Abstract
In the field of industrial automation, Programmable Logic Controllers (PLC), Distributed Control Systems (DCS), and Supervisory Control and Data Acquisition (SCADA) systems are three pivotal technologies. While they share some overlapping functions, their technical characteristics and application scopes differ significantly. This article provides an in-depth comparison of these systems, highlighting their unique features, advantages, and suitable use cases.
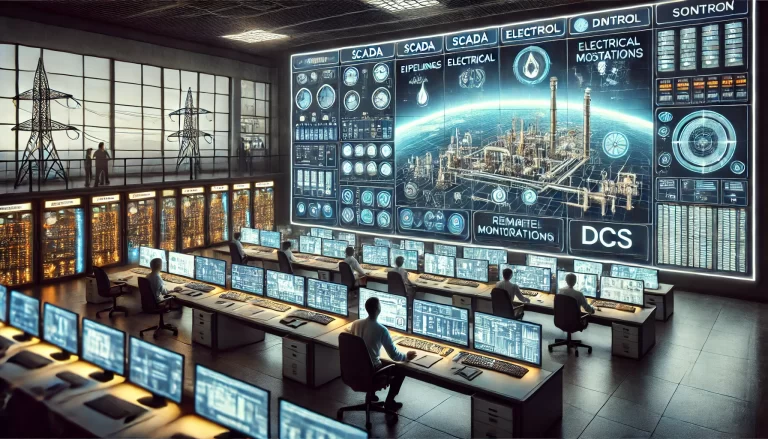
1. Programmable Logic Controller (PLC)
A Programmable Logic Controller (PLC) is a digital computer specifically designed for industrial automation to control machinery, production lines, and other automated processes. PLCs are renowned for their high flexibility, real-time processing capabilities, and ease of programming. These controllers are ideal for applications requiring rapid responses and adaptable control logic, such as assembly lines, packaging machinery, and robotic operations.
Key Features:
Flexibility: Easily reprogrammable to adapt to varying control tasks.
Real-time Operation: Capable of executing tasks with minimal latency.
Scalability: Suitable for both simple and complex control systems.
Durability: Designed to withstand harsh industrial environments.
Applications:
Manufacturing and assembly lines
Packaging and material handling systems
Automated warehouse management
2. Distributed Control System (DCS)
A Distributed Control System (DCS) is engineered for complex and high-demand process control. It employs a decentralized structure where multiple controllers are networked to manage different subsystems. DCS is predominantly used in industries like chemical processing, power generation, and oil refining, where continuous process control and data integrity are paramount.
Key Features:
Distributed Architecture: Decentralized control nodes enhance reliability and scalability.
Advanced Process Control: Supports complex control algorithms and multi-variable control.
Integrated Operator Interface: Provides real-time data visualization, analysis, and reporting.
High Reliability: Ensures minimal downtime with redundancy and fault-tolerant design.
Applications:
Chemical and petrochemical industries
Power plants and energy generation
Pharmaceutical manufacturing
3. Supervisory Control and Data Acquisition (SCADA)
SCADA systems focus on remote monitoring, data acquisition, and centralized control of industrial processes. They collect data from various field devices like sensors and actuators and provide operators with real-time monitoring, alarm management, and historical data logging. SCADA is primarily utilized in infrastructure management across large geographic areas.
Key Features:
Remote Monitoring: Enables centralized supervision over wide areas.
Data Visualization: Offers user-friendly dashboards and graphical interfaces.
Alarm Management: Provides timely alerts for abnormal conditions.
Integration Capability: Can seamlessly integrate with PLCs and DCS for comprehensive control.
Applications:
Water supply and wastewater management
Electrical power distribution grids
Transportation systems (e.g., railways, traffic control)
4. Key Differences Between PLC, DCS, and SCADA
Feature | PLC | DCS | SCADA |
---|---|---|---|
Architecture | Centralized | Distributed | Centralized with remote access |
Control Focus | Discrete, sequential control | Continuous, process control | Monitoring and supervisory control |
Scalability | High for local systems | High for complex, large-scale systems | High for geographically dispersed systems |
Response Time | Fast, real-time | Moderate to fast | Varies, focused on monitoring |
User Interaction | Minimal, mainly for maintenance | High, integrated operator interfaces | High, real-time dashboards |
Typical Industries | Manufacturing, assembly lines | Chemical, power generation | Utilities, infrastructure |
5. Integration in Industrial Automation
In modern industrial environments, PLC, DCS, and SCADA systems are often integrated to maximize efficiency, reliability, and scalability. For instance, PLCs might handle fast, localized control tasks within a broader DCS framework, while SCADA systems provide centralized monitoring and management. This layered approach enables industries to achieve robust, adaptive, and comprehensive automation solutions.
6. Conclusion
PLC, DCS, and SCADA systems each serve distinct roles within industrial automation. PLCs excel in high-speed, discrete control tasks, DCS systems are ideal for continuous and complex process control, and SCADA systems specialize in remote monitoring and data management. By understanding the strengths and limitations of each system, industries can effectively deploy integrated solutions tailored to specific operational needs.
References
Kumar, A., et al. (2020). Advanced Automation in Industrial Applications. Industrial Engineering Journal.
Sharma, R., & Singh, P. (2021). Distributed Control Systems: Design and Application. Process Automation Review.
Lee, H., & Kim, S. (2019). SCADA Systems and Modern Industrial Control. Automation Today.