A radar level meter is a liquid level measurement device that is widely used in various industrial scenarios, including the level measurement of compressor inlet manifold tanks. In this paper, we will introduce the characteristics of compressor inlet separator tanks and provide two actual measurement cases to demonstrate the application of radar level meters in this area.
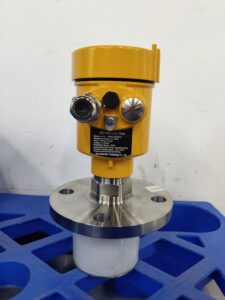
Compressor inlet separator tanks are used in compressor systems to separate liquid and gas mixtures and are characterized by the following features:
High-pressure environments:
Compressor inlet separator tanks are in high-pressure operating environments because they need to handle gas and liquid mixtures at the compressor inlet.
This means that the level-measuring device needs to be sufficiently pressure-resistant.
Liquid-gas separation: The main function of the separator tank is to separate the liquid from the gas, ensuring that only the gas enters the compressor.
Therefore, the level measuring device needs to be able to accurately measure the level of the liquid portion in order to correctly determine the height of the liquid.
Multi-phase liquids: The liquids in the compressor inlet separator tank are usually multi-phase liquids, including a mixture of liquids and gases.
Level measurement equipment is particularly important for the accurate measurement of such multi-phase liquids. Fast response: Fast response to level changes is one of the key requirements of a compressor system.
Level measurement equipment needs to have the ability to respond in a timely manner and provide accurate data in order to make timely adjustments and control system operation.
Below are two actual measurement cases demonstrating the use of radar level meters for level measurement in compressor inlet manifold tanks.
Case 1: Oil and Gas Industry In the oil and gas industry, compressor inlet separator tanks are used to handle crude oil and natural gas mixtures generated at the wellhead. These mixtures contain liquid crude oil, natural gas liquids, and gases.
Conventional-level measurement methods are often ineffective in high-pressure environments and multiphase liquid conditions.
Radar level gauges, however, provide accurate level measurement in high-pressure and multi-phase liquid situations through their non-contact measurement method.
It can quickly respond to changes in liquid level and provide stable level data to help operators make timely adjustments and control the system to ensure the normal operation of the compressor.
Case 2: Chemical plant In chemical plants, compressor inlet separator tanks are widely used to handle liquid and gas mixtures in chemical processes. These mixtures may have different temperatures, pressures, and chemical properties, placing high demands on the level measurement equipment.
Conventional-level measurement equipment is often unable to meet the demand for accurate measurement in such complex environments. The radar level meter is able to cope with the requirements of such complex environments. It can accurately measure the liquid level in the compressor inlet manifold under high pressure and multi-phase liquid conditions.
By transmitting high-frequency electromagnetic waves and receiving their reflected signals, radar level gauges reliably measure the level of liquids regardless of their temperature, pressure, and chemical properties.
The characteristics of compressor inlet separator tanks include high-pressure environments, liquid-gas separation, multi-phase liquids, and fast response, which require level measurement devices with pressure resistance, the ability to measure accurately, and fast response.
Practical measurement examples show the use of radar level meters in the oil and gas industry and in chemical plants for level measurement in compressor inlet separator tanks.
It provides accurate and stable level measurement data in high-pressure environments and multi-phase liquids and helps operators control and adjust the operation of compressor systems.