Valve manifolds are essential industrial components used to integrate multiple valves for controlling, regulating, and distributing media. They play a crucial role in piping systems and industrial equipment. This article provides a comprehensive guide to help beginners understand valve manifolds, focusing on the widely used two-, three-, and five-valve types.
What is a Valve Manifold?
A valve manifold is a compact assembly comprising multiple valves combined into a single unit. It is designed to streamline operations and enhance control in industrial systems.
- Essence: It consolidates multiple independent valves into a cohesive and manageable structure.
- Shape: Typically, it is a metal block or modular assembly featuring ports for inlets, outlets, and valves.
- Materials: Common materials include stainless steel, carbon steel, and aluminum alloys, selected based on the application environment.
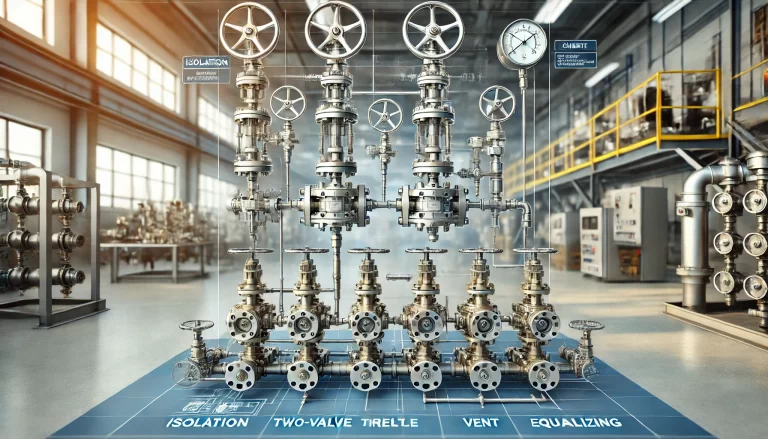
Key Functions of Valve Manifolds
Simplifying Piping Systems
By integrating multiple valves, valve manifolds reduce the number of pipes and connections, minimizing complexity and leakage risks.Saving Space
Compact design reduces the overall footprint, making it ideal for installations in confined areas.Ease of Operation and Maintenance
Centralized control and maintenance save time compared to inspecting individual valves.Enhancing Safety
Manifolds are often used to isolate equipment or media, enabling maintenance without compromising operational safety.Meeting Multifunctional Needs
Valve manifolds facilitate media flow control, isolation, venting, and switching within a single device.
Types of Valve Manifolds
Valve manifolds can be categorized by the number of valves, installation methods, applications, and materials.
1. By Number of Valves
- Two-Valve Manifold: Commonly used in pressure measurement, featuring an isolation valve and a vent valve.
- Three-Valve Manifold: Often paired with differential pressure transmitters, incorporating two isolation valves and one equalizing valve.
- Five-Valve Manifold: Adds two vent valves to the three-valve setup for enhanced functionality and flexibility.
2. By Installation Method
- Direct-Mount: Installed directly onto a transmitter or equipment, reducing connectors and simplifying installation.
- Remote-Mount: Positioned away from equipment, connected via pipes.
3. By Application
- Measurement Manifold: Connects instruments like transmitters to process pipes.
- Distribution Manifold: Distributes media to multiple outlets.
- Regulating Manifold: Controls media flow, pressure, or temperature.
4. By Material
- Stainless Steel: Corrosion-resistant, ideal for chemical and pharmaceutical industries.
- Carbon Steel: Suitable for standard environments.
- Special Alloys: Designed for highly corrosive or high-temperature conditions.
Detailed Overview of Common Valve Manifolds
Two-Valve Manifold
Definition
A two-valve manifold consists of an isolation valve and a vent valve. It is primarily used with pressure transmitters.
Structure and Function
- Isolation Valve: Disconnects the pressure transmitter from the process pipe for maintenance.
- Vent Valve: Releases residual media inside the transmitter for calibration or safety.
Operation Steps
- Normal Operation:
Open the isolation valve to connect the transmitter to the process; keep the vent valve closed. - Maintenance/Calibration:
Close the isolation valve, open the vent valve to release pressure, and perform required operations.
Applications
- Pressure monitoring in oil and gas pipelines.
- Boiler pressure control.
Three-Valve Manifold
Definition
A three-valve manifold comprises two isolation valves and one equalizing valve, commonly paired with differential pressure transmitters.
Structure and Function
- Two Isolation Valves: Separate the high-pressure and low-pressure sides of the system from the transmitter.
- Equalizing Valve: Balances pressure between the two sides to protect the transmitter from damage caused by excessive differential pressure.
Operation Steps
- Normal Operation:
Open both isolation valves and close the equalizing valve to allow differential pressure measurement. - Maintenance/Calibration:
Close both isolation valves, then open the equalizing valve to equalize pressure before performing calibration.
Applications
- Flow measurement using orifice plates or Venturi tubes.
- Liquid level monitoring in storage tanks.
Five-Valve Manifold
Definition
The five-valve manifold extends the three-valve design by adding two vent valves for advanced functionalities.
Structure and Function
- Isolation Valves and Equalizing Valve: Same as in a three-valve manifold.
- Two Vent Valves: Individually connected to the high- and low-pressure sides to release residual media or remove air bubbles.
Operation Steps
- Normal Operation:
Open isolation valves, close the equalizing and vent valves. - Maintenance/Calibration:
Close isolation valves, open the equalizing valve, then use the vent valves to purge or release pressure.
Applications
- Differential pressure systems requiring frequent calibration.
- Gas or steam applications to eliminate air or gas bubbles.
Choosing the Right Valve Manifold
Measurement Type
Use a two-valve manifold for simple pressure measurements and three- or five-valve manifolds for differential pressure applications.Maintenance Needs
For frequent calibration, a five-valve manifold offers added flexibility and ease of operation.Environmental Complexity
For high-pressure or high-safety applications, opt for a five-valve manifold.Budget and Space Constraints
Two-valve manifolds are cost-effective and compact, ideal for simpler systems.
Conclusion
Valve manifolds are indispensable in industrial process control, offering safety, efficiency, and multifunctionality. Two-, three-, and five-valve manifolds address different operational requirements, making them versatile tools for applications ranging from oil and gas to water treatment. For learners and practitioners, hands-on experience and real-world case studies are invaluable for mastering installation, operation, and maintenance.