Pressure transmitters are simple in structure, durable, highly stable, with high precision and good linear characteristics.
They have a wide measuring range and are widely used in various industrial automatic control environments, involving water conservancy and hydropower, railway transportation, intelligent buildings, production automatic control, aerospace, military industry, petrochemical, oil wells, electric power, ships, machine tools, pipelines and other industries.
This article briefly summarizes the problems encountered in the use of pressure transmitters.
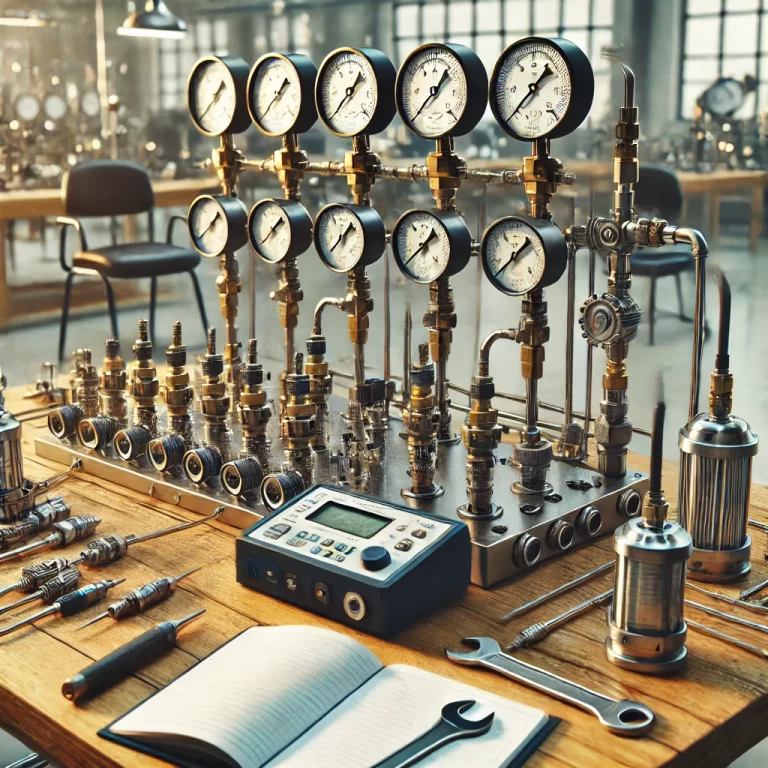
1. Problem phenomenon: Transmitter has no output
Inspection and testing
1. Check if the transmitter power supply is connected in reverse;
2. Measure the power supply of the transmitter to see if there is a 24V DC voltage;
3. If it is equipped with a meter head, check if the meter head is damaged (you can short-circuit the two wires of the meter head first. If it is normal after the short circuit, it means that the meter head is damaged);
4. Connect the ammeter in series to the 24V power supply circuit to check if the current is normal;
5. Check if the power supply is connected to the power input terminal of the transmitter;
Solution
1. Connect the power polarity correctly.
2. Ensure that the power supply voltage of the transmitter is ≥12V (i.e. the voltage of the transmitter power input terminal is ≥12V).
3. If there is no power supply, check whether the circuit is broken and whether the detection instrument is selected incorrectly (the input impedance should be ≤250Ω);
4. If the meter head is damaged, replace it. If it is normal, it means that the transmitter is normal. At this time, check whether other instruments in the circuit are normal.
5. Connect the power cord to the power terminal.
2. Problem phenomenon: Transmitter output ≥ 20mA
Inspection and testing
1. Is the transmitter power supply normal?
2. Does the actual pressure exceed the selected range of the pressure transmitter?
3. Is the pressure sensor damaged? Severe overload may sometimes damage the isolation diaphragm.
4. Is the wiring loose?
5. Is the power cord wiring correct?
Solution
1. If the transmitter power supply is less than 12VDC, check whether there is a large load in the circuit. The input impedance of the transmitter load should meet RL≤(transmitter power supply voltage-12V)/(0.02A) Ω
2. Reselect a pressure transmitter with an appropriate range.
3. If the pressure sensor is damaged, it needs to be sent back to the manufacturer for repair.
4. Connect the wires and tighten them.
5. The power cord should be connected to the corresponding terminal.
3. Problem phenomenon: Transmitter output ≤4mA
Inspection and testing
1. Is the transmitter power supply normal?
2. Does the actual pressure exceed the selected range of the pressure transmitter?
3. Is the pressure sensor damaged? Severe overload can sometimes damage the isolation diaphragm.
Solution
1. If the transmitter power supply is less than 12VDC, check whether there is a large load in the circuit. The input impedance of the transmitter load should meet RL≤(transmitter power supply voltage-12V)/(0.02A) Ω.
2. Reselect a pressure transmitter with an appropriate range.
3. If the pressure sensor is damaged, it needs to be sent back to the manufacturer for repair.
4. Problem phenomenon: Incorrect pressure indication
Inspection and testing
1. Is the transmitter power supply normal?
2. Is the reference pressure value correct?
3. Is the range of the pressure indicator consistent with the range of the pressure transmitter?
4. Are the input of the pressure indicator and the corresponding wiring correct?
5. The input impedance of the transmitter load should meet RL≤(transmitter power supply voltage-12V)/(0.02A) Ω
6. Is the input end of the multi-point paper recorder open when there is no recording?
7. Is the corresponding equipment housing grounded?
8. Is it separated from the AC power supply and other power supplies?
9. Is the pressure sensor damaged? Severe overload sometimes damages the isolation diaphragm.
10. Is there sand, impurities, etc. blocking the pipeline? If there are impurities, the measurement accuracy will be affected;
11. Is the temperature of the pipeline too high? The operating temperature of the pressure sensor is -25~85℃, but it is best to use it within -20~70℃ in actual use.
Solution
1. If the transmitter power supply is less than 12VDC, check whether there is a large load in the loop. The input impedance of the transmitter load should meet RL≤(transmitter power supply voltage-12V)/(0.02A) Ω.
2. If the reference pressure gauge has low accuracy, replace it with a pressure gauge with higher accuracy.
3. The range of the pressure indicator must be consistent with the range of the pressure transmitter.
4. If the input of the pressure indicator is 4~20mA, the transmitter output signal can be directly connected; if the input of the pressure indicator is 1~5V, a resistor with an accuracy of one thousandth or more and a resistance of 250Ω must be connected to the input end of the pressure indicator, and then connected to the input of the transmitter.
5. The input impedance of the transmitter load should meet RL≤. If it does not meet the requirements, corresponding measures can be taken according to the differences: such as increasing the power supply voltage (but must be lower than 36VDC), reducing the load, etc.
6. If the input end of the multi-point paper recorder is open when it is not recording, then: 1. Do not carry other loads; 2. Use other recorders with input impedance ≤250Ω when not recording.
7. Ground the corresponding equipment housing.
8. Separate the wiring from the AC power supply and other power supplies.
9. If the pressure sensor is damaged, it needs to be sent back to the manufacturer for repair.
10. If there are sand, impurities, etc. blocking the pipeline, the impurities need to be cleaned and a filter should be added before the pressure interface.
11. If the temperature of the pipeline is too high, add a buffer tube to dissipate heat. It is best to add some cold water to the buffer tube before use to prevent superheated steam from directly impacting the sensor, thereby damaging the sensor or reducing its service life.