Introduction
M-Bus (Meter-Bus) and Modbus are two widely adopted communication protocols in industrial and automation systems. Despite their shared goal of enabling efficient communication between devices, their design principles, application scenarios, and features differ significantly. This article provides an in-depth explanation of these protocols, highlights their unique characteristics, and offers a side-by-side comparison to help practitioners determine the best protocol for specific use cases.
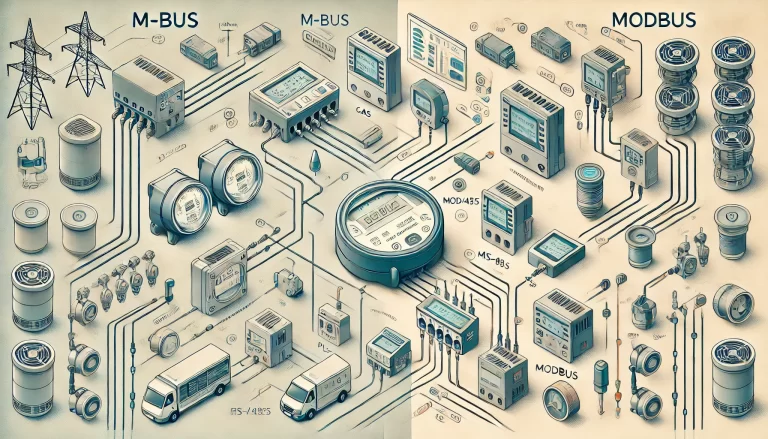
1. M-Bus Communication Protocol
Overview
M-Bus, short for Meter-Bus, is a European standard communication protocol designed for remote reading of metering devices, such as water, gas, and electricity meters. It is optimized for low-power and long-distance communication in metering and energy monitoring applications.
Key Features
- Low Power Consumption: M-Bus is designed to minimize energy usage, making it ideal for battery-powered devices.
- Master-Slave Topology: The protocol employs a master-slave architecture, allowing a single master device to communicate with multiple slave devices.
- Physical Layer: M-Bus uses a two-wire twisted pair as its transmission medium, enabling long-distance communication with minimal interference.
- Transmission Speed: Supports low baud rates, typically ranging from 300 to 9600 baud, sufficient for metering applications.
- Data Format: M-Bus data frames include fields for address, control, data length, and error-checking to ensure reliability.
- Applications: Commonly used in energy management systems, smart buildings, and utility meter readings.
2. Modbus Communication Protocol
Overview
Modbus, developed by Modicon (now part of Schneider Electric) in 1979, is an open industrial communication protocol. It was designed to facilitate simple and effective communication between electronic devices, particularly in automation systems.
Key Features
- Simplicity: Modbus is easy to implement, with a straightforward protocol structure and low communication overhead.
- Open Standard: As an open protocol, it allows manufacturers and developers to freely adopt and implement it.
- Master-Slave Architecture: Similar to M-Bus, Modbus uses a master-slave structure to manage communication.
- Physical Layer Support: Operates over RS-232, RS-485, and TCP/IP, offering versatility across different systems.
- Data Organization: Data is structured in registers, including input registers, holding registers, coils, and discrete inputs.
- Transmission Modes:
- RTU (Remote Terminal Unit): Uses binary encoding for higher efficiency.
- ASCII: Employs text encoding, which is easier to read and debug but less efficient.
- Applications: Extensively used in programmable logic controllers (PLCs), Supervisory Control and Data Acquisition (SCADA) systems, and various automation equipment requiring real-time data exchange.
3. Key Differences Between M-Bus and Modbus
Aspect | M-Bus | Modbus |
---|---|---|
Purpose | Designed for metering and energy monitoring | General-purpose industrial automation |
Transmission Speed | 300–9600 baud | 110–115200 baud |
Physical Layers | Uses twisted pair cables | Supports RS-232, RS-485, and TCP/IP |
Power Consumption | Optimized for low power | Not specifically designed for low power |
Data Organization | Data frame with address and control fields | Registers and coils for storing data |
Applications | Energy meters, smart buildings | PLCs, SCADA, and industrial devices |
4. Common Terminologies in Communication Protocols
To better understand these protocols, here is a glossary of key technical terms:
4.1 Master-Slave Architecture
A communication structure where a master device (e.g., a computer or PLC) initiates communication with multiple slave devices (e.g., sensors or meters). The slave devices only respond to the master’s requests.
4.2 Frame Structure
The basic unit of data transmission, including the following components:
- Header: Identifies the frame and its source.
- Data Field: Contains the actual information being transmitted.
- Checksum: Ensures the integrity of transmitted data.
4.3 Baud Rate
The number of symbols transmitted per second, measured in bits per second (bps). Higher baud rates indicate faster data transmission.
4.4 Registers
Data storage units used in communication protocols:
- Holding Register: Read/write registers storing device state or parameters.
- Input Register: Read-only registers containing measurement data.
- Coil: Binary registers representing device on/off states.
4.5 Transmission Modes in Modbus
- RTU Mode: Uses binary encoding, resulting in higher data density and communication efficiency.
- ASCII Mode: Uses text-based encoding, simplifying debugging at the cost of reduced efficiency.
4.6 CRC (Cyclic Redundancy Check)
A method for error detection during data transmission. It ensures data integrity, particularly in Modbus RTU mode.
5. Use Cases and Applications
M-Bus
- Remote reading of energy consumption (e.g., water, gas, and electricity meters).
- Smart building systems for centralized energy monitoring.
- Public utility systems requiring low-speed, low-power communication.
Modbus
- Industrial automation systems requiring real-time data exchange.
- PLC-based control systems in manufacturing and processing plants.
- SCADA systems for monitoring and control of infrastructure.
Conclusion
Both M-Bus and Modbus are valuable protocols, each suited to specific use cases. M-Bus excels in energy monitoring with its low-power, low-speed design, while Modbus remains a versatile choice for industrial automation with its high-speed, open standard approach. Understanding their features and differences helps users select the appropriate protocol for their applications.