Pressure transmitters are among the most commonly used sensors in industrial automation control systems. Piezoresistive, capacitive, and monocrystalline silicon resonant pressure transmitters represent three primary types, each with unique principles, advantages, disadvantages, and application scenarios. This article provides a detailed comparison to help choose the most suitable option for specific needs.
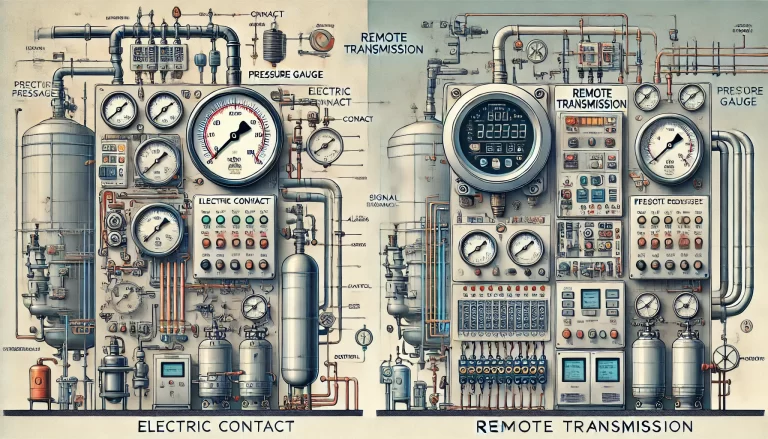
1. Piezoresistive Pressure Transmitters
Working Principle
Piezoresistive pressure transmitters utilize the piezoresistive effect of monocrystalline or polycrystalline silicon to convert mechanical deformation caused by pressure into electrical signals:
Pressure is applied to a sensing diaphragm, causing elastic deformation.
The strain changes the resistance of the piezoresistive elements embedded in the diaphragm.
These resistance changes are converted into electrical voltage signals using a Wheatstone bridge circuit, producing outputs proportional to the applied pressure.
Features
Advantages:
High precision and accuracy.
Simple structure and cost-effective manufacturing.
Fast response time, suitable for dynamic pressure measurements.
Disadvantages:
Highly sensitive to temperature variations, requiring compensation.
Vulnerable to mechanical vibrations.
Long-term stability is moderate, with notable signal drift over time.
Applications
Measurement of liquid, gas, and steam pressures.
Widely used in applications like water treatment, automotive oil pressure monitoring, and refrigeration systems.
2. Capacitive Pressure Transmitters
Working Principle
Capacitive pressure transmitters rely on changes in capacitance caused by pressure-induced deformation:
Pressure deforms a metal or non-metal diaphragm.
The diaphragm and a fixed electrode form a variable capacitor, where pressure-induced deformation alters the capacitance.
The capacitance change is processed into electrical signals proportional to the pressure.
Features
Advantages:
High sensitivity, particularly for small pressure measurements.
Minimal temperature effects and excellent long-term stability.
Suitable for both high and low-pressure measurements.
Disadvantages:
Sensitive to environmental factors like contaminants and humidity, requiring protective designs.
Complex signal processing increases cost.
Slower response speed compared to piezoresistive models.
Applications
Precision pressure measurement in medical equipment and food processing.
Harsh environments with high temperatures, pressures, or corrosive conditions, such as in chemical and petroleum industries.
3. Monocrystalline Silicon Resonant Pressure Transmitters
Working Principle
Monocrystalline silicon resonant pressure transmitters measure pressure through changes in resonant frequency:
Micro-resonators are fabricated on a silicon diaphragm.
Pressure-induced stress on the diaphragm alters the resonators’ stress state, affecting their resonant frequency.
The frequency changes are converted into precise pressure readings using advanced algorithms.
Features
Advantages:
Extremely high accuracy.
Outstanding long-term stability with minimal drift.
Excellent resistance to electromagnetic interference and environmental disturbances.
Suitable for extreme conditions like high temperatures and pressures.
Disadvantages:
High manufacturing complexity and cost.
Slower response time, better suited for static or quasi-dynamic pressure measurements.
Intricate calibration and design processes.
Applications
High-precision and high-reliability applications, such as oil and gas pipeline monitoring and aerospace pressure measurement.
Research and metrology equipment.
Comparison Table
Parameter | Piezoresistive | Capacitive | Monocrystalline Silicon Resonant |
---|---|---|---|
Working Principle | Piezoresistive effect | Capacitance variation | Resonant frequency variation |
Accuracy | High | High | Extremely high |
Long-Term Stability | Moderate, significant drift | Excellent, minimal drift | Outstanding, negligible drift |
Temperature Influence | High, requires compensation | Low | Very low, excellent resistance |
Cost | Low | Medium | High |
Interference Resistance | Moderate | Moderate | Excellent |
Pressure Range | Manufacturer-dependent | Manufacturer-dependent | Manufacturer-dependent |
Response Speed | Fast | Moderate | Slightly slower |
Conclusion and Recommendations
Piezoresistive Pressure Transmitters are suitable for applications requiring high response speed and cost-effectiveness, such as automotive and industrial processes.
Capacitive Pressure Transmitters excel in precision and stability, making them ideal for medical and harsh industrial environments.
Monocrystalline Silicon Resonant Pressure Transmitters are the best choice for demanding scenarios requiring high precision, stability, and interference resistance, such as oil, gas, and aerospace applications.
In summary, the optimal choice depends on the specific requirements of the application, such as accuracy, environment, budget, and response speed. Incorporating the latest advancements and market trends can further refine the selection process to ensure maximum efficiency and reliability.