At present, the level measurement requirements of refinery tank areas are getting higher and higher, not only to be stable and accurate but also to be safe and reliable. Many users are racking their brains and hesitating when it comes to choosing which measuring instrument to use. In fact, a non-contact radar level meter is a very reliable measurement instrument, so in the end, what advantages it has suitable for refinery tank area measurement?
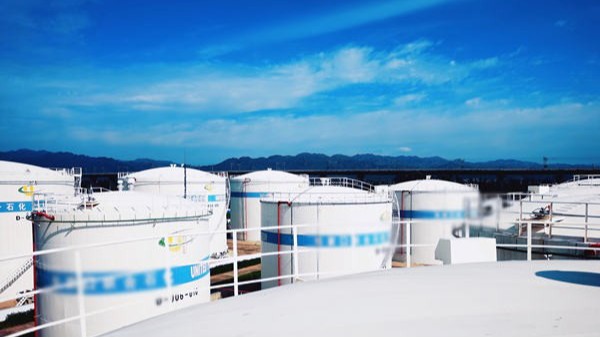
Refinery refers to the crude oil extracted from the ground through the process of distillation, catalysis, cracking, cracking, hydrogenation and refining to produce diesel, gasoline, paraffin, lubricating oil, petroleum coke, asphalt, ethylene, and other products of the plant. Generally speaking, the measurement environment in refinery tanks is relatively harsh, and it just so happens that the advantages of non-contact radar level meters are more suitable for this kind of working condition measurement, for the following reasons.
Firstly, the non-contact radar level meter, with its small antenna size is simple to install and highly reliable. It uses both digital and analog output, is easy to connect with the computer, its emission rate is very low, the surrounding environment and personnel basically no harm, with high operability.
Secondly, the non-contact radar level meter has a high frequency, smaller beam angle, stronger anti-interference capability, and high measurement stability, and the microwave it emits is an electromagnetic wave that can propagate without a medium and can pass through the atmosphere, steam, etc. with very little influence.
Last but not least, the non-contact radar level meter does not need to be in contact with the liquid when measuring, which also avoids the influence of external environmental factors on its internal structure in the harsh working environment of the refinery area, making it have a longer service life than other level measuring instruments and very largely reduces production costs.