Salt storage tanks are important facilities for storing industrial salt or edible salt. Accurate measurement of the material inside them is crucial to ensure the continuity of the production process and the stability of product quality. Traditional level measurement methods are often limited by physical conditions and cannot provide high-precision measurement data. The application of radar level meters, with its non-contact, high-precision and strong adaptability, provides an effective solution for level measurement of salt storage tanks.
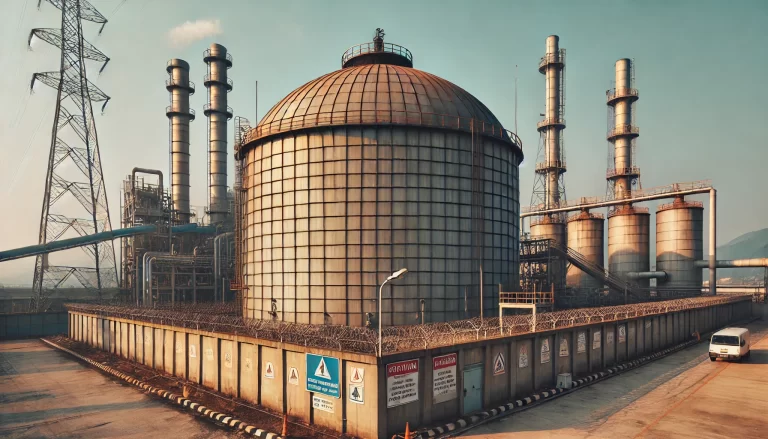
Salt storage tanks are usually vertical cylindrical structures. The salt particles stored inside may present different physical states due to factors such as humidity and temperature, such as dry and loose or wet and agglomerated. These characteristics pose the following challenges to level measurement technology:
1. Changes in the dielectric constant of salt particles will affect the intensity of the reflected signal, thereby affecting the accuracy of the measurement results.
2. The agglomeration phenomenon may cause misreading or damage to traditional measuring equipment (such as float type and heavy hammer type).
3. In a high humidity environment, salt particles are prone to moisture absorption and adhesion, affecting measurement accuracy.
In view of the characteristics of salt storage tanks, radar level meters have shown significant advantages:
1. Non-contact measurement avoids the problems of physical wear and material adhesion.
2. High-frequency radar waves can penetrate steam and dust, reducing the impact of environmental factors.
3. The adjustable signal reflection recognition function can adapt to changes in different dielectric constants and improve measurement accuracy.
In a edible salt processing plant, in order to ensure a stable supply of salt on the production line, the factory decided to use a radar level meter to monitor the salt storage tank in real time.
The salt storage tank is 8 meters in diameter and 12 meters in height, storing fine-grained salt that has been dried. Considering that salt particles may agglomerate due to moisture absorption, a radar level meter with a high-frequency radar wave transmitter was selected. Its operating frequency is 26GHz, which can provide a more concentrated beam and stronger anti-interference ability.
During the installation process, the technicians installed the radar level meter at the center of the top of the salt storage tank to ensure that the radar wave can vertically cover the entire material surface.
By adjusting the sensitivity of the equipment and the signal processing algorithm, the level meter can accurately identify the reflected signal on the surface of the salt particles, and maintain stable measurement results even when there is a slight agglomeration phenomenon on the surface of the salt particles.
In actual application, the radar level meter successfully achieved continuous monitoring of the salt particle level in the salt storage tank.
The data shows that the measurement error is controlled within ±1cm, which far exceeds the factory’s requirements for measurement accuracy. In addition, due to the non-contact measurement characteristics of the radar level meter, maintenance costs and downtime are greatly reduced, and production efficiency is improved.
The application of radar level meter in salt storage tank level measurement not only solves the various challenges faced by traditional measurement methods, but also improves the accuracy and reliability of measurement.
Through reasonable equipment selection and parameter adjustment, efficient monitoring of materials in salt storage tanks can be achieved, providing strong technical support for the automation and intelligence of salt production.