Automation instruments can be categorized into six major types: field measurement instruments, field control instruments, field instrument actuators, display and recording instruments, regulation control instruments, and special measurement instruments. Each major type can be further subdivided into several categories. This article provides a detailed discussion of these types.
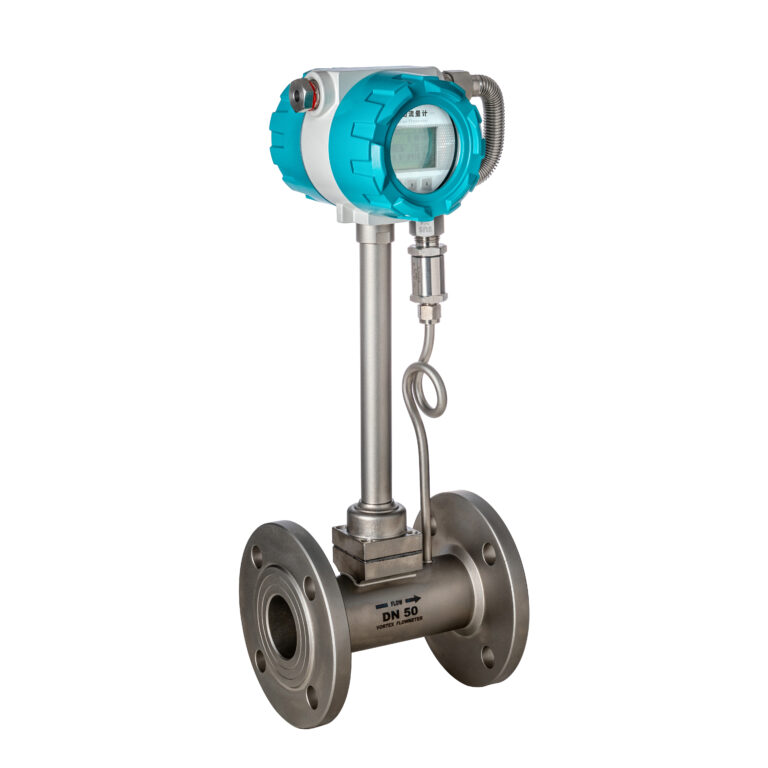
Definition of Automation Instruments
Automation instruments are tools with advanced functions constructed from various automation components. These instruments generally possess multiple functions such as measurement, display, recording, control, and alarm.
Origin of Automation Instruments
Automation instruments truly emerged in the 1980s, when control devices effectively combined automation technology with industrial instruments, leading to comprehensive control via assembled electronic equipment. As control technology continued to develop, automation technology became the main tool for the advancement of industrial instruments, leading to the advent of true automation instruments.
The rapid advancements in microelectronics, computer technology, network communication, and information processing have significantly influenced the innovation of automation instruments. These technologies have become new driving forces for the development of industrial automation instruments, enabling them to acquire comprehensive information faster, more sensitively, reliably, and simply. Today, automation instruments have surpassed traditional optical, mechanical, and electrical frameworks, moving towards intelligent, networked, bus-oriented, and open directions. This guide helps you understand the “family tree” of automation instruments.
Classification of Automation Instruments
Automation instruments can be divided into six major types:
- Field Measurement Instruments
- Field Control Instruments
- Field Instrument Actuators
- Display and Recording Instruments
- Regulation Control Instruments
- Special Measurement Instruments
1. Field Measurement Instruments
These instruments are installed at industrial production sites and can be subdivided into level instruments, pressure instruments, temperature instruments, flow instruments, gas analysis instruments, and liquid analysis instruments.
Level Instruments: Measure liquid level, solid and powder height, and liquid phase interface positions. They include continuous level instruments (e.g., direct reading liquid level gauges, capacitive level gauges, float level gauges) and limit level instruments (e.g., capacitive level switches, float level switches).
Pressure Instruments: Measure pressure or differential pressure in industrial processes. They include liquid column pressure gauges, pressure transmitters, differential pressure transmitters, pressure sensors, pressure gauges, and pressure switches.
Temperature Instruments: Measure the heat level of objects. They include liquid-in-glass thermometers, pressure thermometers, thermocouples, resistance thermometers, temperature transmitters, bimetallic thermometers, temperature switches, optical pyrometers, radiation thermometers, and non-contact infrared thermometers.
Flow Instruments: Also known as flowmeters, they measure the flow rate of gases or liquids. They include mass flow meters, volumetric flow meters, velocity flow meters, and differential pressure flow meters.
Gas Analysis Instruments: Measure the composition of gases. They include gas chromatography/mass spectrometers, oxygen analyzers, toxic/combustible gas detectors, thermal conductivity analyzers, magnetic analyzers, electrochemical analyzers, infrared analyzers, ultraviolet analyzers, laser gas analyzers, and photoelectric gas analyzers.
Liquid Analysis Instruments: Measure various properties of liquids. They include electrochemical analyzers, UV-Vis analyzers, infrared spectrophotometers, distillation analyzers, liquid chromatography/mass spectrometers, water quality analyzers (e.g., pH meters, conductivity meters, concentration/turbidity meters), and viscosity/density meters.
2. Field Control Instruments
Field control instruments are installed at production sites to measure various process parameters, execute control commands, or convert signals for communication. They include pneumatic control instruments, hydraulic control instruments, and electric control instruments.
3. Field Instrument Actuators
These actuators include pneumatic diaphragm control valves, pneumatic diaphragm control valves with valve positioners, electric valve positioners, and smart electric valve positioners.
4. Display and Recording Instruments
Display and recording instruments can be divided into paper chart recorders, paperless recorders, display instruments (analog display instruments, digital display instruments, touch screen HMIs, CRT display terminals), and flash alarm instruments.
5. Regulation Control Instruments
These include PID controllers, PLCs, digital control systems (e.g., alarm continuous control systems, DCS systems, FCS bus control systems, ESD emergency shutdown systems, SIS safety instrumented systems), and IPC industrial PCs.
6. Special Measurement Instruments
Special measurement instruments include shaft vibration meters, shaft displacement meters, tachometers, weighing instruments, thickness gauges, signal calibrators, and flame detectors.
Visual Representation
I will now create a detailed chart to visually represent the classification of automation instruments.
Understanding the Types of Automation Instruments
Automation instruments can be categorized into six major types: field measurement instruments, field control instruments, field instrument actuators, display and recording instruments, regulation control instruments, and special measurement instruments. Each major type can be further subdivided into several categories. This article provides a detailed discussion of these types.
Definition of Automation Instruments
Automation instruments are tools with advanced functions constructed from various automation components. These instruments generally possess multiple functions such as measurement, display, recording, control, and alarm.
Origin of Automation Instruments
Automation instruments truly emerged in the 1980s, when control devices effectively combined automation technology with industrial instruments, leading to comprehensive control via assembled electronic equipment. As control technology continued to develop, automation technology became the main tool for the advancement of industrial instruments, leading to the advent of true automation instruments.
The rapid advancements in microelectronics, computer technology, network communication, and information processing have significantly influenced the innovation of automation instruments. These technologies have become new driving forces for the development of industrial automation instruments, enabling them to acquire comprehensive information faster, more sensitively, reliably, and simply. Today, automation instruments have surpassed traditional optical, mechanical, and electrical frameworks, moving towards intelligent, networked, bus-oriented, and open directions. This guide helps you understand the “family tree” of automation instruments.