Vortex flow meters are widely used for measuring the flow rate of gases, liquids, and steam in various industries due to their versatility, durability, and accuracy. These meters operate by measuring the frequency of vortices shed by an obstruction (bluff body) placed in the flow stream, which is directly proportional to the flow rate. However, to achieve accurate readings, it’s essential to properly install vortex flow meters with specific lengths of straight pipe sections both upstream and downstream, as these sections help ensure a stable and uniform flow profile.
Below are the essential considerations for installing vortex flow meters, including recommended straight pipe lengths and guidance on managing common flow disturbances.
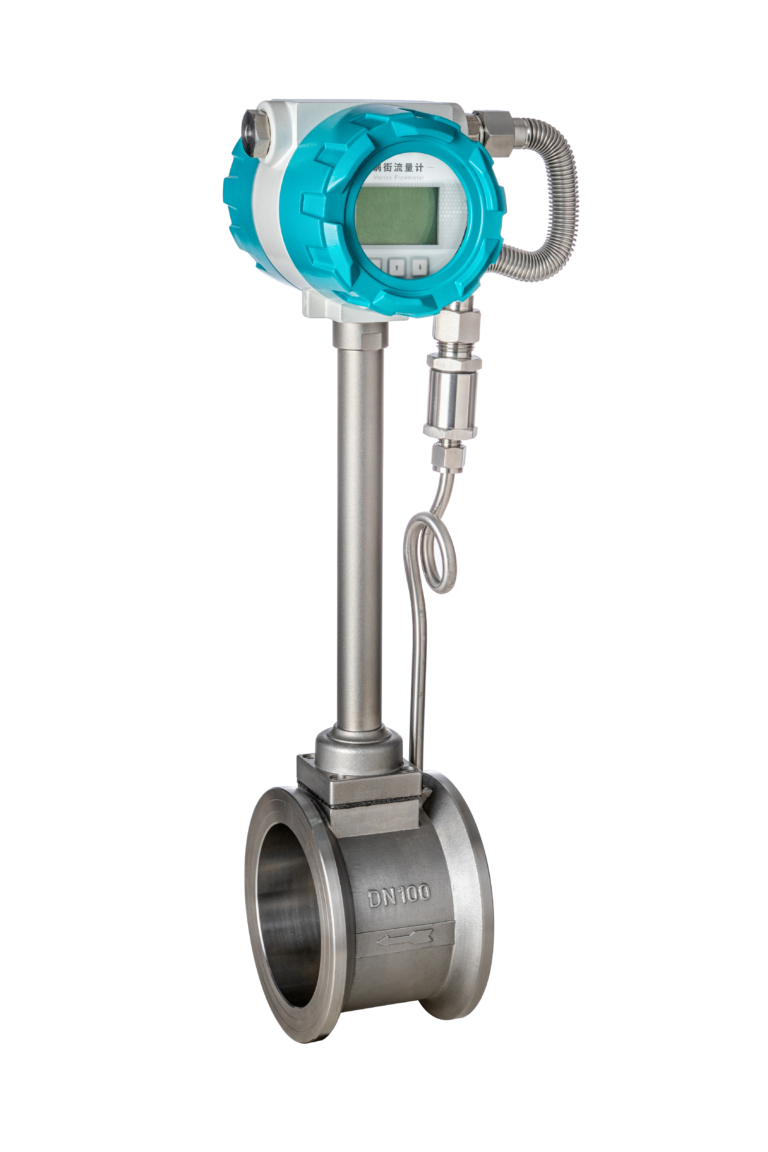
1. Why Straight Pipe Sections Are Important for Vortex Flow Meters
Vortex flow meters rely on a stable flow profile to accurately detect vortex shedding frequencies. Any turbulence, swirling, or asymmetrical flow caused by upstream disturbances (such as elbows, valves, or reducers) can interfere with the vortex shedding process, leading to inaccuracies in flow measurement. By including sufficient straight pipe sections before and after the meter, the flow has time to stabilize, ensuring that the flow profile is as predictable and symmetric as possible when it reaches the meter.
2. Upstream Straight Pipe Requirements
The upstream (inlet) straight pipe section is crucial for stabilizing the flow before it reaches the vortex meter. The length required varies depending on the presence of any upstream disturbances:
- Basic Requirement: A minimum of 15 times the pipe diameter (15D) is generally recommended as the upstream straight pipe length in a standard installation without significant disturbances.
- Higher Disturbances: When there are significant upstream disturbances (such as multiple elbows or valves), it’s recommended to extend the upstream length to 20D or more, allowing for the flow to fully stabilize before reaching the meter.
Following these recommendations helps ensure the accuracy of vortex flow measurements by minimizing disruptions to vortex formation.
3. Downstream Straight Pipe Requirements
The downstream (outlet) straight pipe section, while generally shorter, still plays a role in ensuring measurement stability. This section allows the flow to stabilize after passing through the vortex meter, preventing backflow or turbulence from interfering with readings:
- Basic Requirement: A minimum of 5 times the pipe diameter (5D) is usually sufficient for the downstream straight pipe length.
- Higher Accuracy Requirement: In cases where additional downstream disturbances are present, extending this section to 10D can help ensure stable measurement conditions.
4. Installation Reference Table
For quick reference, the following table summarizes recommended straight pipe lengths based on common upstream disturbances for vortex flow meters:
Upstream Disturbance Type | Recommended Upstream Straight Pipe Length | Recommended Downstream Straight Pipe Length |
---|---|---|
No Disturbance | 15D | 5D |
Single 90° Elbow | 20D | 5D |
Two 90° Elbows (Same Plane) | 20D | 5D |
Two 90° Elbows (Different Planes) | 25D | 5D |
Reducer or Expander | 20D | 5D |
Valve (Control or Throttle) | 25D | 5D to 10D |
Pumps or Compressors (High Turbulence) | 25D to 30D | 10D |
Flow Conditioner Installed | 10D | 5D |
Notes:
- D represents the inner diameter of the pipe.
- Upstream Length Variability: The upstream length can vary based on the severity of the upstream disturbance.
- Downstream Length: Usually shorter but may need to be extended to 10D in high-accuracy applications or with downstream disturbances.
5. Additional Considerations: Flow Disturbances and Flow Conditioners
Certain flow disturbances can create significant turbulence or asymmetrical flow patterns, potentially impacting the vortex flow meter’s accuracy. Below are some additional considerations:
- Elbows and Bends: Elbows near the flow meter, especially in different planes, can cause swirling or asymmetrical flow. If these are unavoidable, installing flow conditioners or increasing the straight pipe lengths can help reduce the impact.
- Control Valves: Control valves cause fluctuations in flow rate, often resulting in turbulence. Positioning valves further upstream (or downstream) can help, or, if close to the meter, additional straight pipe lengths may be necessary.
- Flow Conditioners: Installing flow conditioners or straightening vanes is beneficial in cases where limited space is available for long straight sections. These devices help create a more uniform flow profile before the fluid reaches the vortex meter, minimizing potential inaccuracies.
6. Importance of Following Manufacturer and Industry Standards
Different manufacturers of vortex flow meters may have specific recommendations for straight pipe lengths and installation practices. Adhering to these guidelines, as well as relevant industry standards (such as those from ISO or ASME), ensures optimal performance and measurement accuracy.
7. Conclusion
Proper installation of vortex flow meters is essential to achieve accurate flow measurements. By adhering to the general guidelines—15D to 25D upstream and 5D to 10D downstream, depending on the level of flow disturbance—users can create stable flow conditions that minimize measurement errors. In cases where space is limited or disturbances are high, flow conditioners can further aid in achieving a uniform flow profile. Following these best practices helps maintain the reliability and accuracy of vortex flow meters in various industrial applications.