1. Introduction
In industrial process control, ensuring operational safety and stability under abnormal or limiting conditions is a crucial challenge. Traditional methods for handling such non-standard operating conditions typically include emergency shutdowns or manual intervention. However, these approaches are often reactive rather than proactive.
Selective control systems represent a more advanced solution by proactively switching control strategies when safety thresholds are approached. This document outlines the basic principles of selective control systems and provides a detailed explanation of integral saturation and methods to prevent it.
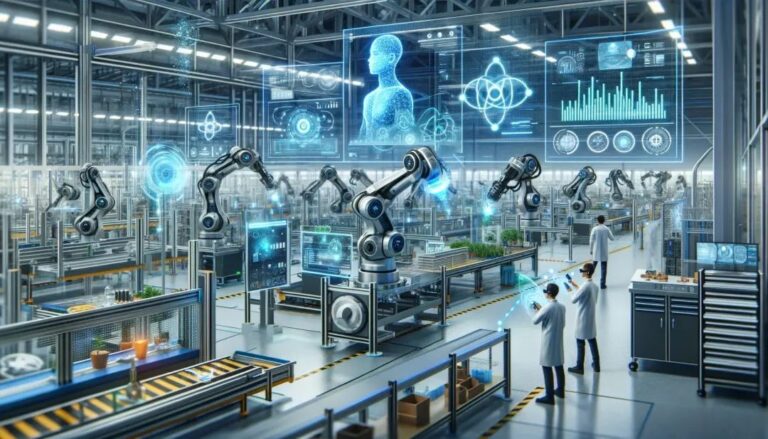
2. Selective Control Systems
2.1 Definition
A selective control system is an advanced control strategy designed to automatically switch between different control modes based on real-time operating conditions. When the process begins approaching unsafe or critical limits, the system overrides the normal control strategy and activates an alternative scheme tailored for safety or process protection. Once the system returns to normal operating conditions, control automatically reverts to the original control scheme.
2.2 Key Characteristics
Dual Control Paths: The system typically includes two or more controllers or measurement transmitters.
Selector Function: A signal selector is used to choose the most appropriate control signal based on predefined logic (e.g., high/low signal selection).
Safety-Oriented Logic: The alternative control logic is designed to ensure safety, equipment protection, or process continuity under abnormal conditions.
2.3 Example Applications
Furnace Temperature Control: When the temperature rises abnormally, the system switches from a performance-oriented controller to a safety-oriented one that limits fuel input.
Compressor Systems: If suction pressure drops too low, the system overrides normal control to prevent surge or cavitation.
3. Integral Saturation and Its Prevention
3.1 What Is Integral Saturation?
In a control system, a controller with integral action accumulates error over time to eliminate steady-state deviations. However, if the controller operates in open-loop mode or the error signal persists too long without correction, the integral output can grow excessively, eventually hitting the controller’s output limits. This phenomenon is known as integral saturation, during which the controller temporarily loses its ability to regulate the process.
3.2 Causes of Integral Saturation
Integral Control Law: The controller employs an integral component in its PID logic.
Persistent Deviation: The input error signal remains uncorrected over an extended period.
Open-Loop Operation: The feedback loop is broken, and the integral action continues accumulating error unnecessarily.
3.3 Consequences
Loss of control responsiveness
Prolonged recovery time once the system returns to closed-loop
Risk of overshooting or instability when normal operation resumes
4. Methods to Prevent Integral Saturation
To maintain effective control and system stability, several methods can be used to prevent integral saturation:
4.1 Output Limiting (Integral Windup Protection)
This method restricts the range of the integral output to prevent it from exceeding controller output limits. Many modern controllers (e.g., Type II or Type III electric controllers) come with built-in output limiting mechanisms.
Example: A digital controller limits the integral term to ±20% of the full-scale output.
4.2 External Feedback (Anti-Windup Feedback)
During open-loop operation, an external signal is fed back to the integrator to “reset” or compensate for excessive integration. This feedback prevents the accumulation of unnecessary integral action.
Benefit: The controller’s output stays closer to realistic control values, allowing smoother return to closed-loop operation.
4.3 Integral Cutoff (Integral Hold or Freeze)
When the control system enters an open-loop mode or manual operation, the integral action is temporarily suspended or held constant. Once closed-loop control resumes, the integral component reactivates from the held value.
Implementation: Most modern DCS or PLC systems offer this feature as a configurable option in PID function blocks.
5. Conclusion
Selective control systems provide a dynamic and intelligent method for managing industrial processes under both normal and abnormal conditions. By proactively switching control logic based on real-time process variables, they ensure safety and stability without operator intervention.
Additionally, understanding and mitigating integral saturation is critical for ensuring consistent controller performance. By implementing anti-windup techniques such as output limiting, external feedback, or integral hold, engineers can enhance the robustness and responsiveness of control systems.
These advanced control strategies, when applied effectively, contribute significantly to process optimization, safety, and reliability in modern industrial automation.