Instrument calibration and measurement procedures are essential for ensuring the accuracy and reliability of equipment used in laboratories, calibration facilities, and even within industrial enterprises. Adhering to proper calibration guidelines is crucial for maintaining quality standards and ensuring traceability of measurements. This article provides a detailed overview of the purpose, responsibilities, and processes involved in instrument calibration and measurement.
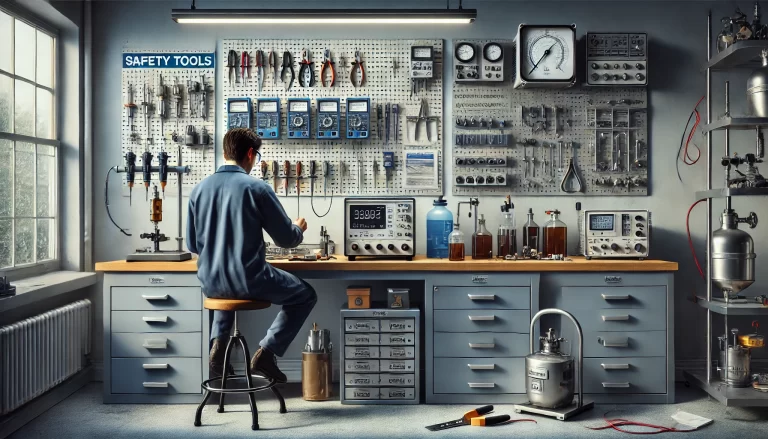
Purpose of Instrument Calibration and Measurement Procedures
The primary objective of calibration procedures is to standardize the calibration work conducted by institutions, laboratories, and enterprises, ensuring the reliability and consistency of measurement instruments. These procedures are designed to:
Ensure Accuracy: Maintain the precision of measurement instruments to ensure they meet operational standards.
Promote Reliability: Facilitate consistent results in measurements, regardless of the location or operator.
Enable Traceability: Create records that enable the traceability of measurements back to national or international standards.
Support Maintenance: Ensure instruments remain in good working condition through regular checks and calibrations.
The scope of these procedures extends beyond laboratories and calibration institutions to include enterprise environments where instruments play a critical role in quality control.
Responsibilities in Instrument Calibration
To maintain an effective calibration system, clear roles and responsibilities must be assigned:
Instrument Users:
Conduct daily maintenance and proper handling of measurement instruments.
Report anomalies or signs of wear and tear promptly.
Quality Assurance/Control Departments:
Conduct periodic checks to ensure measurement instruments remain accurate and functional.
Monitor compliance with calibration schedules and procedures.
Calibration Engineers:
Execute calibration tasks following established standards.
Document calibration results in detailed reports, ensuring compliance with traceability requirements.
Enterprise/Facility Management:
Oversee the calibration program to ensure adherence to industry standards and regulations.
Allocate resources for the acquisition and maintenance of calibration tools and equipment.
Steps in the Instrument Calibration Process
1. Establishing Calibration Schedules:
Regular Calibration: Instruments are calibrated on a fixed schedule, typically every 6 months, depending on their usage and criticality.
Special Calibration: Performed in response to specific needs, such as after significant repairs, environmental changes, or customer requirements. This calibration may deviate from the regular schedule.
2. Preparing for Calibration:
Inspect the instrument for visible damage or contamination before calibration begins.
Verify that all accessories required for calibration are available and in good condition.
Ensure the environment meets the required standards for temperature, humidity, and vibration to avoid interference.
3. Performing Calibration:
Calibration engineers use reference standards that are traceable to national or international measurement systems.
Adjust the instrument as needed to minimize deviations from reference values.
Repeat measurements multiple times to confirm consistency and reduce uncertainty.
4. Documenting Results:
Record all measurement data and adjustments in a calibration certificate.
Include detailed information such as instrument details, environmental conditions, reference standards, and observed deviations.
Retain these records for traceability and future audits.
5. Post-Calibration Actions:
Label the instrument with a calibration status sticker, indicating the date of calibration and next due date.
Archive calibration certificates for reference.
Review calibration data to decide whether the instrument requires additional repairs or replacement.
Importance of Calibration Certificates
Calibration certificates serve as official documentation of the calibration process. These certificates must include:
Instrument identification details.
Calibration date and validity period.
Environmental conditions during calibration.
Reference standards and their traceability information.
Measurement results and uncertainties.
Recommendations for corrective actions if needed.
Enterprises should analyze the calibration certificate to determine the instrument’s suitability for continued use. If self-calibration is performed internally, a structured self-calibration procedure must be documented and followed to ensure consistency and reliability.
Conclusion
Proper instrument calibration and measurement procedures are indispensable for ensuring the accuracy and reliability of measurement instruments. By adhering to established guidelines, organizations can maintain their measurement systems’ integrity, reduce risks, and meet regulatory and operational requirements. The roles and responsibilities of users, quality control personnel, and calibration engineers are integral to the success of the calibration program. Regular reviews, coupled with thorough documentation, ensure the traceability and reliability of calibration processes, ultimately supporting the broader goals of quality and efficiency.