In industrial process control systems, instrumentation plays a critical role in monitoring and controlling various parameters such as pressure, temperature, flow rate, and level. However, during regular maintenance, calibration, or replacement of instruments, it’s important to ensure that the process continues uninterrupted. This is where bypass design for instrumentation becomes essential. A bypass design allows the process to continue running while the instrument is being worked on. In this article, we’ll delve into the details of what bypass design is, its key components, and why it’s essential in various industrial applications.
What is Bypass Design?
Bypass design refers to the implementation of an alternative pathway for the process fluid to flow around an instrument. This pathway, commonly known as a bypass line, allows the process to keep running even when the primary instrument is offline for maintenance, calibration, or troubleshooting.
The key objective of bypass design is to ensure that instrument servicing does not lead to any downtime in the process. This is particularly crucial in industries where any stoppage in the process can result in significant financial losses or safety risks, such as in chemical processing, oil and gas refining, and power generation plants.
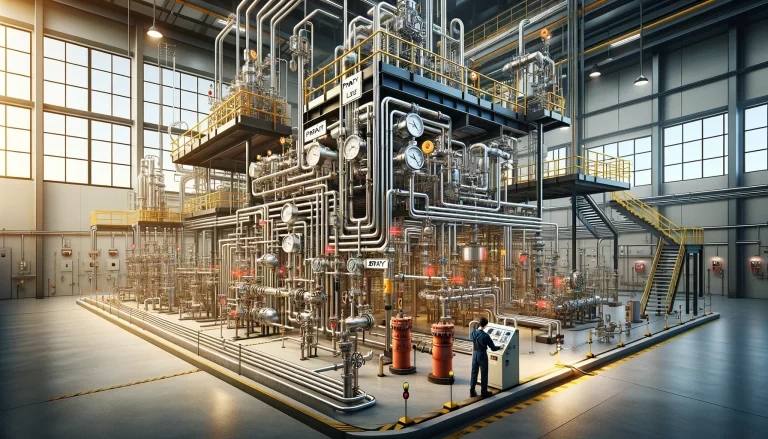
Components of an Instrument Bypass Design
Bypass Line: A bypass line is a secondary pipe or conduit that is installed parallel to the main instrument. The fluid or gas flowing through the process can be diverted through this bypass line when necessary. This allows the instrument to be isolated for service or replacement without shutting down the process. The bypass line is sized appropriately to handle the same flow rates as the main line to ensure smooth operation.
Isolation Valves: Valves are an essential component of a bypass design. Typically, three valves are used: two isolation valves for the instrument itself (upstream and downstream of the instrument) and one valve for the bypass line. The isolation valves can close off the instrument, allowing the process fluid to flow through the bypass line instead. These valves must be high-quality, reliable, and capable of providing a tight seal to prevent leaks.
In some designs, three-way valves are used to facilitate easier switching between the instrument and the bypass line. These valves combine the functionality of two isolation valves and the bypass valve, simplifying the overall setup.
Maintenance and Calibration Ports: A well-designed bypass system often includes ports for calibration and testing. These ports allow operators to conduct instrument calibration without removing it from the system. They can also be used to connect external instruments for diagnostic purposes while the primary instrument is offline.
Pressure Equalization: In some systems, pressure equalization is necessary to ensure that there are no sudden pressure drops or spikes when switching between the main instrument and the bypass line. Pressure balancing valves or regulators may be included to prevent process disturbances during the transition.
Key Benefits of Bypass Design
Continuous Process Operation: The most significant benefit of a bypass design is the ability to maintain continuous operation of the process even when the instrument is being maintained, calibrated, or replaced. This minimizes downtime, which is critical in industries with high operational costs or safety concerns.
Maintenance Flexibility: With a bypass in place, instruments can be serviced at any time without scheduling costly process shutdowns. This flexibility allows for proactive maintenance and quicker response to instrument failures, leading to improved system reliability and reduced costs associated with emergency repairs.
Improved Safety: In processes that involve hazardous materials or high-pressure systems, bypass designs improve safety. They allow operators to isolate an instrument for maintenance while avoiding any exposure to dangerous substances. Additionally, the ability to test and calibrate instruments without removing them from the system further reduces risks associated with handling.
Ease of Instrument Calibration: Regular calibration of instruments is necessary to ensure accuracy in process control. Bypass designs allow calibration to be performed without disrupting the process. This is particularly useful in systems with strict requirements for accuracy, such as pharmaceutical manufacturing or chemical refining.
Application Scenarios for Instrument Bypass Design
Flow Meters: Flow meters are commonly bypassed during calibration or replacement. The bypass design allows operators to maintain flow rates and system pressure while the flow meter is serviced.
Pressure and Temperature Sensors: In many processes, pressure and temperature sensors require periodic calibration. A bypass allows for quick sensor isolation without affecting the overall process, ensuring that data accuracy is maintained while the process continues uninterrupted.
Control Valves: In some applications, control valves are equipped with bypass lines to allow manual operation during valve maintenance. This is especially useful in safety-critical systems where precise control over fluid flow is essential.
Chemical Injection Systems: In chemical processing, the injection of precise amounts of chemicals is often monitored by instruments that can be bypassed for maintenance. The bypass ensures that the chemical injection process continues seamlessly while the instrument is offline.
Considerations for Implementing a Bypass Design
System Complexity: The complexity of the system is a key factor in deciding whether a bypass design is required. For simple systems, a bypass may not be necessary, but for large, complex systems, it is often essential to ensure smooth operation during maintenance activities.
Space Constraints: In some installations, space may be limited, making it difficult to add a bypass line. In such cases, compact valve designs such as three-way valves can be employed to minimize space requirements while still providing bypass functionality.
Cost: The installation of bypass lines and additional valves adds to the initial cost of the system. However, this cost is often justified by the savings in downtime and improved safety and reliability over the long term.
Material Compatibility: The materials used in the bypass design should be compatible with the process fluid to prevent corrosion, erosion, or chemical reactions that could damage the system. This is particularly important in corrosive environments such as those found in chemical processing plants.
Conclusion
Bypass design for instrumentation is a crucial aspect of maintaining the efficiency, reliability, and safety of industrial processes. It allows for the continuous operation of systems while instruments are calibrated, maintained, or replaced, minimizing downtime and enhancing operational flexibility. When properly implemented, a bypass system can provide significant benefits in terms of cost savings, safety improvements, and system reliability.
For industries that rely on uninterrupted operations, such as oil and gas, chemical manufacturing, and power generation, investing in a well-thought-out bypass design is essential to achieving long-term success.