The commissioning of a Distributed Control System (DCS) is a critical and complex task that requires careful preparation and attention to a number of factors. For a smooth and successful commissioning process, the following key conditions must be met:
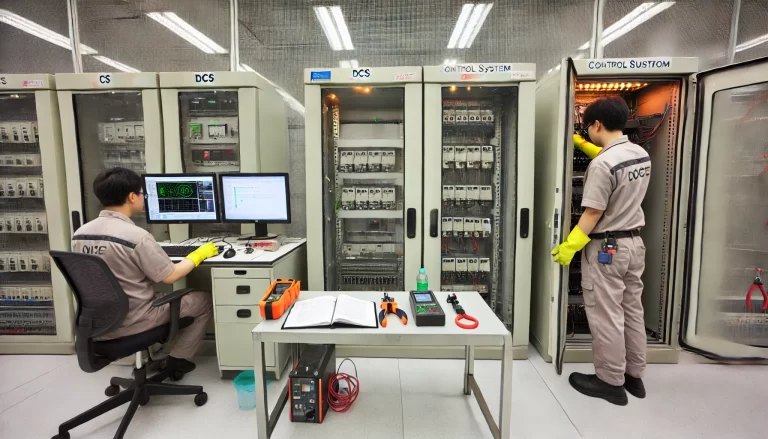
1. Hardware Requirements
1.1. System Installation
The DCS cabinets must be installed according to the design specifications, ensuring they are correctly positioned. The cabinets should meet the required vertical and horizontal alignment standards and be securely fixed.
All hardware components, including control stations, operator stations, and engineer stations (such as the host computers, monitors, keyboards, and mice), must be properly installed and connected. It is essential that the internal boards and cables are correctly connected, with no loose connections.
1.2. Power Supply System
The power supply system must be fully installed and operational. This includes a dual power supply with automatic switching capability. The system should be equipped with redundant power sources to ensure uninterrupted operation.
The voltage and frequency of the power supply should meet the specifications of the DCS equipment, with permissible fluctuations within specified limits (typically 220V ± 10% and 50Hz ± 1Hz).
The grounding system for the power supply must be checked, and the grounding resistance should be within acceptable limits. Normally, the resistance should be less than 4Ω, though for some systems, more stringent requirements (e.g., less than 1Ω) may apply.
1.3. Network Connectivity
Internal communication networks, such as redundant industrial Ethernet networks and process networks (e.g., Profibus, Modbus, etc.), should be fully wired and connected. Ensure that cables (e.g., network cables, fiber optics) are intact and not damaged.
Network switches, hubs, and other devices must be installed and configured, with all communication links thoroughly tested. A tool such as the “ping” command can be used to verify network connectivity between devices.
1.4. I/O Channel Check
All input/output (I/O) cards must be correctly installed in the appropriate slots within the cabinets, and their models should match the design specifications.
Ensure that the connections between I/O channels and field devices (e.g., transmitters, actuators) are secure and correctly wired, with no errors in polarity.
Each I/O channel must be tested to ensure that it is free of short circuits or open circuits. Using simulation signals for input/output can help verify the card’s ability to collect and transmit data.
2. Software Requirements
2.1. Operating System and Driver Installation
The operating systems on all workstations, engineer stations, and control stations must be installed and compatible with the DCS system. Ensure that the correct OS versions are used to avoid compatibility issues.
Hardware drivers (e.g., network cards, serial port drivers) must be installed to ensure the computers can properly communicate with and control the relevant hardware devices.
2.2. DCS Configuration Software Installation
The DCS-specific configuration software should be installed on the engineer’s station. Verify that the software version is compatible with the system requirements and is properly licensed.
The initial system configuration, including the definition of control strategies, creation of graphical user interfaces, and database setup, should be completed. This configuration should undergo a preliminary review to ensure that the logic is correct and no errors are present.
2.3. Communication Protocol Setup
For communication with field devices (e.g., Modbus, Profibus), the required settings such as baud rate, data bits, and parity must be configured within the DCS system. This ensures that the DCS can communicate effectively with the devices.
Interfaces for communication with third-party systems (e.g., PLCs, smart instruments) should be configured and tested to ensure proper data exchange.
3. Site Conditions
3.1. Process System Conditions
All process equipment connected to the DCS system must be installed and undergo initial commissioning. For example, motors should be able to start and stop correctly, valves should open and close as required, and the status and control signals should be accurately communicated back to the DCS.
Piping installations, including flushing and pressure testing, must be completed without any leaks. The field instruments (e.g., temperature sensors, pressure transmitters) should be installed, calibrated, and verified to ensure accurate measurements.
3.2. Environmental Conditions
The environment in the DCS control room should be within specified temperature (typically 18°C to 28°C) and humidity (40% to 70%) ranges to ensure optimal operation of equipment.
The control room should be clean and free from dust, oil, or other contaminants, with proper ventilation to support heat dissipation from the equipment.
Effective measures for fire, water, and static electricity protection should be in place to prevent any environmental factors from damaging the DCS system.
4. Personnel and Documentation Conditions
4.1. Qualified Personnel
- A dedicated commissioning team must be assembled, consisting of engineers familiar with DCS systems, technicians experienced in field commissioning, and process specialists. All personnel should be well-trained in the system’s principles, configuration methods, and commissioning procedures.
4.2. Complete Documentation
The DCS design documentation, including system configuration diagrams, network topology, I/O lists, control logic diagrams, and screen design layouts, should be fully available for the commissioning process.
Equipment manuals, operation guides, and maintenance documentation should also be on hand to support the commissioning work.
A detailed commissioning plan must be in place, outlining the procedures, methods, quality standards, and safety considerations. This plan should be reviewed and approved to ensure that the commissioning process proceeds smoothly.
Conclusion
Successful commissioning of a DCS system relies heavily on meeting all these critical conditions. The hardware installation, software configuration, site readiness, and personnel preparation must all align for the system to operate correctly. By ensuring that each of these conditions is met, and by adhering to a well-defined commissioning process, you can help guarantee a smooth and efficient startup, ensuring the DCS system performs as expected.