that could interfere with the flow or damage the rotameter.
Use of Filters or Magnetic Separators:
If the medium contains particulates or magnetic debris, install a filter or magnetic separator upstream to protect the rotameter and ensure smooth operation.
Control Valve Placement:
Place control valves downstream of the rotameter to maintain stable flow conditions. Adjusting a control valve located upstream can introduce turbulence, affecting measurement accuracy.
Address Pulsating or Multiphase Flow:
For applications involving pulsating or multiphase flow, install a flow damper upstream to reduce fluctuations and stabilize the measurement conditions.
Case Study: The Impact of Straight Pipe Sections
A chemical processing plant faced challenges with inconsistent flow readings from its metal rotameters. After investigation, it was discovered that the upstream piping lacked sufficient straight pipe sections, and the control valve was improperly installed upstream of the flowmeter.
By adding straight pipe sections (12×DN upstream and 6×DN downstream) and relocating the control valve to the downstream side, the plant achieved a 15% improvement in measurement accuracy. This adjustment not only reduced operational inefficiencies but also extended the lifespan of the rotameters.
Why Straight Pipe Sections Matter
Straight pipe sections do more than stabilize fluid flow; they also protect the internal components of the rotameter from premature wear caused by turbulence or debris. Over time, this translates to reduced maintenance costs and improved reliability. Moreover, compliance with recommended installation practices ensures consistency and repeatability in flow measurement, which is essential for critical industrial processes.
Conclusion
Straight pipe sections are indispensable for optimizing the performance of metal rotameters. They provide the stable flow conditions needed for precise and reliable measurement, while also safeguarding the equipment. By adhering to installation guidelines, such as incorporating appropriate straight pipe lengths and ensuring vertical alignment, users can maximize the accuracy and longevity of their flowmeters. In practice, these seemingly small adjustments can have a significant impact on overall operational efficiency.
When planning the installation of a metal rotameter, remember: the investment in proper straight pipe sections and thoughtful setup pays off in the form of accurate measurements and long-term reliability.