Flanges are vital components in piping systems, enabling the connection of pipes, valves, pumps, and other equipment, providing easy access for cleaning, inspection, or modifications. Their correct selection, installation, and maintenance are critical to ensuring the safety, efficiency, and longevity of industrial systems. This article presents a comprehensive overview of flanges, focusing on their definition, classification, materials, application in instrumentation, and essential installation and maintenance practices.
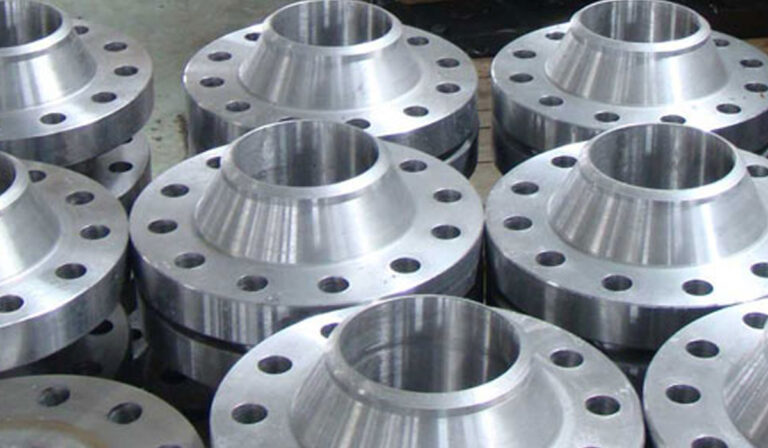
1. Definition and Basic Structure of Flanges
A flange is a mechanical part used to connect pipes, valves, pumps, and other components within a pipeline system. Typically, a flange consists of three parts: the flange disc (or ring), a gasket, and bolts and nuts. The flange disc features bolt holes, through which bolts secure two flange discs together. The gasket, sandwiched between the two discs, ensures a tight and leak-proof seal, preventing any fluid or gas from escaping.
Flanges are essential in allowing disassembly for inspection, cleaning, or maintenance, while maintaining the integrity of the system under pressure.
2. Classification of Flanges
Flanges are classified based on their connection method and the type of sealing surface.
By Connection Method:
Slip-on Flange: This is the most common type of flange. It is welded to the pipe through a fillet weld. Slip-on flanges are simple to manufacture and lower in cost but are generally used for medium- and low-pressure applications due to their lower strength. They are suitable for fluid transportation systems in chemical plants.
Weld Neck Flange: This flange type has a long neck that is butt-welded to the pipe, offering higher strength and rigidity compared to slip-on flanges. It is ideal for high-pressure and high-temperature applications and is commonly used in steam pipelines in petrochemical plants.
Socket Weld Flange: In this design, the pipe is inserted into a socket on the flange and then welded. This type is used for small-diameter pipes, offering better sealing performance. It is suitable for pipelines with a pressure rating of PN≤10.0MPa and a diameter of DN≤40mm.
Threaded Flange: This flange has an internal thread and is connected to a pipe with matching external threads. It is often used in low-pressure systems or where welding is impractical, such as in instrument air lines.
By Sealing Surface Type:
Raised Face (RF) Flange: This flange type features a raised flat sealing surface. A gasket is placed on the raised area, and the seal is achieved by tightening the bolts. Raised face flanges are the most commonly used type and are suitable for medium- and low-pressure environments.
Male and Female (MFM) Flange: These flanges feature one concave and one convex surface, with a gasket placed in the concave area. This design prevents the gasket from being extruded under pressure, making it suitable for medium- to high-pressure systems.
Tongue and Groove (TG) Flange: The sealing surface is composed of a tongue on one flange and a matching groove on the other, with the gasket installed in the groove. This offers superior sealing performance, especially for high-pressure pipelines carrying flammable, explosive, or toxic media.
Ring Joint (RJ) Flange: The sealing surface is shaped like a trapezoidal groove, where a metallic ring gasket is compressed to create the seal. RJ flanges are designed for use in high-pressure and high-temperature systems, such as hydrogenation units in refineries.
3. Flange Materials
Flanges come in a variety of materials, selected based on the working environment, pressure, temperature, and the nature of the fluid being transported. Common flange materials include:
- Carbon Steel (e.g., Q235B): Suitable for general-purpose pipelines.
- Stainless Steel (e.g., 304, 316): Ideal for corrosive environments, such as chemical processing pipelines.
- Alloy Steel (e.g., 15CrMo, 12Cr1MoV): Used in high-temperature and high-pressure applications, such as power generation and petrochemical industries.
The material choice is critical to the flange’s longevity and performance, especially in environments with corrosive chemicals or extreme conditions.
4. Application of Flanges in Instrumentation
Flanges are crucial in connecting various instruments to pipelines, especially in measuring and monitoring fluid and gas properties.
Pressure Instrumentation: Devices like pressure transmitters and pressure gauges often use flanges to connect to pipelines and measure the internal pressure of fluids. The choice of flange type and specification depends on the working conditions, including temperature and pressure. For example, weld neck flanges may be used in high-temperature steam systems to ensure strength and sealing.
Level Instrumentation: Instruments such as flange-mounted level transmitters use flanges for installation on containers or tanks, measuring liquid levels based on differential pressure. The accuracy of these measurements depends on the flange’s sealing performance, which in turn is determined by the sealing surface type and gasket material.
Flow Instrumentation: Flow meters, such as electromagnetic and vortex flow meters, often use flanges for connection. The flange diameter must match the pipeline and the instrument to ensure smooth fluid flow and accurate measurement.
5. Installation and Maintenance of Flanges
Proper installation and maintenance are essential to ensure that flanges remain leak-proof and perform reliably throughout their operational life.
Installation Guidelines:
Before installation, verify that the flange specifications, including the material, size, and model, meet the design requirements. The sealing surface should be smooth, without any radial grooves or defects like pores.
Ensure high-quality welding when attaching the flange to the pipe. After welding, clean the weld area and flange surface, and conduct non-destructive testing if required.
The gasket should be correctly aligned, with the appropriate material and size for the application. Avoid gasket twisting or misalignment.
Bolts should be tightened symmetrically and evenly using a torque wrench to ensure uniform pressure distribution and prevent leaks.
Maintenance Recommendations:
Regularly inspect flange connections for leaks. If a leak is detected, first try tightening the bolts evenly. However, avoid over-tightening, as this can damage the gasket or flange.
Periodically check for gasket wear or damage, especially in systems that experience high pressure or temperature fluctuations. Replace worn gaskets promptly.
In environments with corrosive chemicals, inspect the flange for signs of corrosion. If defects such as corrosion pits are found, repair or replace the flange as necessary.
Conclusion
Flanges play an indispensable role in the integrity of piping systems, especially in industries where precise measurement and control of fluids are critical. Their selection, installation, and maintenance directly impact the efficiency and safety of pipelines and instruments. Whether used in low-pressure chemical lines or high-pressure steam systems, understanding the properties of different flange types, materials, and applications is essential for engineers and technicians working in various industries. With advancements in materials and design, the performance of flanges continues to improve, contributing to the overall reliability of industrial infrastructure.