Preventive maintenance, daily maintenance, and overhauls of DCS systems are tasks that every instrumentation technician will encounter in their work. This article organizes some knowledge regarding the preventive maintenance, daily maintenance, and overhauls of DCS systems for everyone’s reference. The goal is to help improve the maintenance skills of instrument technicians in handling DCS systems.
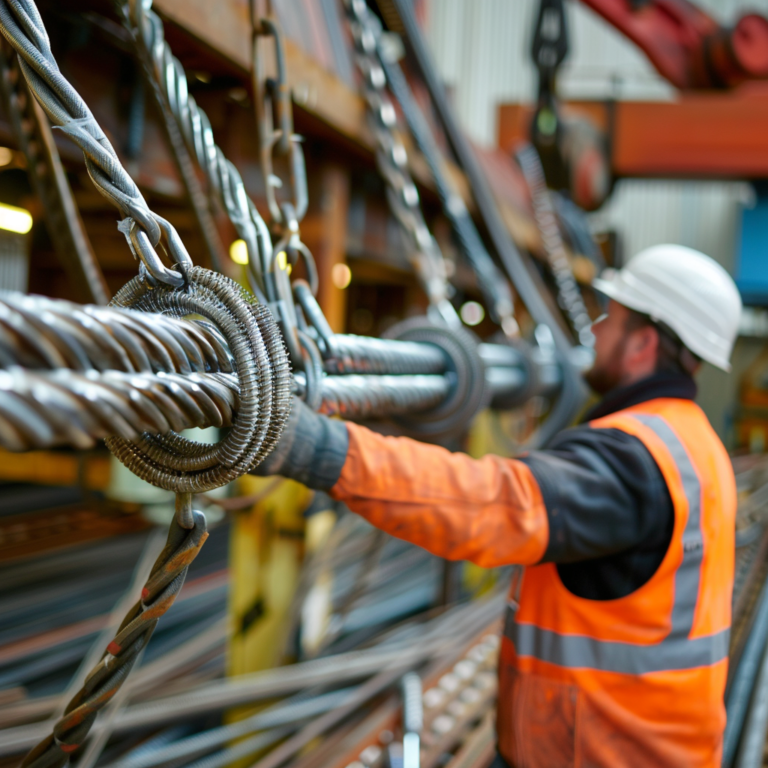
I. Maintenance Basics
Main Tasks in DCS System Maintenance:
- DCS maintenance mainly includes preventive maintenance and fault maintenance.
- Preventive Maintenance: Prevent issues before they occur through strict daily management, regular inspections, and proper upkeep to avoid failures.
- Fault Maintenance: Detect and eliminate faults in a timely and effective manner to ensure normal operations.
- DCS maintenance mainly includes preventive maintenance and fault maintenance.
Maintenance Tools:
- Software Tools: Real-time monitoring software, fault diagnosis software.
- Hardware Tools: Anti-static gloves, dust-removal tools, testing instruments, debugging tools, etc.
Powering Down and Powering Up of the DCS System: This includes the steps, methods, and precautions for shutting down and starting up the system.
Testing of DCS Cards: The testing methods for various types of cards.
Redundancy Testing in DCS:
- Card Redundancy Testing: This includes testing for the main control card, data forwarding card, and I/O card.
- Redundancy Testing of Communication Ports.
- Redundancy Testing of Switches.
- Redundancy Testing of Power Supplies (220VAC, 24VDC).
Battery Replacement for the Main Control Card in the DCS System:
- The battery on the main control card helps preserve controller data when the system is powered down. This battery is typically replaced every 3 to 5 years.
Storage, Backup, and Querying of Historical Data in DCS Workstations
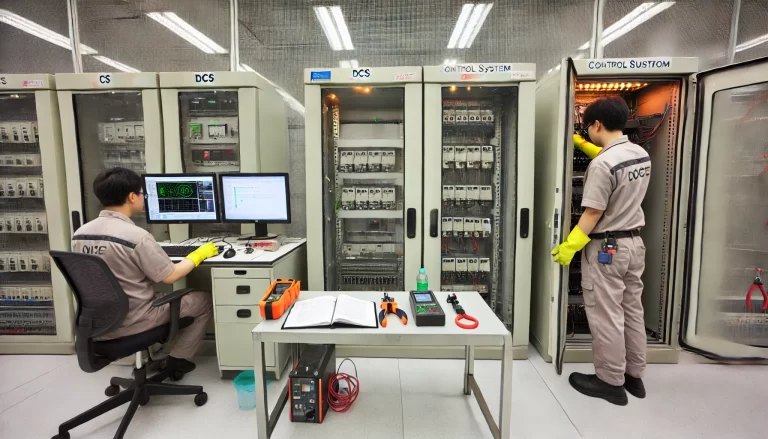
II. Preventive Maintenance
- Daily Management System:
- Inspection System: Define the frequency, route, and inspection content for system maintenance personnel.
- Shift Handover System: Keep records of inspections, any unresolved issues, and pass them on to the next shift.
- Hazard Registration System: Log any software or hardware hazards that cannot be addressed during the shift and report major hazards for handling with supplier assistance.
- Rationalization Proposal System: Propose improvements for issues and deficiencies in the system’s hardware and software.
- Technical Training System: Develop a technical training and learning system to improve system maintenance skills.
- Periodic Work System: Set regulations for tasks like system backups and system cleaning, specifying the content and timing of the work.
- Spare Parts Management System: Clearly define the management of tools and spare parts, including inventory tracking.
- System Inspection and Maintenance System: Set inspection and maintenance standards, including the procedure, content, safety precautions, and the various work permits required.
- Safety Operation System: This includes safety education, risk assessment for safe operations, and hazard evaluation.
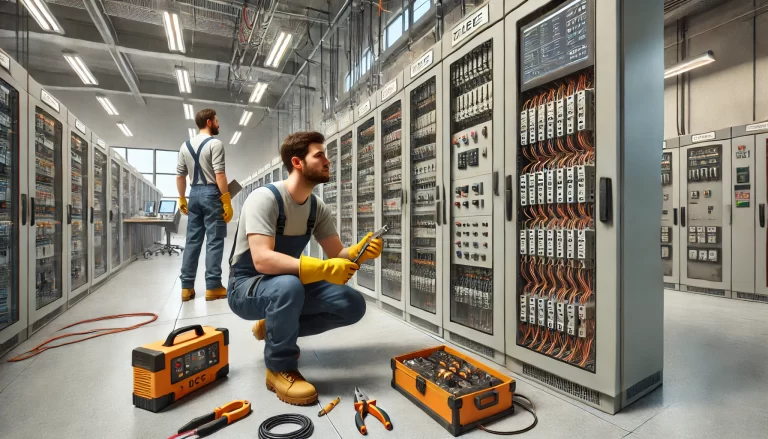
Daily Management of DCS Systems
Central Control Room Management:
- Seal all entry points where dust, moisture, pests, or other harmful insects may enter.
- Ensure stable operation of air conditioning equipment and maintain temperature fluctuations within 5°C, preventing condensation on system equipment.
- Separate the control room from the field environment, and regularly clean the control room to keep it tidy.
- Restrict access to the control room to authorized personnel only.
DCS Control Station Management:
- Do not modify or dismantle system components without authorization.
- Avoid pulling or damaging cage wiring, grounding wires, power lines, or communication cables.
- Keep cabinet doors locked, and assign key management to specific personnel.
DCS Workstation Hardware Management:
- Handle equipment with care, using appropriate force when operating the keyboard and mouse.
- Do not insert or remove workstation equipment while powered on. Keep the workstation clean and regularly clean the industrial computer’s filters.
- Avoid electromagnetic interference with the display and do not move the running industrial computer or monitor. Avoid pulling or damaging equipment connection cables and communication cables.
- Keep the monitor away from heat sources, and do not clean it with alcohol. If cleaning is necessary, turn off the power first and use a damp sponge to wipe the monitor.
DCS Workstation Software Management:
- Do not use unauthorized Windows software.
- Operators must not exit real-time monitoring software.
- Operators must not modify the computer’s system configuration, or arbitrarily add, delete, or move files and directories on the hard drive.
- Maintenance personnel must carefully use external disks to prevent virus intrusion.
- Do not run unnecessary multitasking operations on the real-time monitoring platform.
- Maintenance personnel must back up necessary system drivers.
- Configuration files should be stored in the root directory of drive D under a folder named “DCSData”. No files other than the most recent configuration file should be stored on drive D. Configuration files should also be backed up in a folder named “Configuration Backup” on drive E, and backups should be stored on paper, hard drives, and optical discs simultaneously.
DCS Communication Network Management:
- Avoid pulling or damaging communication cables.
- The communication network is divided into an A network and a B network, corresponding to the respective network cards and switches, and must not be swapped.
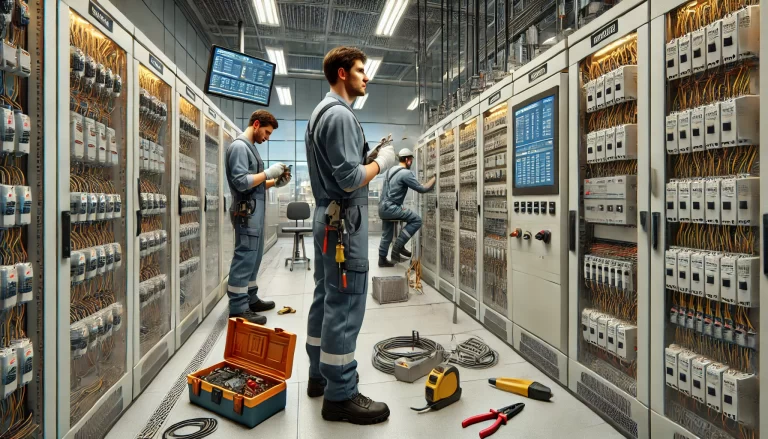
Regular Inspections of the DCS System
Control Station Inspections:
- Clean the control station monthly and the machine cage inside the cabinet regularly.
- Record the temperature and humidity inside the control cabinet daily to monitor for condensation and corrosion.
- Regularly check the operation of the power supply and fans, ensuring that the power output is normal.
- Check the operational indicator lights on all cards daily. If fault indicator lights are flashing, take immediate action to resolve the issue.
- Inspect all cable connections weekly to ensure they are secure and correctly connected.
- Check grounding connections quarterly.
Workstation Inspections:
- Check the workstation’s fan and industrial computer temperature daily to ensure normal operation.
- Review system logs, security logs, and application logs weekly for abnormal records.
- Monitor hard drive space monthly and run defragmentation if necessary.
- Check the IP address settings of the workstation monthly, and ensure flow control on the network card is disabled.
- Ensure no unauthorized software is installed on the workstation monthly.
- Verify that configuration files, data files, and operating parameters are backed up monthly.
- Ensure that fault diagnosis, data refreshing, trend recording, and consistency between the upper and lower system configurations are functioning normally.
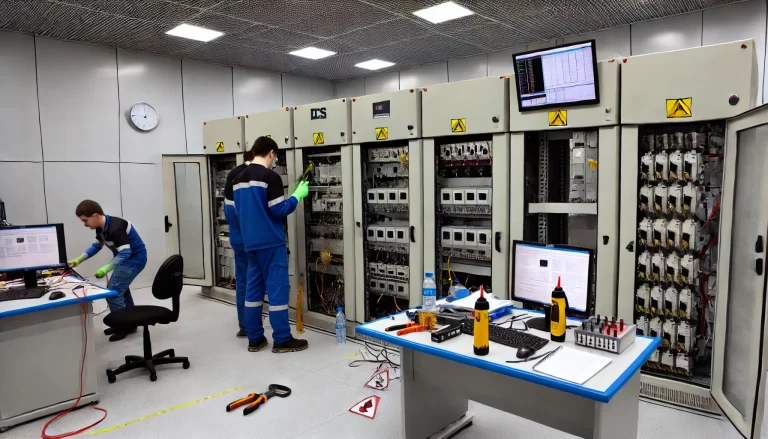
III. Overhaul Maintenance of DCS Systems
During an overhaul, the DCS system should undergo comprehensive maintenance, including:
- Conduct a thorough inspection of the control system and make records.
- Back up system configurations and verify part labels and addresses.
- Perform power-down cleaning of the control station and related components such as dust filters, power supply boxes, and machine cages inside the control cabinet.
- Inspect power supply lines, electrical boxes, terminals, relays, safety barriers, and other components to ensure they are working properly and that connections are secure.
- Inspect the grounding system, perform power performance tests, and conduct insulation tests on wiring.
- Tighten control station cabinet wiring and secure screws.
- Apply dust-proofing and sealing treatments to the control station cabinet, and replace cooling fans.
- Address any unresolved defects from normal operation and restore or improve various labels.
- Test the functionality of hardware devices, load configuration software, and verify system performance.
- Calibrate measurement cards and perform interlock protection tests.
- Inspect, replace, or repair cables, pipelines, and related components.
- Inspect the grounding system, including terminal inspections and ground resistance testing.
- Check communication line connections and ensure that all components are working properly and that connections are secure.
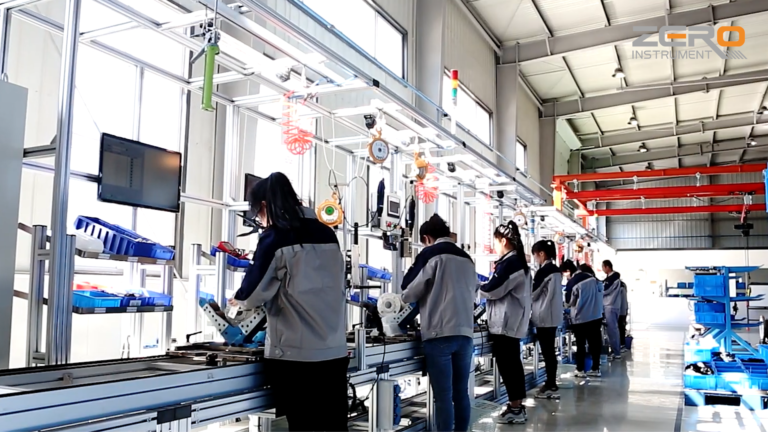
IV. Troubleshooting in DCS Systems
Basic Approach to Troubleshooting:
- Understand the most common and useful fault symptoms, analyze the causes of the fault, and use elimination and substitution methods to resolve the issue.
Troubleshooting Communication Failures:
- Common causes of communication failures include:
- Communication hardware failure (e.g., communication cables, network cards, switches, communication interfaces, communication modules).
- Network settings and configuration errors (e.g., network card drivers, IP addresses, subnet masks, communication protocols, baud rates, dial switches).
- Common causes of communication failures include:
Handling Abnormal Card Operation:
- Possible causes of abnormal card operation include:
- Incompatible or damaged chip versions.
- Low lithium battery voltage (below 3.3V) on the main control card.
- Damaged communication ports.
- Incorrect address settings or faulty dial switches.
- Improper power supply to the card.
- Incorrect signal wiring or jumper settings on the card.
- Various types of noise or interference.
- Poor grounding or a faulty motherboard.
- Faults in field instruments.
- Possible causes of abnormal card operation include:
Handling Workstation Failures:
- Common workstation hardware failures include:
- Monitor Failures:
- Separate monitor failures from video card failures. If replacing the monitor does not resolve the issue, consider possible faults with the video card or other components.
- If the monitor flickers or shows partial color, it may be due to improper refresh rate settings or interference from high-power electrical equipment.
- Host Failures:
- Host failures include problems with power supplies, hard drives, motherboards, memory, video cards, and sound cards. These are generally resolved by replacing parts provided by suppliers. Eliminate hardware faults using substitution methods, and ensure the host is powered off when replacing hardware.
- Operator Keyboard Failures:
- Common operator keyboard issues include unresponsive keys or the entire keyboard failing to output. Causes may include individual key damage, excessive static buildup at the interface, improper grounding of the operator console, faulty motherboard ports, or errors in custom key settings in the configuration. Due to static buildup, the keyboard may show a red light, but this won’t affect operations. Carefully unplug the keyboard, wait for about 3 minutes, then carefully reinsert it to resume normal operation.
- Monitor Failures:
- Common workstation hardware failures include:
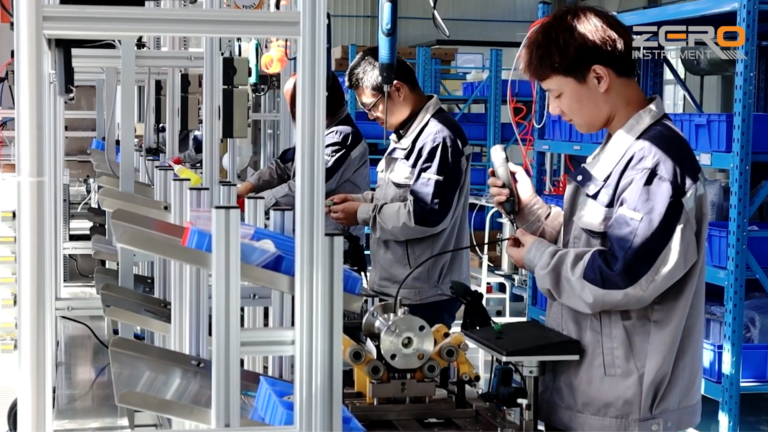
Conclusion
Maintaining a DCS (Distributed Control System) is a critical aspect of ensuring smooth, efficient, and uninterrupted operations in various industrial settings. By adhering to the outlined preventive maintenance, daily management routines, and comprehensive overhaul strategies, technicians can significantly reduce the risk of system failures and optimize the longevity and reliability of the DCS.
The key to successful DCS maintenance lies in regular inspections, proper use of tools, and diligent attention to both hardware and software. Troubleshooting methods are equally important, as they help swiftly identify and resolve issues before they impact overall system performance. Through continuous learning, adherence to safety protocols, and effective management, maintenance personnel can enhance their skills and contribute to the safe and effective functioning of DCS systems.
By following these best practices, organizations can ensure the long-term stability of their systems, minimize downtime, and achieve more efficient production outcomes.