Industrial automation and safety systems play a critical role in managing and controlling complex processes in industries such as oil and gas, chemical manufacturing, power generation, and more. Among these systems, Safety Instrumented System (SIS), Emergency Shutdown System (ESD), Distributed Control System (DCS), and Programmable Logic Controller (PLC) serve distinct yet sometimes overlapping roles. Understanding the differences between these systems is crucial for optimizing both safety and efficiency in industrial environments.
1. Safety Instrumented System (SIS)
SIS, or Safety Instrumented System, is designed to automatically prevent hazardous events by monitoring critical parameters of a process and taking action to maintain safety. It is essential for industries where even a minor deviation can lead to catastrophic consequences, such as in chemical plants, oil refineries, and gas processing facilities.
Functionality: SIS monitors predefined critical process conditions (e.g., temperature, pressure, flow) and, upon detecting an abnormal state, initiates actions such as shutting down equipment, isolating certain processes, or activating emergency response systems. Its goal is to prevent dangerous conditions from escalating into accidents.
Applications: Commonly used in high-risk industries such as oil and gas, petrochemical, pharmaceutical, and nuclear power, SIS ensures that if unsafe conditions arise, they are promptly mitigated. For example, if a reactor’s temperature exceeds safe limits, the SIS will trigger a controlled shutdown to prevent overheating or explosion.
Key Characteristics:
- High Reliability: SIS is designed with redundant systems (e.g., multiple sensors, actuators) to ensure failure is highly unlikely.
- Compliance with Safety Standards: SIS must adhere to stringent international safety standards such as IEC 61508 and IEC 61511, which govern functional safety requirements for the design, implementation, and maintenance of safety systems.
- Safety Integrity Level (SIL): Each SIS is assigned a SIL level based on the potential risk it mitigates, ranging from SIL 1 (lowest) to SIL 4 (highest). Higher SIL levels indicate higher safety requirements and lower tolerances for failure.
2. Emergency Shutdown System (ESD)
ESD, or Emergency Shutdown System, is a subset of SIS but focuses specifically on ensuring the safety of the plant or equipment in emergency situations. While SIS continuously monitors and controls safety parameters, the ESD system is primarily tasked with rapid, automatic shutdown of processes during dangerous conditions.
Functionality: ESD is triggered either manually or automatically to shut down critical systems, isolate hazardous sections of the plant, or cut off fuel and energy supply in the event of emergencies such as equipment failure, gas leaks, or fire. The shutdown procedure is usually pre-programmed to avoid further escalation of the incident.
Applications: ESD is most frequently seen in industries where processes involve volatile chemicals, flammable gases, or high-temperature equipment. For example, in an offshore oil rig, if the system detects a gas leak, the ESD would immediately stop all processes, seal off sections of the platform, and activate emergency alarms.
Key Characteristics:
- Fast Response: ESD systems are engineered for rapid response in critical situations, ensuring that equipment is shut down or isolated within seconds.
- Redundancy: Like SIS, ESD employs redundant systems and pathways to minimize the chance of failure in emergencies.
- Manual and Automatic Triggering: ESD can be activated both manually by operators and automatically by sensors or safety relays.
3. Distributed Control System (DCS)
DCS, or Distributed Control System, is a control architecture that manages large, complex, and often continuous industrial processes by distributing control tasks across multiple independent controllers. DCS provides real-time control and monitoring of processes, ensuring efficient and optimized operation.
Functionality: DCS systems use a hierarchy of controllers to manage different parts of a process, such as temperature control, pressure regulation, and flow control. Each controller manages a specific section of the process and reports back to a central operator interface. The central system can adjust setpoints, view system status, and intervene in real-time if needed.
Applications: DCS is used in industries that require precise and continuous process control, such as oil refining, chemical processing, water treatment, and power generation. For instance, in a power plant, the DCS controls and monitors the boilers, turbines, and generators, ensuring that each component functions optimally.
Key Characteristics:
- Scalability: DCS systems are designed for scalability, meaning they can manage small plants with a few controllers or large operations with hundreds of control nodes.
- Redundancy and Fault Tolerance: Critical components of a DCS are often duplicated to ensure that even if one part fails, the system continues to operate.
- High-Level Integration: DCS integrates various control functions, such as batch processing, continuous control, and discrete control, into a single system for comprehensive oversight.
- Real-Time Data and Control: The system continuously gathers real-time data from various parts of the process, allowing operators to make informed decisions quickly.
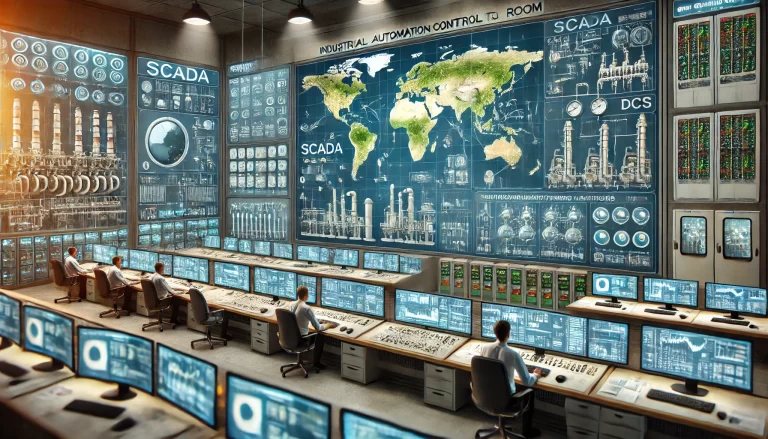
4. Programmable Logic Controller (PLC)
PLC, or Programmable Logic Controller, is a highly versatile and robust industrial control device used to automate machinery and processes. Originally designed to replace relay-based systems, PLCs have since become a staple in industrial automation.
Functionality: PLCs operate by executing a pre-programmed set of instructions (the logic) based on input signals (e.g., from sensors or switches) and then triggering output actions (e.g., turning on a motor, opening a valve). They are typically used for discrete or sequential control tasks, such as starting and stopping machines, routing materials on conveyor belts, or filling bottles in a bottling line.
Applications: PLCs are widely used in industries ranging from automotive manufacturing and material handling to packaging and energy. For example, in an assembly line, a PLC might control the movement of robotic arms and conveyor belts to ensure smooth operation.
Key Characteristics:
- Flexibility: PLCs are easily programmable, meaning they can be adapted to a wide range of applications and process changes with minimal hardware modifications.
- Reliability: PLCs are designed to withstand harsh industrial environments, including temperature extremes, humidity, vibration, and electrical noise.
- Fast Execution: PLCs can process inputs and outputs in real-time, making them ideal for applications where speed is critical.
- Modular Design: Most PLC systems are modular, allowing users to expand functionality by adding input/output modules, communication modules, and other components as needed.
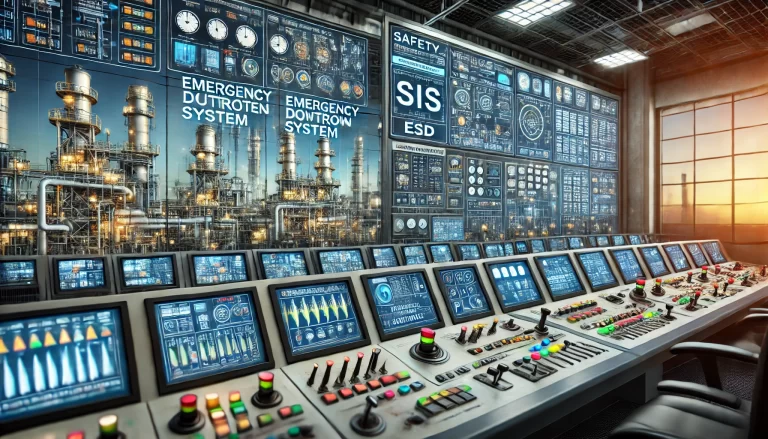
Summary of Key Differences:
Feature | SIS | ESD | DCS | PLC |
---|---|---|---|---|
Primary Role | Ensures safety by monitoring and controlling critical parameters | Performs emergency shutdown during unsafe conditions | Controls and monitors large, complex processes | Controls specific machinery or automation tasks |
Application | High-risk industries (oil, gas, chemicals) | High-risk industries (oil, gas, chemicals) | Large-scale continuous processes (oil refining, power generation) | Discrete or sequential automation (manufacturing, packaging) |
Focus | Safety and accident prevention | Fast emergency response and shutdown | Process optimization and control | Flexibility in discrete control |
Redundancy and Safety | High, often with SIL certification | High, fast response and redundant | Moderate, focuses on continuity of process control | Limited to specific tasks, minimal redundancy |
Programming Complexity | High (due to safety requirements) | Moderate to high (depending on scope) | High (due to process complexity) | Low to moderate, flexible logic programming |
In conclusion, while all four systems play vital roles in industrial automation, their functions are distinct. SIS and ESD focus on safety and emergency actions, whereas DCS and PLC are more concerned with optimizing and automating industrial processes. Each system is chosen based on the specific needs of the industrial process and the safety requirements involved.