Level is one of the four major thermal parameters in the process industry, along with temperature, pressure, and flow. Unlike a level meter, a level switch is a measuring instrument used to control the level. Although it cannot display or measure the level height, as an electronic component, it plays a key role in many fields.
Although this term is relatively unfamiliar in daily life, it is widely used and important. In order to help users better understand the level switch, this article will introduce the function, installation, maintenance and use guide of the level switch.
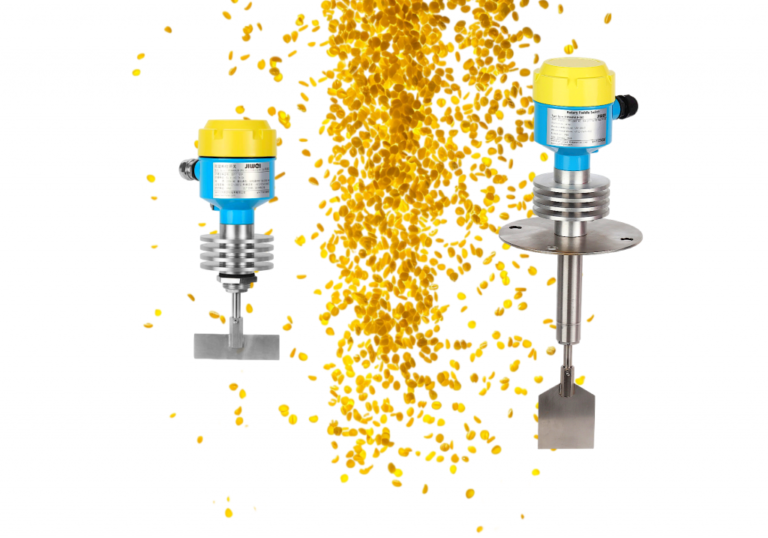
Introduction to Level Switches
Level switch, as a new type of level instrument, includes rotary paddle level switch, tuning fork level switch, vibration level switch, capacitive level switch, radio frequency admittance level switch and so on.
Level switches, depending on the measured level, mainly cover the liquid level, material level and the interface formed by different media due to different densities. They are used to monitor the upper and lower limits of the level and perform alarm or switch output and control.
Installation and Maintenance of Level Switches
When installing and maintaining the level switch, pay attention to the following points:
1. Avoid installing it near the material inlet.
2. When the particle diameter is greater than 15mm or the installation is less than 7 meters from the lower part of the feed inlet, a probe protection baffle should be added to protect the probe.
3. When measuring powders with high viscosity, the probe should be inserted vertically downward from the top of the container or obliquely downward from the side wall to reduce the phenomenon of hanging material.
4. When the probe is used in working conditions where the temperature exceeds 120°C, it will affect the service life of the piezoelectric element, so the switch action should be checked regularly to see if it is normal.
5. When wiring in and out, pay attention to safety and do not wire with power on to prevent short circuits and burn the substrate or probe.
6. When working in a dusty environment, an explosion-proof level switch should be used, and a level switch with good sealing performance should be selected to keep the entire machine sealed.
Level Switch User Guide
1. Probe length: The probe length is the distance from the front end of the mounting thread to the front end of the probe. When ordering an extended probe, the probe length is the above distance.
2. Output wiring: The output indication is the output when the output conversion switch is in the “NC” position. When it is in the “No” position, the normally closed end and the normally open end are interchanged.
3. Instructions for use:
1) Switch settings before use: ① Set the “OUTPUT” switch to “NC”.
② Turn the sensitivity knob right to the high sensitivity “HIGH” position.
2) Power-on test and debugging: ① After the power is turned on, the red light is on and the relay is closed. After about 5 seconds, the probe vibrates, the red light goes out, and the relay is open (when the “OUTPUT” switch is set to “No”, the state is the opposite). Touch the front end of the probe with your hand, the red light is on, leave, and the red light goes out in 1~2 seconds.
② The sensitivity selection can be adjusted according to the material before installation, but for general materials, it can be placed in the “HIGH” position without debugging (this should be stated when ordering the liquid level switch).
③ When the operating temperature is high, choose the lowest “LOW” sensitivity as much as possible while ensuring accurate measurement.
3) Measurement: ① When the probe contacts the material, the probe stops vibrating, the red light turns on, and the relay closes (the state is opposite when “No”).
② When the material leaves the probe, 1~2 seconds later, the probe vibrates again, the red light turns off, and the relay opens (the state is opposite when “No”).
4) Terminal block: The output indicated by the output operation panel is the output when the “OUTPUT” switch is set to “No”.
Conclusion
With the continuous improvement of industrial automation production level, the role of level switches is becoming increasingly important.
It can accurately detect changes in the measured objects in the equipment, helping operators to make production adjustments according to actual conditions, thereby improving production efficiency and work quality.
In the pharmaceutical, petroleum and other industrial fields, vibration level switches and radio frequency admittance level switches play an important role.
In recent years, with the rapid development of discrete control technology, some simple level switches are sufficient to solve common problems.
However, due to the diversity of working conditions, it is very important to choose a suitable level switch. Whether the level switch is selected correctly directly affects its reliability and accuracy in practical applications.