Effective liquid level monitoring is critical in ensuring the safety and operational efficiency of storage tanks across industries, including petroleum, chemical, and water storage. To achieve this, storage tanks are equipped with high and low-level alarms to notify operators of any potentially dangerous liquid levels.
This article outlines the key standards and specific requirements for setting up liquid level alarms, covering international standards, alarm types, technical considerations, and regular maintenance.
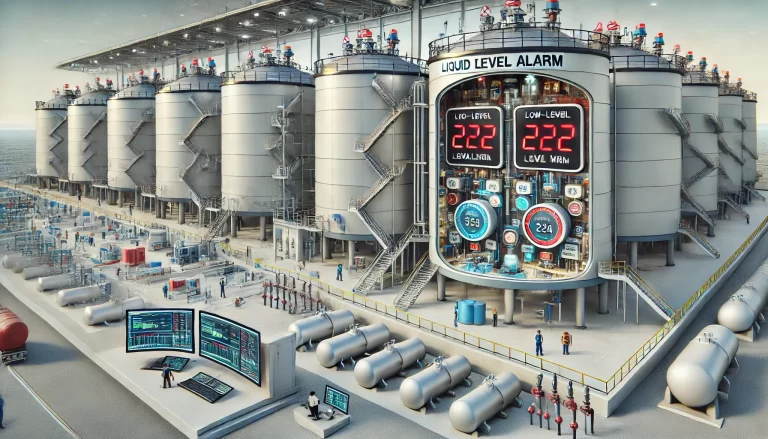
1. International Standards for Tank Level Alarms
Several internationally recognized standards provide guidelines for setting tank level alarms. These standards ensure uniformity and safety across industries.
API 2350 Standard (American Petroleum Institute)
API 2350 is the primary standard used for overfill protection and alarm systems in the petroleum industry. Key requirements include:
- High-Level Alarm: Must be set before the maximum operational level of the tank to allow sufficient time for operators to respond and take corrective action.
- Overfill Alarm: Should be set near the top of the tank, close to the maximum safe working capacity but not exceeding it.
- Low-Level Alarm: Should be installed to prevent equipment damage, such as pump cavitation, when liquid levels drop too low.
IEC 61511 and IEC 61508 (Functional Safety Standards)
These standards focus on the safety of instrumentation systems, including alarms used in liquid level monitoring. They outline the design and implementation of Safety Instrumented Systems (SIS) to ensure that tank alarms are reliable and efficient. The goal is to reduce the likelihood of system failures through proper safety measures.
2. National Standards (China Example)
Different countries also have their specific standards. In China, two key standards apply:
GB/T 50093-2013: Code for Design of Oil Storage Depots
- The high-level alarm should be set 2-5% below the tank’s design safety level to ensure a margin for operator response.
- The low-level alarm should be set sufficiently above the tank bottom to avoid issues like pump cavitation or damage from low fluid levels.
GB 50160-2008: Code for Design of Fire Prevention in Petrochemical Enterprises
- Tanks storing flammable or combustible liquids must have both high- and low-level alarms to prevent overflow and operational hazards. For large tanks (e.g., those with diameters over 15 meters), multi-stage level alarm systems are mandatory to monitor liquid levels more effectively.
3. Specific Alarm Setting Requirements
To ensure optimal safety, the following detailed guidelines apply to the configuration of liquid level alarms:
High-Level Alarms
- Primary High-Level Alarm:
- Set at around 90%-95% of the tank’s maximum operational capacity.
- This provides operators ample warning to slow or stop the inflow of liquid before the tank reaches its critical level.
- Secondary High-Level Alarm:
- Set closer to the maximum safe level, around 95%-98% of the tank’s capacity. This triggers emergency action, such as stopping the inflow automatically to prevent overfilling.
- High-High-Level Alarm (Optional):
- Should be configured near the physical limit of the tank (approximately 98% or higher). This alarm mandates immediate action, such as shutting off pumps and activating emergency pressure relief systems if necessary.
Low-Level Alarms
- Primary Low-Level Alarm:
- Typically set just above the minimum operating level. This prevents potential equipment damage from low liquid levels, such as cavitation in pumps.
- Secondary Low-Level Alarm:
- Set at a more critical threshold, indicating that immediate action is required to either refill the tank or shut down equipment.
4. Technical Considerations for Alarm Systems
Liquid level alarm systems must consider several technical aspects to ensure proper operation:
Alarm Delays and Signal Filtering
Due to the natural fluctuation of liquid levels (e.g., sloshing or wave action), it is common to implement a short delay (2-5 seconds) in the alarm activation to prevent false alarms. This ensures that only sustained level deviations trigger alerts.
Redundancy and Reliability
For critical applications, it is advisable to install redundant level sensing systems. Dual sensors provide a backup in case one sensor fails, ensuring that the alarm system continues to function reliably even in the event of equipment malfunctions.
Types of Alarms
Visual and Audible Alarms: These alarms should be installed both at the tank site and remotely in a control room. Flashing lights or loud sirens can alert personnel at the tank, while remote digital alarms notify operators in the central control room.
Digital Integration: Modern alarm systems can be integrated into Supervisory Control and Data Acquisition (SCADA) systems or Distributed Control Systems (DCS) for real-time monitoring and automatic shutoff responses.
Tank Type and Stored Medium
The type of tank and the characteristics of the stored liquid also influence alarm settings:
- Corrosive or Hazardous Liquids: Sensors in tanks storing corrosive or hazardous materials must have corrosion-resistant components and be rated for explosion-proof conditions, depending on the liquid’s properties.
- Pressurized Tanks: For pressurized tanks, the alarm system may need to incorporate pressure relief mechanisms in addition to level monitoring, ensuring both pressure and level alarms work in tandem.
5. Maintenance and Calibration of Alarms
Regular maintenance is critical to ensure the accuracy and functionality of the alarm system. Industry standards typically recommend:
- Annual Calibration: Sensors and alarms should be tested and calibrated annually, ensuring that they accurately reflect the tank’s liquid level.
- Functional Testing: Before critical operations, the alarm system should undergo functional testing to verify that it responds correctly to both high and low-level conditions.
- Component Replacement: Sensors, alarms, and related components should be inspected regularly, and any worn or malfunctioning parts should be replaced to avoid failures during critical operations.
6. Advanced Monitoring and Automation
Advancements in technology have introduced automated monitoring and alarm systems for storage tanks. These systems use sensors with real-time data transmission capabilities, enabling:
- Automatic Shutoffs: In the event of high-level alarm activation, automated systems can immediately stop pumps or divert flow without manual intervention.
- Predictive Analytics: Integration with big data and machine learning systems allows for predictive maintenance and operational efficiency by analyzing historical alarm data to prevent future issues.
Conclusion
Setting appropriate high and low-level alarms for storage tanks is essential for maintaining safe and efficient operations. The alarms provide operators with critical warnings of potential overflow or underflow conditions, protecting both equipment and personnel. International standards such as API 2350 and IEC 61511, along with national regulations, offer clear guidelines for establishing these alarms. In addition to proper installation, routine maintenance and testing of alarm systems ensure they remain functional and reliable in critical situations.